Commercial buildings rely on HVAC – Heating, Ventilation, and Air Conditioning systems, to eliminate humidity and to cool the premises.
Chillers are an intrinsic part of air-conditioning systems in big commercial buildings. Some of these units are referred to as water-cooled chillers, air-cooled chillers, and absorption chillers because of the processes involved in these systems.
These complex machines produce cold water to extract heat from the air in the building.
Chillers dissipate heat from water by compressing a refrigerant and using its physical state as it circulates through the system.
Chillers are complicated machines that are costly to purchase and run.
They consume more energy than any other equipment in a big building. Well-maintained and efficiently operated chillers can yield huge savings on energy bills.
How Chillers Work
Chiller Maintenance
Hi, I'm Eric Sorensen with Servi-Tek Engineering and Facility Solutions. We're still out here at our Orange
County building with the built-up DX, the direct expansion system. And one of the unique things about
these direct expansion systems, is the type of cooling tower that they utilize. And it's really an
evaporative condenser, versus what we consider a cooling tower which has fluid that runs constantly
through it, back through the machine. These machines don't actually see any liquid cooling. That's all
happening inside this evaporative condenser.
What we have here is the refrigerant vapor is going back through, after the compressor, through the
coils. And the coils are running through. There's what's called the tube bundle. And it's running through
this evaporative condenser. Water is being cascaded down on top of them and that's what's causing the
refrigerant vapor to convert back into a liquid form.
One of the unique things about these that you have to be careful about is something called fretting.
Fretting is when the vibration of the machine or the compressors is going through the piping, and that
pipe is being held by a tube sheet. So you've got the pipe going through a hole in tube sheet and a whole
series of them. And that vibration causes a collet that is being held. So collet is around the tube, which is
in the tube sheet. And that collet tends to vibrate out. When that collet vibrates out what happens is the
tube starts to vibrate inside the metal tube sheet. And you can imagine what happens at that point. The
metal on metal aware causes a hole in the tube, which causes refrigerant loss in the entire refrigerant
circuit.
So fretting is one thing to be very cautious of when we have these things. If you're running an older type
of compressor, the Carrier Carlisle, or any type of reciprocating compressor that causes a lot of
vibration, even though you have vibration isolators and all those things that are supposed to prevent
that vibration from hitting the tube bundle itself, it's always a good idea to get to a vibration analysis
done.
This is an evaporative condenser, not a cooling tower in the truest sense. And they're really more
prominent in built-up DX direct expansion cooling systems.
The operation of a chiller involves three primary principles: heat transfer, liquid circulation, and refrigeration.
A low-pressure liquid refrigerant is introduced into the evaporator to commence the refrigeration cycle.
The heat transfer from the water inside the evaporator changes the state of the refrigerant from a low-pressure liquid to a low-pressure gas.
The refrigerant in its gaseous state then enters the compressor which compresses it into a high-pressure gas.
This high-pressure gas is sent to the condenser where the surrounding air or condenser water extracts heat and cools it down sufficiently to once again change its state from a high-pressure gas to a high-pressure liquid.
The refrigerant in its high-pressure liquid state is moved into the expansion valve.
The expansion valve or the metering device regulates the quantity of the refrigerant entering the evaporator, thus initiating the refrigeration process again.
Preventive Chiller Maintenance Benefits
Chillers are a vital piece of equipment in your building’s HVAC system.
Maintenance of your chiller should not mean that you seek emergency repairs when things suddenly go wrong.
It makes sense to set up a contract for scheduled preventive maintenance of your chiller for best results.
Here are some of the key benefits of preventive chiller maintenance:
- Improved energy efficiency and lower utility bills
- Extended life of the equipment
- Better indoor air quality
- Avoidance of costly repairs or replacement
- Minimal disruption for the building occupants
Parts Of A Chiller
Evaporator
The cold liquid refrigerant introduced into the evaporator, streams over the tube cluster present inside.
The liquid refrigerant evaporates and is transformed into its gas state due to heat transfer from the water produced in the chiller.
The water is then moved through the water delivery system to the air-handling assemblies in the building.
The chilled water expels heat from the air inside the building as it moves through the air-handler units’ coils.
The heat thus transferred from the building’s ventilation air warms up the water in the coils as it circles back to the evaporator and the recurring process begins again.
Compressor
The compressor clears out refrigerant from the evaporator and makes sure that the evaporator pressure stays at levels sufficiently low for it to soak up heat at the right rate.
Upon exiting the evaporator, the refrigerant in its low-pressure gas state enters the compressor where it is converted into a high-pressure, high-temperature state, through mechanical compression.
In this state, it leaves the compressor and moves into the condenser of the chiller.
Condenser
The high-pressure, high-temperature gaseous refrigerant moves around the condenser tubes holding the water.
The refrigerant transfers its heat to the water, thus condensing it into the liquid state again.
The condenser water is extracted from the condenser tubes and into the cooling tower where heat from the water is dissipated into the ambient air.
Meanwhile, the liquid refrigerant is pushed into the expansion valve.
In an air-cooled condenser, the hot refrigerant gas is condensed into its fluid state by using ambient air.
Expansion valve
The expansion valve or the metering device regulates the rate of cooling by controlling the flow of the refrigerant into the evaporator.
Having passed through the expansion valve, the refrigerant expands to lower pressure and a much lower temperature.
It cascades around the evaporator tubes, absorbing the heat of the water that’s been circled back into the chiller from the building’s air handler units, thus concluding the refrigeration cycle.
Service On A Chiller
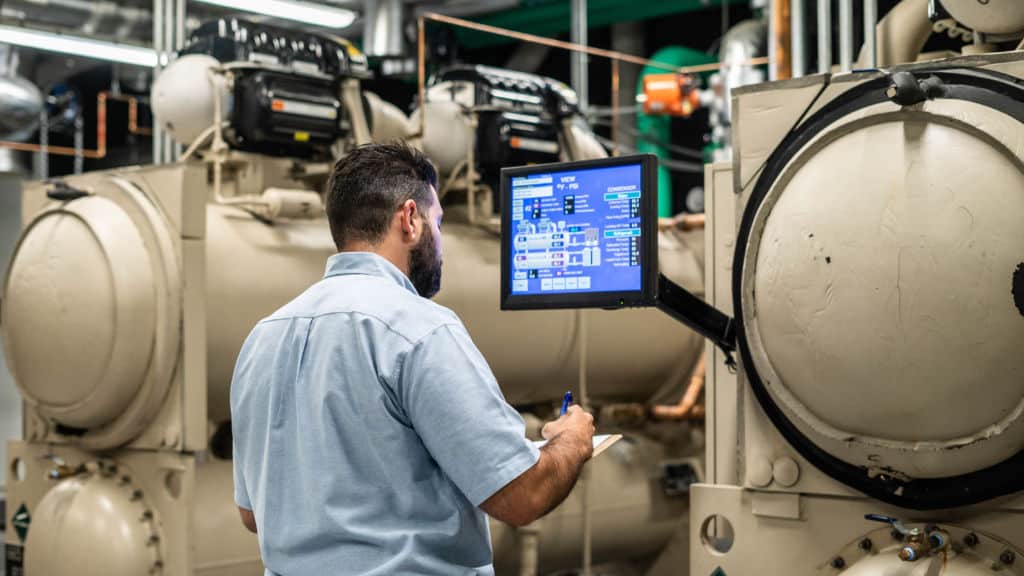
Filter Dryer
The filter screens dirt, metal, or other impurities which helps guard the components mainly the expansion valves. The dryer soaks any left-over moisture in the system which prevents possible freezing.
Hot gas bypass valve
This valve exerts simulated stress of high-pressure, heated gas on the evaporator which thwarts the compressor from short cycling the system at times when the demand for cooling is low.
Liquid Solenoid Valve
This valve blocks liquid refrigerant from entering the compressor during shutdowns.
Refrigerant sight glasses
These provide visual evidence of the refrigerant moving through the system and also indicate the level of moisture.
Types Of Chillers
Mechanical compression chillers can be categorized according to the type of compressor used.
- Reciprocating Compressor: The electric motor turns on the crankshaft and the pistons cause gas compression. The process is similar to that of an automobile engine with multiple pistons. The heated gas gets discharged into the condenser rather than exiting from a tailpipe. The capacity of a reciprocating chiller may be anywhere from 20 to 120 tons.
- Centrifugal Compressor: This compressor runs quite like a centrifugal pump to compress the refrigerant. The advanced design of these chillers allows for superior cooling capacity of at least 150 tons or higher.
- Rotary Screw Compressor: This model has a pair of helical rotors in a stationary casing. As they rotate, the compression of the gas occurs due to volume reduction between the rotors. Rotary screw compression capacity could be between 20 and 450 tons.
- Frictionless Centrifugal Compressor: This is designed for high energy efficiency and is based on magnetic bearings technology. The DC motor has a variable speed and no lubricant is needed for this compressor. It is available capacity ranging from 50 to 300 tons.
Basics Of A Commercial Centrifugal Chiller
Centrifugal chillers provide the most cost-effective way to cool large commercial buildings.
With advancements in technology, these chillers have become the preferred choice for most design engineers.
Commercial HVAC systems usually need a compressor unit to remove excess heat from the indoor air in circulation.
A centrifugal chiller is designed to chill water by making use of the vapor compression cycle.
It will transfer the heat that gets collected from the water as well as the heat produced from the compressor to a water loop.
A cooling tower is then cool the water loop.
One of the reasons behind the popularity of commercial centrifugal chillers is that compared to other chillers, they have fewer moving parts.
As a result, they have a longer lifespan and are easy to maintain.
You can achieve a greater cooling capacity for your building with a smaller energy footprint when you use centrifugal chillers.
How Does A Centrifugal Chiller Function?
The refrigeration cycle is composed of four essential parts: :
- EVAPORATOR
In a water-cooled centrifugal chiller, an evaporator works as the heat exchanger, which takes out heat from the chilled water.
The commonly used configuration is a tube and shell heat exchanger.
The heat converts the refrigerant from a liquid state to a gaseous state. An energy-efficient option could be a flooded evaporator.
- COMPRESSOR
The dynamic energy of the liquid flow will be converted into rotational kinetic energy with a centrifugal compressor.
The refrigerant will go into the pump impeller and will gain acceleration. It will then flow outward radially and exit.
The centrifugal compressor is frictionless and uses a DC motor and advanced magnetic bearing technology.
- CONDENSER
A condenser is also a heat exchange, quite like the evaporator, with a tube and shell configuration that removes heat from the refrigerant.
The pressure on the refrigerant will convert it from a gas to a liquid.
The circulating condenser water temperature rises because of the heat.
This water then goes to the cooling tower where the surplus heat is released into the outside air.
- EXPANSION DEVICE
After the condensation of the refrigerant from gas to liquid occurs, it goes through an expansion device to lower the pressure.
This device can be an electronic modulating valve or a basic orifice plate.
Operating And Maintaining A Centrifugal Chiller
The centrifugal chiller is a vital part of your commercial HVAC system.
You should have a periodic maintenance program in place to keep it in top working condition at all times.
It is important to have trained personnel to keep the chiller in good operation as well as hire a reliable facility maintenance provider for periodic inspections, service, and maintenance.
You can optimize your commercial building load by installing multiple chillers.
First, use the centrifugal chiller that has the maximum efficiency.
Increase the temperature of the chilled water and establish a proper reset schedule to adjust the temperature of water in sync with the ambient air temperature.
When you are using a centrifugal chiller, raising the chilled water temperature by about 2°F will cut down the chiller energy consumption by up to 5%.
Similarly, reducing the cooling tower water temperature by about 3°F will lower your energy use by about 3%.
For water exiting the cooling tower, keep the setpoint as low as the manufacturer would permit.
Why Install A Chiller In A Commercial Building
Commercial chiller installation is particularly useful for commercial or industrial buildings with large machinery and equipment that generate considerable heat.
Here are the key reasons for installing a chiller in large buildings:
- MASSIVE COOLING OUTPUT
Chillers can deliver exceptionally strong cooling at a relatively lower cost.
Depending on the chiller size that you choose, you can expect to have cooling per hour in the range of 180,000 to 1.8 million BTUs.
This makes them well-suited for large commercial and industrial buildings that cannot be serviced merely with standard AC equipment.
- COST EFFICIENCIES
Commercial chillers are designed to circulate water, so they will not continually use water from an external source and then drain it into the sewer system.
In other words, you can improve your building’s water sustainability as well as reduce the utility costs for water and sewer.
The energy usage of modern chillers is also relatively low and saves money.
- PROTECTING MACHINERY AND EQUIPMENT
Overheating of large industrial equipment or machinery can lead to expensive repairs and replacements; therefore, having chillers installed helps to protect the equipment and extend its life.
This can translate into significant savings for the business in the long run.
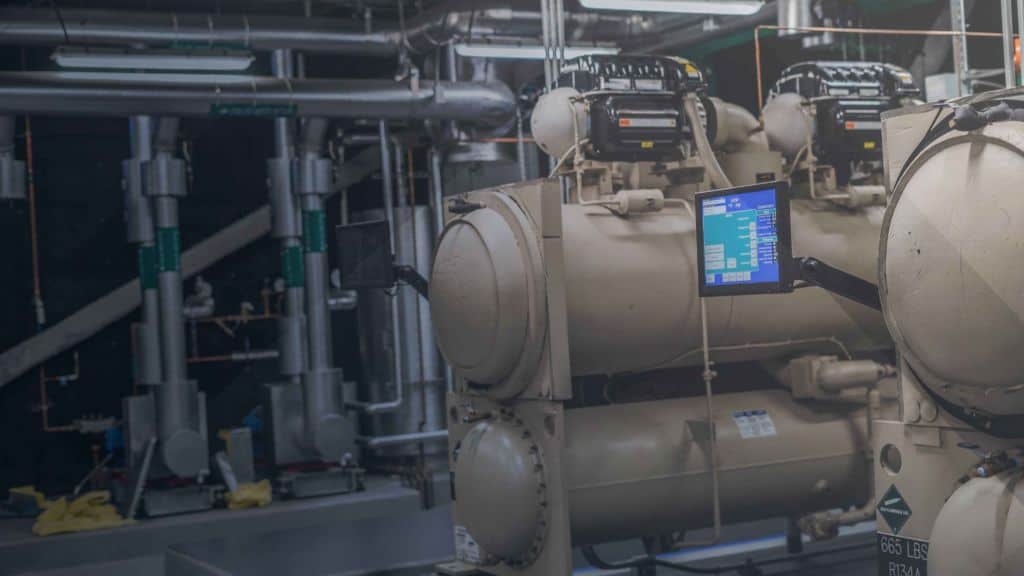
How To Prevent Chiller Breakdowns?
Advanced, state-of-the-art, onboard microprocessor chips control myriad chiller processes.
These controls calibrate safety and operating systems, primarily.
In case of any equipment failure or malfunction, the safety control shuts the chiller down to avert severe damage to the machine.
Operating controls also regulate and adjust some chiller operating functions.
Linking the chiller control system with the building’s direct digital control (DDC) helps to supervise and enhance chiller efficiency.
Is Chiller Maintenance Necessary?
Cost of operating a chiller accounts for a significant part of a building’s utility bills.
Chillers often are a building’s biggest electric load. Chillers running chillers optimally translate into huge savings.
Regular preventive maintenance of chillers can reduce energy costs and help save money on labor and equipment.
A maintenance program for chillers also helps extend the life of the HVAC system.
What Is Routine Chiller Maintenance?
Most organizations acknowledge the value of chiller maintenance and put in place measures to ensure it.
Some accepted best practices for chiller maintenance include:
Treatment of water to get rid of corrosion, scale, mud, algae, and other impurities is vital for all condenser water loops which use an open cooling source. Not doing so can lead to clogging in the condensers, thus hindering heat transfer.
Supervise water quality and look for signs of corrosion through remote monitoring on a regular basis or check chilled water loops once a year.
Inclusions In Annual Chiller Inspection
A seasoned facility maintenance company will offer both annual chiller maintenance services and periodic inspections.
Their team may carry out a detailed inspection of the equipment as well as perform a review of the building’s in-house maintenance logs.
The annual chiller inspection should preferably include the following items:
- Testing of the electrical
- Leak testing and pressure check
- Testing and calibration of controls
- Oil sampling and replacement of unit filters
- Purging system maintenance (if the equipment is low pressure)
- Cleaning of the condenser tube
Chiller Maintenance Checklist
The first part of chiller maintenance should be a visual inspection of the unit.
You should ensure that all pieces of equipment are working, and the necessary safety mechanisms are in place.
The second part is to check for any potential leakages in the refrigeration and water pipework, and look for any visible spillage of oil, refrigerant, or water.
The third part is to identify any potential sources of unusual or abnormal sounds and vibrations.
After the chiller unit has been disconnected from the power source, the following items should be completed as part of the chiller maintenance checklist:
- Tighten any loose fastening or fixing
- Look for any signs of corrosion in the chiller parts, particularly the pipework
- Inspect the cooling coils for corrosion and fins distortion, if any
- Look for any signs of damage in the insulation
- Evaluate the fouling of chiller parts
- Check electrical relays, contactors, starters, and electrical wiring
- Determine whether the compression is aligned to the specs
- Test that safety devices are functioning well
- Check the oil filter and suction filter
- Check the valves, strainers, and pressure vessels
- Determine whether the consumables (oil, refrigerant, water, and glycol) need replacement
Daily Maintenance Schedule For Chillers
Here are the essential steps for daily maintenance to ensure optimized performance of the chiller:
Sequencing and Chiller Use: Sequence or switch off the chillers that are not required
Daily Physical Inspection: Inspect the chiller unit visually to make sure that the machine is operational and all the safety systems are functioning
Inspect the Setpoints: Review all the setpoints to ensure appropriate setting and operating
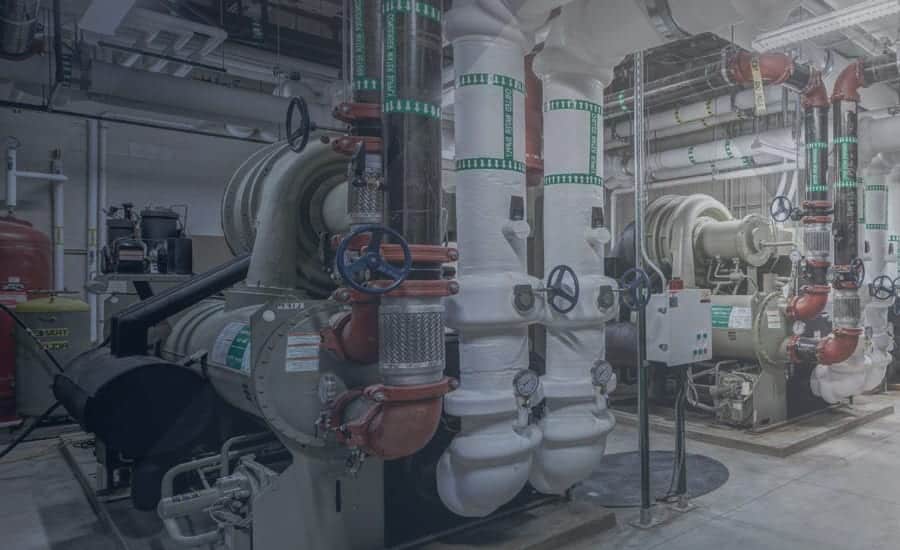
What Is The Proper Way To Increase A Chiller’s Duty Cycle?
Lower the condenser water temperature
One way to improve a chiller’s performance is to reduce the temperature of the water entering the condenser.
It reduces the load on the chiller and makes its work easier, thus increasing efficiency and bringing down costs.
Raise chilled-water temperature
Setting up a chilled-water reset schedule can help adjust the chilled-water temperature as the outside air temperature changes.
A rise in the temperature of the chilled water supplied to the air handlers will enhance the chiller’s efficiency.
Maintain an optimum water flow rate
A flow rate that is too low adversely affects the chiller efficiency and results in laminar flow.
On the other hand, a flow rate too high results in noise and vibrations and could lead to tube erosion.
The minimum flow rate is generally around 3-ft. per second (FPS) while the maximum recommended flow rate is around 12 FPS.
Maintain sufficient refrigerant charge
The amount of refrigerant moving through the compressor directly affects the amount of cooling a chiller can produce.
Maintaining an appropriate level of refrigerant as per the conditions and desired output will ensure a higher chiller efficiency.
Reliability and efficiency can be adversely affected by air and moisture in the system and refrigerant leaks.
The compressor will need to work harder in case of a low refrigerant charge.
Limit inefficiencies caused by air and moisture
Air and moisture leaking into low-pressure chillers can bring down the efficiency of the chiller as compared to their rated performance.
Purge units lessen the effects of air and moisture.

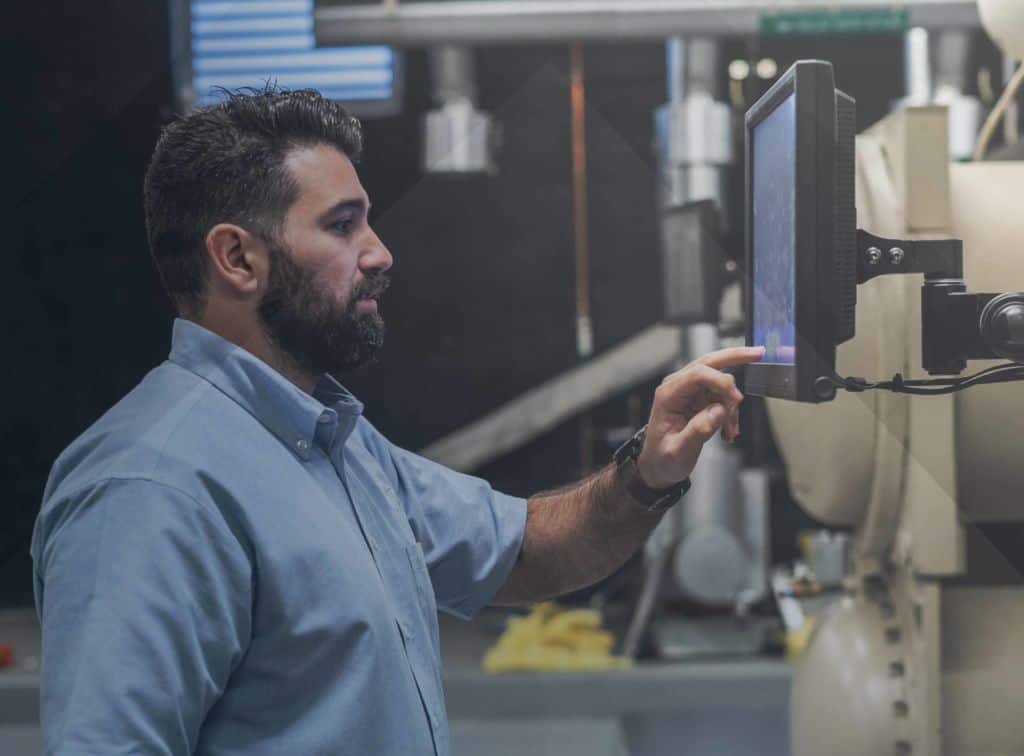
Chiller Maintenance
Inspect compressor oil
A sample of the lubrication oil should be sent to a laboratory for a “spectrometric” chemical analysis once a year.
There is no need to replace the oil unless the analysis demands it. Inspect oil filters for pressure drop and change them if the oil charge is replaced.
Check starters and motors
Check the safety and sensor measurements on microprocessor controls.
Also, check for hot spots and frayed contacts. Shaft seals of open drive motors need a routine inspection for any refrigerant leaks.
Clean air vents to make sure of optimum cooling effect.
Install variable speed drives
The biggest electrical load in a building is usually the chiller motor.
Variable Speed Drives match load to motor efficiency and helps in substantial savings in energy.
Variable Speed Drives minimize the inrush current for the motor which reduces the load factor for chillers running on emergency generators.
Chiller Cleaning
Maintain cleaning and maintenance records
A daily logbook goes a long way towards running and maintaining an efficient chiller plant.
Data history of various operating conditions and their regular audit with the help of remote technologies can help in generating reports that can determine a need that can be acted upon before it can become a problem.
Clean the condenser tubes
The primary key to a well-maintained chiller is efficient heat transfer.
Foreign matter and impurities can escalate heat resistance and bring down efficiency by not allowing the heat transfer as required.
Condenser tubes need to be cleaned at least once a year, or as per the maintenance schedule to rid them of contaminants.
Keep a tab on approach temperatures as higher approach temperatures suggest diminishing heat transfer efficacy.
Steps To Boost Chiller Efficiency
Advancements in chiller technology and design have led to a steady improvement in the efficiency of chillers.
The result is that modern chillers have relatively tight operational tolerance.
Therefore, periodic maintenance and service of the chiller is more important than ever before.
Facility managers should focus on these five steps to improve chiller efficiency when they work with experienced chiller maintenance professionals:
- Maintain a day-to-day operations log
- Make sure that the tubes are kept clean
- Keep the unit free of leakages
- Provide for appropriate water treatment
- Regularly analyze the refrigerant and oil
What Happens When a Chiller Is Not Maintained?
Failing to monitor and sustain chiller maintenance could result in various issues.
In air-cooled condensers, dust and debris accumulation on fins and fan blades can hinder airflow, reducing the cooling capacity.
In water-cooled condensers, heat transfer can be affected for the worse by scale formation, biological growth, or corrosion.
Chillers that are not properly maintained could end up using at least 20 percent more energy.
Safely Clean The Chiller
Mechanical cleaning helps purge mud, algae, sludge, and other materials from the tubes.
It involves taking out the water-box covers, brushing the tubes, and flushing with water.
Chemical cleaning clears away the scale. A chemical cleaning should always be followed by an intensive mechanical cleaning.
What Are The Major Causes Of Chiller Failure?
Chiller Does Not Power Up
It could be the result of a loose connection or even a wrong phase connection (in three-phase units). Check for a blown circuit breaker or fuse and need repairs. Also, check if the input voltage is proper.
Insufficient Fluid Flow
Check if there is sufficient fluid in the tank. A blocked fluid filter or partially closed process valve could also cause insufficient fluid flow. Process piping could be too small. An inspection of the pump for any failure may be in order.
Insufficient Cooling
Check for a clogged air filter or condenser coils. Check if the coolant fluid fulfills the temperature requirements or if its heat transfer properties have deteriorated.
A refrigerant leak, an iced-up evaporator or high ambient temperature could be some other things to check in case of insufficient cooling.

What Are Chiller Preventive Maintenance Tips?
Preventive maintenance work for chillers needs to be carried out daily, weekly, semi-annually, or annually.
Daily | Weekly | Semi-annually | Annually |
Daily visual scrutiny by technicians programming the data is essential. | Inspection of the evaporator and condenser coils. Review of the motor temperature. Scan for leaks, checkup control operation, and water quality. | Inspection of load balances and limits. | An intensive cleaning, electrical system inspection, and other maintenance tune-ups are required. |
Preventive maintenance not only helps protect your chiller investments but also helps in reducing energy usage.
Scheduling For Prevention Of Chiller Breakdowns
You need a professional facility maintenance service provider with the necessary tools and skill-sets to perform preventive maintenance.
You can make a contract for periodic maintenance and service of your chiller and other building equipment to ensure that your building is safe and fully functional at all times.
Scheduling preventive maintenance in the long run is the most cost-effective way to run your building and prevent chiller breakdowns.
Reliable Chiller And HVAC Maintenance For Your Building
Servi-Tek provides customizable engineering and facility maintenance solutions for commercial buildings.
Our experienced teams are equipped to perform best in class commercial HVAC maintenance, including chiller service, repairs, and preventive maintenance.
If you have concerns about your chiller’s cooling capability or energy efficiency, contact us online or call us at (866) 454-6185 today.