Any maintenance strategy must include preventive maintenance. It’s essential for minimizing maintenance costs, cutting downtime for equipment, extending the lifespan and efficiency of assets, and boosting worker safety.
In this article, we will see why preventative maintenance is important, discuss how to design the best preventive maintenance plan, and how to use it so your companies can stay on top of any potential problems.
Preventive Maintenance: What Is It?
Building maintenance that has a proactive approach and is focused on preventing problems is known as preventive maintenance (PM). It entails routine checks as well as targeted maintenance and repairs to the building’s equipment at predetermined intervals.
Preventive maintenance aims to extend equipment life expectancy and avoid equipment failure, minimizing unscheduled downtime and lowering total maintenance costs by fixing errors as soon as they are discovered, and before they become major issues.
Do not confuse preventive maintenance with predictive maintenance (PdM).
Predictive maintenance uses advanced analytical data which most of the time is gathered through sensors or through assets run to the failure life span that’s calculated by manufacturer/industry historical trending data and involves work performed based on the state of a system or component, as opposed to maintenance carried out at predetermined intervals, but we’ll cover more differences later on in this article.
Why do you need a preventive maintenance program?
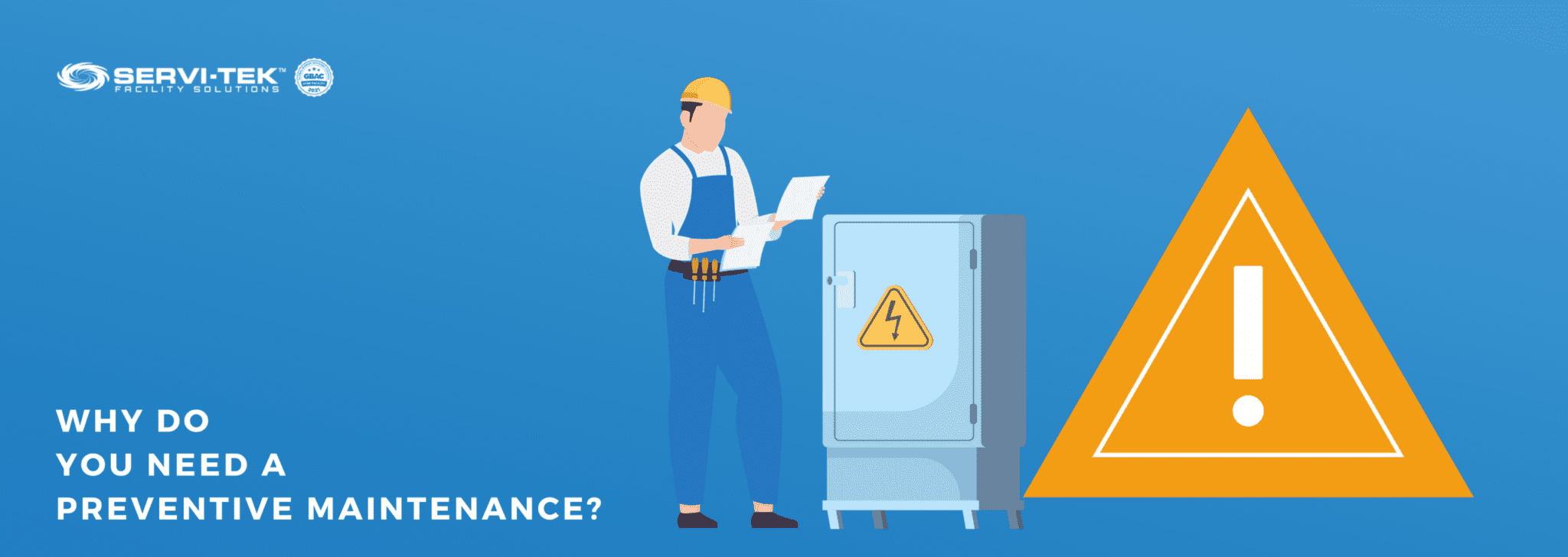
A preventive maintenance program for the most part starts with a maintenance schedule which helps with task organization and prioritization, enabling the maintenance teams to repair the equipment to its best possible functioning condition and ultimately leads to extending its lifespan. In recent years, more and more managers realize the importance of having this program set up and implemented.
You can make sure your equipment continues to run safely and efficiently by doing routine maintenance.
When working with a lot of equipment, keeping a good PM schedule can be very difficult to manage, thus maintenance technicians frequently benefit from the use of some form of maintenance software which can help with scheduling and organizing PMs from most critical to least critical and can help with organizing tasks within each PM.
The benefits of preventive maintenance are:
- Extend the life of the asset: Keeping your equipment in good shape enables it to run longer, lowering costs;
- Reduce the risks of failures: Your facility runs the risk of loss of production and possibly a damaged reputation if you wait until something goes wrong and are reactive;
- Boost performance: Equipment that receives regular preventive maintenance not only lasts longer but also operates more effectively;
- Reduce unscheduled downtime: By planning maintenance work ahead of time using a preventative maintenance strategy, downtime can be considerably decreased;
- Encourage safety and health: Utilizing a computerized maintenance management system (CMMS) to track preventative maintenance will enable you to manage all of the equipment in your business and save vital asset data in one central location;
- Increase client satisfaction: with proper preventive maintenance, a facility can ensure comfort heating and cooling is properly maintained and productivity is never lost for instance, due to a broken-down HVAC unit. Also, with a proper program, it can help in preventing the breakdown of equipment and maintain the quality of the goods produced;
- Save money: Typically, unplanned maintenance costs 3 to 9 times as much as scheduled maintenance.
When calculating for Emergency reactive maintenance it’s important to note one must account for missed sales or productivity while the equipment is not in use, as well as the cost of expedited shipping for critical machinery parts.
Types of preventive maintenance
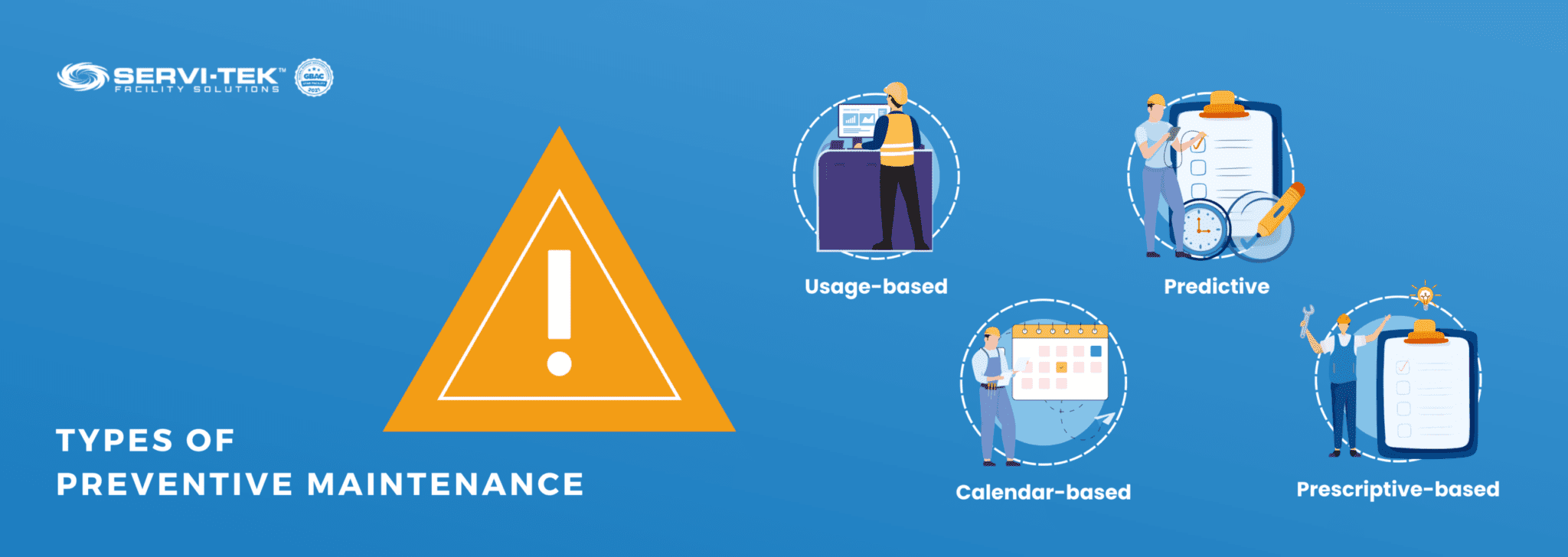
There are different types of preventive maintenance: four key categories to be more exact. Although they are all arranged and scheduled differently to meet various business operation needs, each is based on the idea of planned, regular maintenance.
Usage-based preventive maintenance
Actual asset use is what drives usage-based preventive maintenance strategy. This type of maintenance forecasts a future inspection or maintenance task’s due date by taking into consideration an asset’s typical daily usage or exposure to environmental conditions.
Calendar-based preventive maintenance
Preventive maintenance that is time or calendar-based is carried out at a predetermined time. When the due date approaches and the required work orders have been created, maintenance action is initiated.
Predictive maintenance
Predictive maintenance procedures are planned before a failure occurs. To estimate when maintenance should be carried out, the team must first assess the equipment’s condition. After that, maintenance personnel plans key actions to avoid any critical failure in the future.
Prescriptive maintenance
Prescriptive maintenance not only predicts when and where failure will occur but also explains why it is occurring. To reduce any danger to the operation, this sort of maintenance assists in the analysis and determination of various possibilities and probable results.
How to create a preventive maintenance plan
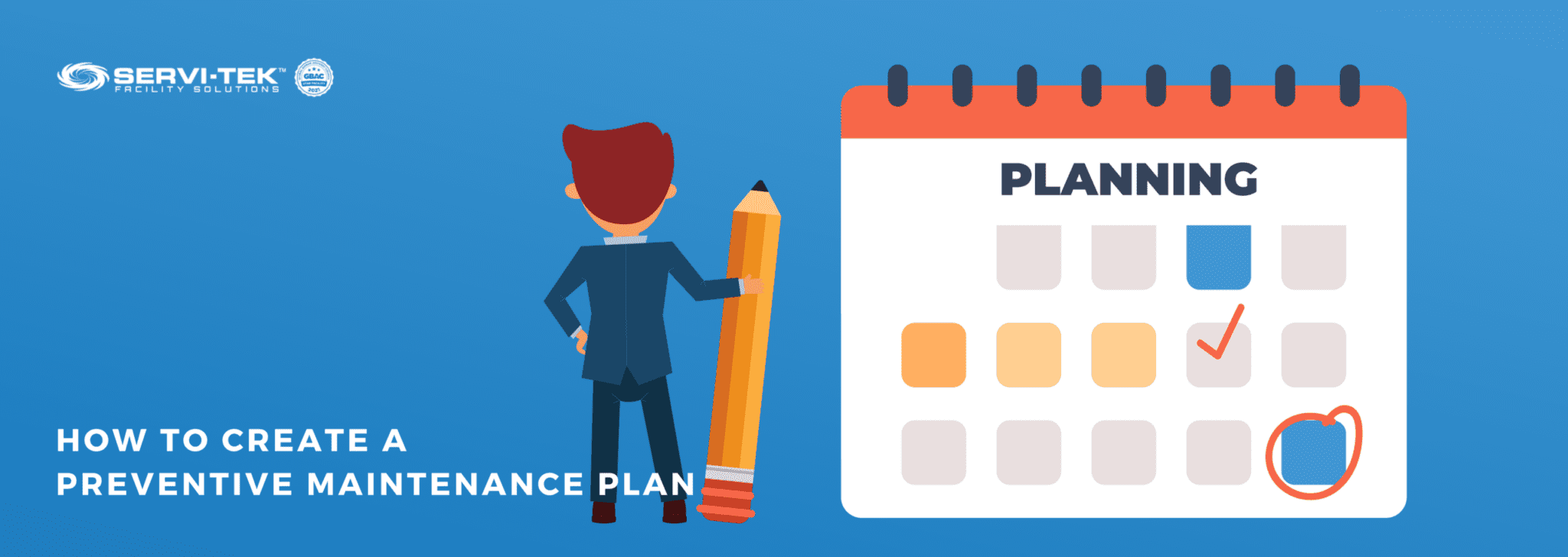
It’s not always recommended to schedule additional preventive or corrective maintenance. Preventive maintenance tasks performed merely to raise your planned maintenance KPIs can be expensive, a waste of time, and can result in breakdowns after repair.
A successful preventative maintenance program revolves around fine-tuning the frequency of maintenance so that you only schedule work when it’s essential.
Finding the ideal balance between performing a scheduled maintenance activity too frequently (expensive and unsafe) and insufficiently frequently (you’re likely to miss failures between inspections) is essential.
One of the best ways to improve your preventative maintenance schedule is to follow the below structure:
- Plan: Take a closer look at repairs history, criticality, equipment usage patterns, and equipment failure to establish a baseline for PM frequencies.
- Do: Stick to your plan to get accurate outcomes.
- Check: Evaluate the failure indicators for each asset to see if your strategy is effective.
- Act: Reduce the frequency of PMs if you are not detecting failures between PMs and increase the frequency if an asset is breaking down between maintenance activities.
What are the steps of a good preventive maintenance plan?
You’ll go through the following steps before the process is finished as you choose which components of your business and equipment to focus on for preventive maintenance.
1. Set priorities for your goals
Establishing your goals is the first step in developing a successful preventative maintenance program. Every facility has unique objectives, and those objectives guide all the following choices.
Would you like to cut downtime? Increase trustworthiness? Spend less money?
Make a comprehensive list of your motivations for setting up a structured PM program. It’s now time to prioritize your goals. Let’s face it, you’re constantly busy, and adding a preventative maintenance plan to your to-do list will be a major undertaking.
2. Establish KPIs and follow them
You should give numbers or a form of data to track your goals now that they are set up. Without having clear objectives, it might be difficult to determine whether a preventative maintenance program is effective, especially in the long term.
Common examples include the percentage of planned maintenance that is critical, the compliance with preventative maintenance, the overall piece of equipment efficacy, and the average time between failures.
You can easily calculate these parameters with preventive maintenance software, such as a computerized maintenance management system.
Create a strategy for routinely measuring these indicators once you’ve decided on the KPIs you’ll be utilizing to gauge performance. Statistics are only helpful if you regularly use them to enhance your preventative maintenance strategy.
Building processes and procedures that guarantee data is regularly collected, examined, and used is essential. You can then assess your progress toward your objectives and identify your areas of strength and weakness.
3. Use the right technology
One of the key components of a successful PM strategy is modern technology. You may effectively handle all the smaller preventive maintenance chores, such as scheduling, inventory maintenance management, reporting, and work order organization, that are necessary for your facility to adopt a PM attitude by utilizing a digital solution.
The moment has come to prepare for a switch to a digital solution if your facility still uses an old system, like Excel or pen and paper.
When selecting the best technology for a preventative maintenance program, there are several things you must consider, including your team’s skillset, your budget, the capabilities of your assets, your team’s preferences, historical data security, and more.
When looking for preventive maintenance technology, such as CMMS software, ease of use is among the most crucial considerations. A system won’t be used efficiently if it is too difficult to comprehend and use correctly, and all the effort and money spent developing the solution will be wasted.
4. Implement
Implementing your plan for preventive maintenance is the logical next step. If your team is unfamiliar with preventative maintenance, you can think about starting a pilot program at one location, one area of your plant, or with a select few assets.
In this approach, you can work out the kinks in your PM program while assisting your team in adjusting to a new way of doing things.
5. Build a preventive maintenance checklist to analyze the results
A final step is to prioritize inspection and keep an eye on the data after your preventative maintenance program is in action. A preventive maintenance checklist is crucial because it enables you to regularly monitor KPIs like the average time for necessary repairs, the percentage of planned maintenance, and the average time between failures.
You should be able to determine how your program is affecting the effectiveness of your maintenance operation by analyzing these statistics and comparing them to pre-plan values.
Join Forces with Maintenance Experts
Your employees might not have the time, knowledge, and authorization to conduct all required preventative maintenance tasks depending on how your organization is set up. Indeed, for enhanced quality, safety, and efficiency, many mandatory tasks are best handled by trained personnel. They know how to follow best practices, what works, and what doesn’t.
As a result, hiring specialized maintenance services to take care of things like commercial cleaning, servicing of equipment, plumbing, oil changes, HVAC, and more is a good idea and it pays off.
And it’s more cost-effective to work with a full-service facilities management business that completes everything on your timeline rather than hiring different agencies for each task.
Get started today with preventive maintenance
At Servi-Tek Facility Solutions, our team of highly trained specialists has the knowledge and skills necessary to analyze and fix a wide range of facility operational issues.
We can service any kind of janitorial cleaning equipment or help with onsite building engineering while following the latest industry standards. Our scheduled maintenance and service plans will help to ensure that your equipment performs at its best when you need it, saving you time and money and ultimately enhancing the bottom line of your company.
Get in touch with us today!