Variable frequency drives (VFD) are widely-used to heighten the efficiency of electric motors used in different appliances and compressors.
The enhancements in efficiency result from handling energy at certain frequencies and voltages that control and optimize output.
But what’s behind Variable Frequency Drives and how will this help your business? Read all about it here.
What Are Variable Frequency Drives?
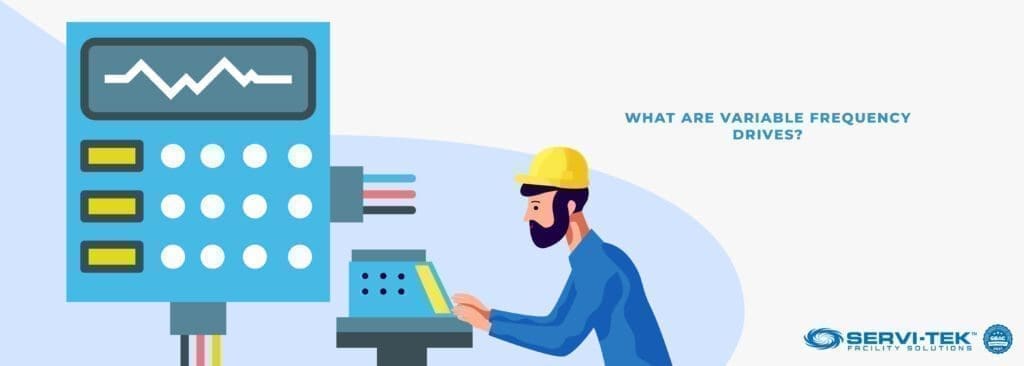
VFDs are controllers of electric motors that use variations in voltage and frequency. Frequency is expressed in hertz (Hz) and it correlates with the speed of a motor in RPMs.
In recent years, VFDs have become smaller yet more capable of performing through integration with continually evolving technologies.
As with the majority of markets in 2020, the pandemic had a significantly negative impact on the variable speed market.
VFDs are now deployed across most applications in industrial settings. Commonly referred to as variable speed drives, VFDs have proven to be both sustainable and adaptable to market changes.
VFDs are used to meet the user’s goals and needs by effective torque control, motor speed, loads, and much more. AC motors have long been used for driving fans, pumps, blowers, and conveyors to boost performance and save energy.
In many types of applications, an electric motor doesn’t need to operate at full speed. For example, the VFD might be used to bring down a motor’s load by reducing frequency and voltage.
Aside from simply increasing or decreasing the speed of a motor, drives now feature enhanced diagnostic and networking options. Many of these improvements have proven to be economical while also boosting productivity and overall performance.
Intelligent motor control has recently emerged as a solution for reducing costs by lowering the current draw during peak periods. Today’s most common uses include managing cycles of compressors, fans, pumps, and related components.
Another core application today involves regulating the speed of compressors used in refrigeration, which involves cooling. This application of VFD use replaced traditional fixed compressors that were in an on or off mode.
Manufacturers of VFDs are improving aspects of their products including inverters, switches, transistors, diodes, capacitors, and adjustable frequency drives.
The market is segmented by drive type, input and output voltage, and the categories of end-users.
Some of the key VFD attributes include horsepower, full load amps (FLA), voltage, RPMs, and whether the unit is inverter rated. VFDs may have variable torque loads or constant torque loads, have various methods of control, and require special enclosures.
The voltage of a VFD should correspond to the motor, which for lower voltage will include 208, 230/240, or 460/480 VAC. One of the key VFD thresholds is whether the load is less than or greater than 3 HP.
The Basics of a Variable Frequency Drive
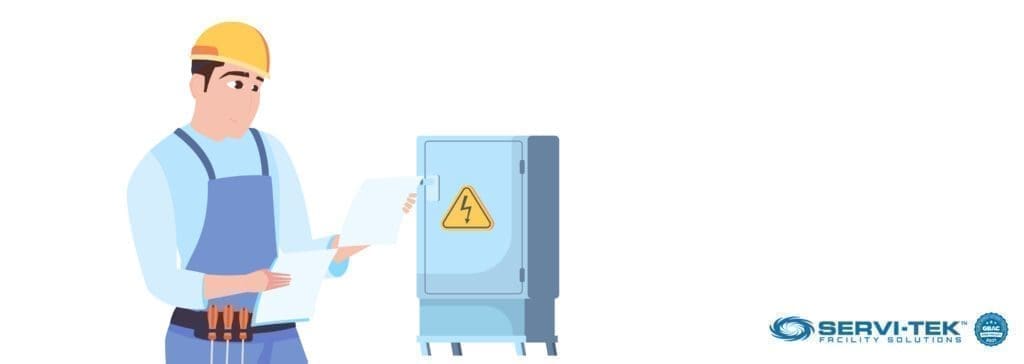
To gain a reasonable understanding of how a VFD operates it is important to comprehend the basics of electricity. Much of this involves understanding alternating current (AC) power and direct current (DC) power.
DC power describes an electrical current that operates in a straight line or in a linear way like a river. It is sourced from various things including solar or fuel cells, batteries, and some alternator varieties.
DC may also be created by converting AC power through a rectifier, and it is typically seen as more reliable and consistent and the majority of electronic devices depend on it.
The current source inverter, often referred to as a current fed inverter can convert DC into AC. A transformer also might be used to increase or decrease DC voltage.
Some types of devices do not operate on DC such as various household appliances like washing machines. Here, the power outlets connect directly with the grid to deliver AC power.
AC power is traditionally the current from power outlets and has a flow that will change directions. Here, electrons influence the flow and cause a switch from positive to negative.
A sinusoidal AC waveform occurs at power stations when alternators use a loop and a magnetic field to generate AC. As the wire moves to different areas of magnetic polarity, a current can travel in the opposite direction.
AC power can carry much further compared to DC because of its waving motion, which is critical in reaching outlets. In the meanwhile, DC power is preferred based on its even flow and voltage.
Both AC and DC are needed in modern electrical systems, with AC being the current that distributes. Upon arriving at the source, such as your business, AC may be transitioned to DC.
The Basic Components
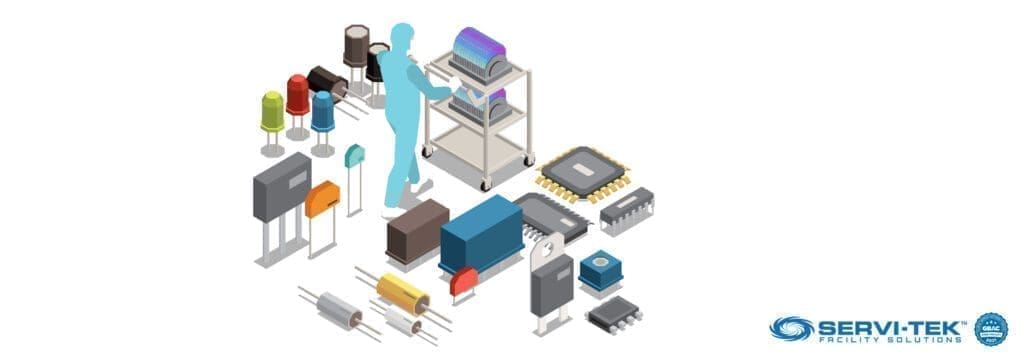
VFD can be divided into two sets—the power stage and the control circuit.
The power stage of a VFD may involve converting AC to a Variable Voltage Variable Frequency (VVVF) output for a motor.
Here, rectifiers, DC bus capacitors, and IGBTs handle the conversion of voltage. The control unit then must dictate what reaches the motor.
These systems use configurations of analog, digital, and relay inputs and outputs, each with different purposes. For example, based on the incoming voltage, an analog input might be needed to achieve optimal speed.
A VFD circuit (solid-state) could be described as having three distinct parts as follows:
- A three-phase bridge rectifier, which might be simply called a rectifier or converter module;
- A segment containing filter components, which might be referred to as simply an intermediate section;
- A segment where the DC link is reversed into three-phase AC or the inverter section.
The rectifier is potentially susceptible to dangerous surges of voltage; therefore, varistors might be connected for protection. The intermediate or filter section contains capacitors and an inductor.
The DC bus is connected to capacitors, which leads to an inductor and negative DC bus wire. Resistors are components responsible for capacitor-discharge, which occurs when power is not passing through.
Next, filters alter DC voltage that is pulsing to standard DC for reverting it to three-phase voltage. Pulse width modulation (PWM) refers to processes that work with transistors to facilitate the transition to three-phase.
The VFD board will transmit PWM signals. VFDs today are generally equipped with microprocessors that collect incoming signals and alter frequency and voltage accordingly.
Applications
VFDs are used in most fields and industries where demand exists for managing speeds and torque in motors. Machine tools, pumps, blowers, and conveyors generally will rely on a VFD-driven AC motor.
VFDs may be used for controlling the speed of a conveyor by having technicians manually adjust a remote potentiometer. A potentiometer will allow for changing speeds and is defined as an instrument that divides voltage and measures electromotive forces.
Here, the cycle speed of the motor that a VFD control has parameters that are programmed—minimums and maximums. Both “general purpose” VFDs and vector control applications have reference tables that guide a technician.
A general-purpose VFD may use automation to achieve energy savings by increasing or decreasing the amount of pressure of air. Often, the volume of airflow or intensity of the pressure is adjusted for the time of day, seasonal variations, etc.
Aside from improving the efficiency of a machine, a VFD might allow for deploying a smaller-sized machine. This might apply in larger systems that involve fans used in cooling towers or used in drying machines.
Depending on the needs, an operator might adjust the speed of a rotor such as for the deceleration of a pulley. Programming is increasingly automated for regulating conveyor speed and having the system stop at certain locations.
Vector variable frequency drives (vector control) provide high power factors that produce torque without large speed changes. This is beneficial when machines are used for injection molding, drawing wire, agitation, or extrusion work.
Here, these capabilities are useful when powerful starting torque is needed to account for braking, such as in multilevel automobile parking.
Another common application applies to operations involving centrifugal pumps, which are mechanical and operate by moving fluids. This is effective because a VFD can adjust frequency and voltage to regulate speed, horsepower, and torque.
Operations in the mining industry have increasingly adopted VFDs for use with crushers that are processing stone. VFDs help mining operations that were traditionally hindered by ongoing maintenance and adjustments needed to account for encountering different materials.
Manufacturers
VFD manufacturing has continued to evolve for decades to use mechanical or electrical options for dictating speed.
The motors are dependent on the capability of several poles (stator) and frequency to control speed.
In the 1950s, manufacturing predominately focused on mechanical devices for speed control and the machines were large by today’s standards. The Energy Policy Act of 1992 rejuvenated VFD manufacturing by implementing policies geared toward conserving power and maximizing efficiency.
New standards regarding energy applied to all motors manufactured beginning in 1997, based on National Electrical Manufacturers Association (NEMA) provisions. These standards applied to the vast majority of motors with exclusions only for special-purpose AC motors and certain DC models.
In the decades since technology has played a more integral role in the further development of VFDs for more applications. VFDs now not only save energy but also enhance product quality, reduce costs of production, and have many other benefits.
Inverter duty motors remain largely a separate market from those specifically designed for maximum efficiency.
In recent years, manufacturers have been making their VFDs more appealing to those operating in the oil and petroleum sectors.
Many experts feel that these and similar industrial sectors could generate up to 10% in compound annual growth.
Manufacturers in China are making progress in the market of VSDs, which comparatively entered this realm of production much later. The recent market and redevelopment of VSDs in China have been averaging increases of nearly 20% each year.
The Chinese government seems to support production and variable speed drives can also help to reduce carbon emissions. The manufacturers involved in VFD production range from small specialty organizations to larger companies with an international presence.
When To Use a VFD
When assessing the potential benefits of implementing a VFD, managers might conduct a simple cost and benefit analysis. For example, those considering a VFD for regulating a centrifugal pump motor often find that they are a viable solution.
Here, a centrifugal pump motor of the rapid power changes involved with these machines. The pump speed can be decreased, which also lessens flow and pressure; however, the power consumption drops much more dramatically.
Managers considering VFDs often assess the following factors:
- Conditions for operation: Specification of the minimum and maximum requirements and runtime at varying speeds;
- Installation-related expenses: Aside from the initial installation, often there are additional equipment needs for noise filtration, high power factor corrections, etc.;
- Likely savings: Assessment of the annual savings from operating the motor at slower speeds, which is based on KWH estimates. Keep in mind that maintenance costs should drop and the motor may have a longer serviceable life.
Once these and other similar variables are calculated, the answer of whether to move forward is likely to be apparent.
Safety Considerations
As with most aspects of commercial and industrial operations, there are potential safety concerns that must be addressed. For example, determining if modifying the machine’s control system by adding a VFD poses any risks.
The perceived or anticipated risks might be mitigated to some extent if protective measures are also implemented. When assessing risk, often it is encouraged to consider the tolerance level assuming that the machine is misused by an operator.
In situations where the findings represent an excessive level of risk, then major design or application changes are necessary. Many manufacturers have assessed potential safety concerns and created additional systems and functions that provide safeguards.
One type of functional safety change involved locking guards and similar control devices that reduce risk. Managers will typically create a safety requirement analysis considering any number of potential risks.
Types of Drives
There are a host of common drives as follows:
1: Direct Drive
A direct conversion drive takes AC power and converts it to variable AC in a single stage. This is most common using a cyclo-converter that controls a synchronous motor where speeds are low and torque needs are high.
A key drawback to direct conversion drives is the likelihood of harmonic currents that enter the circuit and network. Newer techniques and directional switches are expected to continue developing and allow operation with the lower harmonic current.
2: 3 Phase Advance and Phase Shifting
Motors exceeding the size for VFDs built for phase conversion may consider a standard drive for a single-phase supply of power. Here, the AC input has two hot wires with one connected to the VFD and the other unused or open.
Using this configuration, the amperage is concentrated on two phases rather than three, which may create diode failure. In this application, a VFD is chosen that is oversized and can handle the increased ampacities.
For example, assuming a given motor is rated at 15 FLA, the VFD to choose is one rated to handle 30-amp. One potential problem involves the inability of the VFD to handle the power conversion needed for running peripheral devices.
3: Phase Compensation
Sensorless control configurations may allow for more function. For example, slip compensation will handle the “slip,” which is the difference between actual speed and reference speed.
The device might have an Operation Mode that enables slip compensation automatically by altering speed and stator frequency. Slip compensation may also be manually activated in the absence of such capabilities.
Uses in HVAC Systems
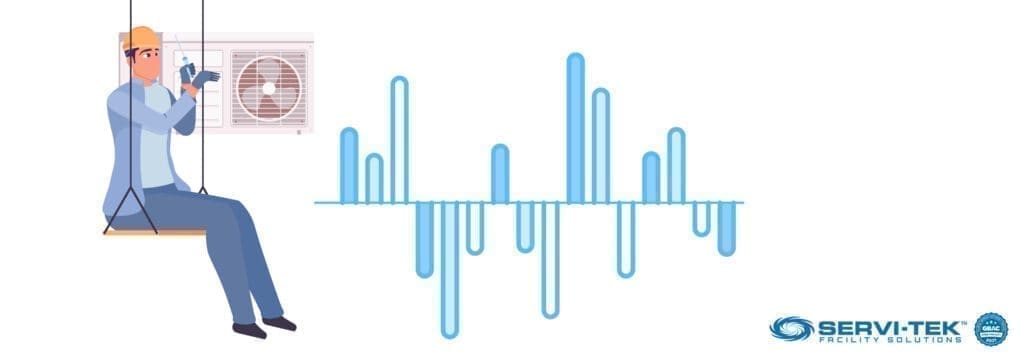
Heating, ventilation, and air-conditioning (HVAC) systems are created for peak load operations, as needed during certain periods each year. A VFD can be used to maximize energy efficiency for compressors, pumps, etc.
HVAC systems are often Single-zone Variable Air Volume (VAV) systems that use outdoor air, return dampers, filters, coils, and fans. Many configurations use a bypass damper, a fan for driving return air, and coils for preheating.
Single-zone systems are generally designated to manage the temperature levels in one space based on a set point. Regulating the speed of fans in conjunction with coil valves for heating and cooling is effective in reaching supply air temperatures.
The 2010 ASHRAE update required a water-cooled coil and supply fan units of 5 hp to have two-speed motors or VFDs. This also applied to those with direct-expansion (DX) cooling coils and capacities of 110,000 Btu/h.
Among the most common are single-duct VAV systems (SDVAV) with outdoor air dampers, coils, and safety components. Dampers or “duct dampers” may be opened or closed to control airflow in the ducts to directionally maximize efficiency.
Here, a VFD is positioned on the supply and return fans to control duct pressure. The speed of the VFD is reduced as and the load decreases when sustaining a set point.
Return fan speed changes affect static duct pressure or building differential pressure. Unable to operate effectively by itself, volume tracking methods are used to control the supply and return airflows.
Dual-duct VAV systems use separate duct networks for independently moving hot or cold air through a control terminal. Many have a single fan for input or supply and each duct network also has a fan for their purposes.
The hot air supply fan drives air across coils with hot water or steam, while the cold deck has cooling coils. Many systems use a third VFD placed on the single return fan where both hot and cold air pass.
Advantages of VFDs
VFDs help to smooth the processes of starting, accelerating, and decelerating which was a problem.
They also manage high power factors, methods of stopping, and motor reversal functions.
Disadvantages of VFDs
In many cases, VFDs require that inverter duty motors be used to reduce noise and offer improved insulation. When insulation is lacking, motors were potentially more susceptible to failure as a result of premature wear.
Pulse width modulation (PWM) can create unwanted currents, which must be properly grounded and insulated to avoid reaching the bearings.
Limitations of VFDs
VFDs are vulnerable to extremes such as heat or cold and drives may need to be oversized to handle them. Excessive dust is another problem that often requires that an enclosure be installed.
While the user control interfaces are improved, they might be more confusing when compared to line starters. Many VFDs are known for having complex settings and the specifications are often poorly documented.
Smaller applications including local utilities might find the cost to be high when used with larger pumps.
Motors & Power Supplies a VFD Can Be Used With
Direct current fields generally must have a zero-speed option for generating torque when VFDs are used with synchronous motors. For synchronous motors, DC slip rings or AC brushless-type exciters might be necessary for integrating a VFD.
Some motors in constant torque applications are susceptible to overheating and require that an external blower be used. An auxiliary fan is one alternative to a blower that can keep the motor cool.
The power supply voltage and frequency must be compatible with a VFD and motor. This includes devices for switching and protection to ensure compatibility with the load and specific installation.
Prospective users are encouraged to review the manufacturer’s specifications for input and output current ratings.
The voltage of the power supply must be assessed to choose the correct cable sizes and any necessary protection devices.
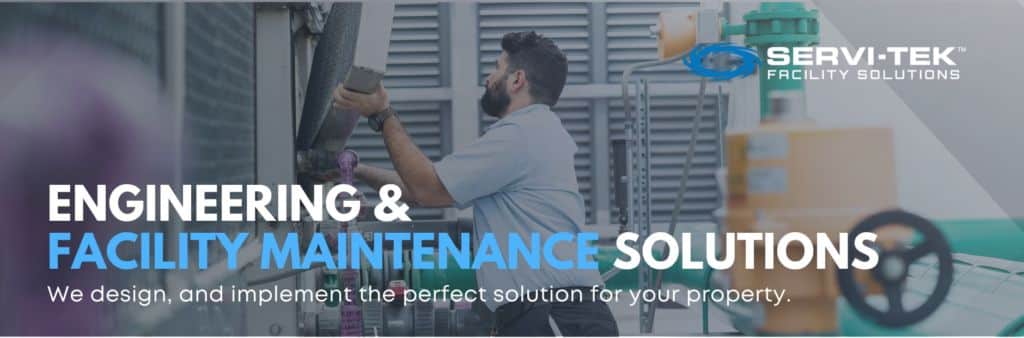
Which Industries Do VFDs Benefit the Most?
VFDs have proven to deliver game-changing results in many different sectors. Those involved in working with the natural environment and with aspects of infrastructure commonly deploy VFDs.
For example, organizations involved in sourcing and generating power such as those involving oil and gas.
Essentially, most of those operating in industrial sectors or manufacturing will potentially derive benefits from implementing a VFD.
Does A Variable Frequency Drive Save Money?
VFDs have proven to reduce interim, short-term, and potentially long-term costs. They also can extend the lifespan of equipment simultaneously.
Energy Efficiency
Energy consumption can be significantly reduced by allowing the pump motor to operate at reduced speeds. Mechanically driven components also tend to increase energy costs; therefore, a VFD is beneficial.
Short Circuit Protection
In addition to controlling speed, VFDs also protect motors with fuses that offer short-circuit protection. The fuses are usually factory-installed by the manufacturer and referencing their specifications is strongly encouraged before replacing them.
Regenerative Braking
Motors that are rotating faster than the winding require that voltage is transferred or otherwise moved. Any excess voltage might be returned to the AC power source, or be absorbed by a braking resistor.
VFDs are usually equipped with circuits that sense DC voltage and can interrupt the flow when necessary. When activated, the VFD might display some “excess voltage” indicator when the inverter output switches “brakes.”
Vibration Compensation
The motor operation may create vibration, such as from torque applied at different frequencies. Based on the way a motor is mounted, vibration levels commonly rise when a VFD is added.
Vibration may result when equipment operates at certain speeds or if the motor bearings begin eroding due to high-frequency impulses. The existence of resonance is often seen at specific torque frequencies when coupled with mechanical frequencies.
Some remedies include placing additional bearings to prevent shaft vibration i.e., every two feet instead of four feet. Having shafts that are larger in diameter and using “stiffer” discharge heads have also proven effective against vibration.
Reduced Carbon Footprint
VFDs have also proven to create environmental benefits, which is a great aspect of today’s “green” business environment. Energy efficiency is linked with reductions in CO2 emissions and using VFDs in applications with electric motors is a solution.
Electricity savings using VFDs might be direct when the power is created on-site or indirectly if purchased from the electric grid.
Specific applications where the VFD is used dictate the reduction in emissions to widely varying degrees.
Who Should Use a VFD?
Those with the most to gain from implementing a VFD include those that operate motors seeking speed control. The serviceable lifespan of a motor can be extended by reducing the abrupt surge of current that occurs at startup.
The overall power system benefits from a VFD because the voltage is more stable. This translates to fewer drops in voltage that commonly cause sensitive peripheral equipment to trip.
The AC motor is also subjected to significantly less wear by more controlled acceleration, deceleration, and when applying torque. The VFD might also provide the capability to program and operate equipment remotely.
VFDs may allow for eliminating the need for a reversing starter and spending money on maintenance. In most cases, VFDs will increase space because the system is physically smaller.
Established Provider of Facility Maintenance and Engineering Services
Servi-Tek Facility Solutions has a more than proven track record of boosting productivity, minimizing downtime, and maximizing efficiency for clients.
Our team of proven industrial technicians and maintenance professionals understands the importance of protecting critical capital assets.
We work with facilities across dozens of industries that are looking for guidance and support associated with new technology.
We offer a very comprehensive scope of maintenance, service, and engineering capabilities while customizing our approach for each client.
Contact us today to discuss how our organization can benefit your business and needs.
