One of the most important ways to keep your facility in great shape is by doing an easy-to-follow preventative maintenance schedule.
If you’re not sure how to get started, don’t worry. In this blog post, you’ll find out how to perform easy to follow preventative maintenance in your commercial building, how to keep costs away, and have safe working conditions for your employees.
What Is Preventive Maintenance?
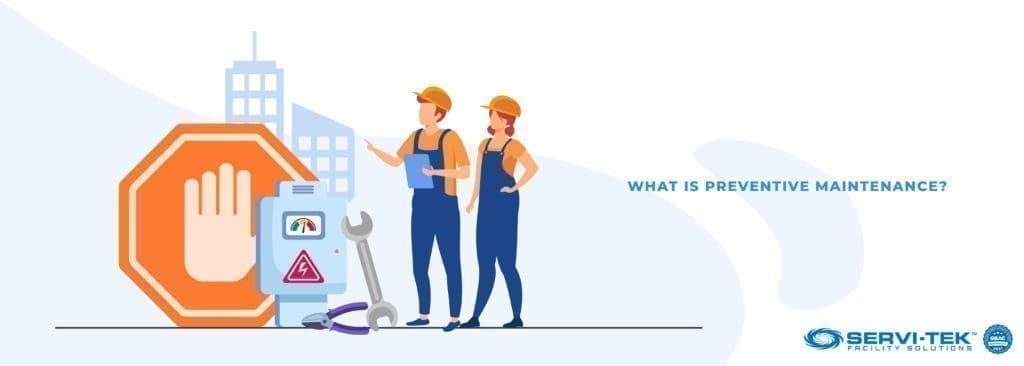
Preventive maintenance (PM) is the regular inspection and care of assets to prevent any unexpected equipment failure or costly unplanned downtime. It ensures that all equipment is kept in running order, without any costly delays.
This is different from reactive maintenance which occurs after a piece of equipment has already broken down. Preventive maintenance helps in keeping assets efficient and in optimal working order proactively.
A successful preventive maintenance strategy requires scheduling and planning before any major problem occurs. A good PM program will involve keeping records of equipment servicing and past inspections.
Many companies make use of preventative maintenance software since it can be too complex to maintain a preventive maintenance schedule for large pieces of equipment.
Preventive maintenance software can be used for organizing required preventive maintenance tasks.
Who Is Responsible?

Several routine checks will be carried out by the facilities team to perform preventative maintenance. The procedures include testing, parts replacement, inspections, lubrication, measurements, tightening, and adjusting of equipment.
These will allow the facilities team to perform maintenance tasks adequately and deliver the right kind of repairs whenever needed. It is easier to fix issues that are detected faster. This can also extend the overall useful life of equipment and systems within a building.
It is best to hire a commercial maintenance contractor to carry out preventive maintenance tasks. This will ensure that the maintenance is performed on time as scheduled. It will also prevent the in-house facility crew from being overwhelmed.
The majority of preventative maintenance plans fail because the facilities team doesn’t have enough time to carry out proper inspections.
What Are The Benefits Of Consistent Preventive Maintenance?

There are several key benefits of performing preventive maintenance for facility maintenance managers and building owners. This includes:
1. Improved Safety
Potentially dangerous failures can be prevented by maintaining assets and equipment. This is useful towards reducing injuries risks and any associated liability lawsuits.
2. Greater Equipment Lifespan
You can improve the lifespan of your asset by ensuring that the equipment runs as per guidelines. Failing components and parts reduce the lifespan of the equipment. This can result in expensive replacement and long-term damages.
3. Improved Productivity
Poor maintenance can significantly reduce a company’s production capacity and seriously impact the bottom line.
As a facility manager, it is your responsibility to prevent a fall in productivity by meeting the maintenance requirements. This will also reduce their downtime and help towards enabling greater productivity and efficiency.
4. Reduced Costs
Experts believe that running any asset to failure can prove to be ten times as expensive as performing basic periodic maintenance. The expense manifests in the form of unexpected repairs and downtime.
You can schedule necessary part replacement and repairs by understanding the maintenance requirements.
The repairs can be performed at a suitable time when you identify them early. You also have the option to decide whether the repairs need to be performed internally or with the help of an outside professional.
You can always work with a comprehensive service provider that offers a full range of services, including inspection, maintenance, and repairs.
5. Reduced Energy Consumption
Preventive maintenance has a major environmental benefit component. Poorly maintained equipment and assets use more energy as compared to the ones functioning correctly.
This means there is a financial benefit of lower energy bills. In some cases, the reduction in energy bills makes up for the cost of frequent inspections.
What Does The Preventive Maintenance Schedule Cover?

The purpose of a preventive maintenance schedule will vary depending on the type of asset and the operation performed. There are several available standards to industries that help in determining maintenance schedules.
This ensures that assets and pieces of equipment do not run into failure. The industry guidelines will also cover the type of maintenance and inspection required.
Ideally, a preventative maintenance schedule should follow the standards or guidelines set down by manufacturers to ensure proactive maintenance instead of reactive maintenance.
Reactive maintenance refers to the steps you take when something has already started to break down. It can be compared to damage control rather than preventing damage in the first place.
A predictive maintenance schedule should also cover tasks, such as condition monitoring. This provides an accurate recording of servicing and inspections of the equipment. It helps in creating an accurate lifespan of particular components of the equipment.
What Buildings Need This?
Preventative maintenance is required by all major commercial buildings involving equipment. Every commercial facility has an HVAC system, which necessitates the need for preventive maintenance.
These are a few common types of buildings that need to employ a preventative maintenance schedule:
1. Offices and Workspaces
There are boilers and HVAC units in workspaces, and preventive maintenance can decrease the likelihood of system failure.
You need to regularly check elevators, parking lots, hallways, and the kitchen. This is to make sure that your workers have a safe, risk-free working environment.
2. Hospitals
There are strict sanitation and safety standards for hospitals as per OSHA guidelines.
Hospitals can perform preventive maintenance to preserve the value of their fixed capital assets, such as imaging equipment.
3. Schools and Universities
There are various types of equipment at educational properties. This includes research and laboratory equipment. It is recommended to hire a commercial maintenance contractor to take care of managing the complete asset lifecycle.
Equipment maintenance will include HVAC inspections, light and ballast replacements, and emergency repairs for leaks and flooding.
4. Retail Malls and Shopping Centers
There may not be a lot of heavy-duty equipment in a mall or shopping center, but the elevators and HVAC systems need constant preventive maintenance. These systems are costly investments, and their absence will not go unnoticed.
A surprise breakdown can cause discomfort to a lot of customers, and can even shut down the entire business for a while.
5. Tenant Buildings
You cannot leave your building and all its components to the engineering maintenance supervisor. It needs a trained and experienced company to ensure the HVAC system and elevators among other equipment function as intended.
Residential buildings can benefit from having preventive maintenance performed as well.
6. Factories, Workshops, and Warehouses
This is perhaps the most important type of building to get preventative maintenance. Unintentional equipment failure could result in lower productivity and reduced profits. Factories in particular should invest in hiring a commercial maintenance contractor for preventing untimely machine breakdowns.
What Is a Preventive Maintenance Plan?
A preventive maintenance program can be a series of guidelines, processes, and tools to help a business perform necessary preventative maintenance while being efficient with money and time. It can be highly beneficial if you are looking to break out of breakdowns and reactive maintenance.
What Is Easy to Follow Preventative Maintenance?

It takes time to transition from reactive to preventive maintenance. You’ll need to follow a strict calendar and enable resources to ensure that your facility is on the right path.
You need to create a preventive maintenance schedule and stick to it for achieving a successful preventive maintenance program.
The following steps are part of all standard preventative maintenance programs:
1. Perform A Walk-Through Inspection
The first thing you must do in any preventive maintenance plan is to carry out a thorough inspection. The team should look at all equipment and systems that may require maintenance.
2. Maintain or Replace HVAC Filters
HVAC filters are always part of any preventative maintenance plan. There is something that needs fixing even if the system is a brand new one.
For starters, you may need to change or clean the air filters. It is recommended to create a special preventative maintenance plan just for the HVAC system. This will allow you to stay on top of things.
3. Maintain or Replace Lighting Fixtures
Light fixtures should be part of the maintenance plan to ensure that no hallway or corridor is left in the dark. Preventative maintenance can help you avoid costly repair and safety problems.
4. Keep Up To Date On Electrical Outlets
Preventive maintenance plans can include taking care of all electrical outlets.
5. Keep Up To Date On Medical Equipment
This is specifically for medical institutions and hospitals. The maintenance team should take care of all medical equipment. In other buildings, the first aid kit can be checked during preventive maintenance to ensure everything is in order.
6. Maintain or Replace Fire Alarms
Fire alarms need to be checked to stay compliant with OSHA and building standard codes.
7. Maintain or Replace Plumbing Fixtures
Ill-maintained plumbing fixtures can result in leaks and major problems as a result of that. It can also cause water stains on the walls and ceilings.
8. Maintain or Replace Floor Coverings
Floor coverings are important in any office space or customer-facing business. You can have the floor coverings cleaned as per scheduled maintenance to avoid replacing them before time.
9. Maintain or Replace Paint Surfaces
Power washing can be included as part of the periodic preventive maintenance to clean walls and paintwork. This can include removing graffiti from the walls as well.
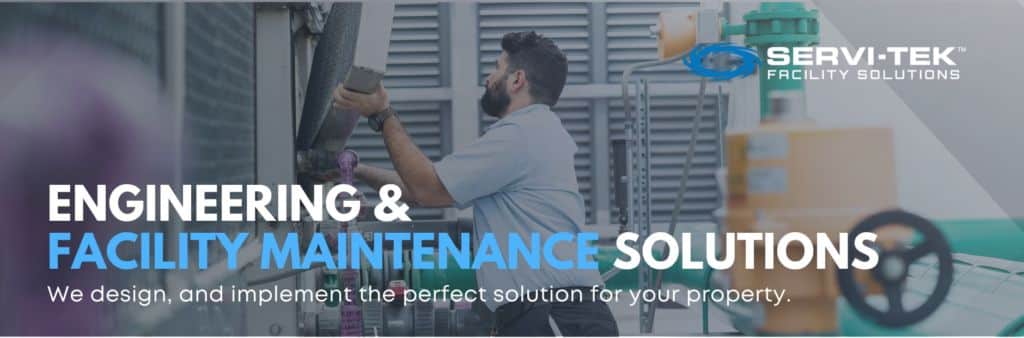
How Often Should Facility Maintenance Occur?
Preventive maintenance can be scheduled on usage, time, or condition-based factors.
These are a few types of preventive maintenance your building might need:
1. Usage-Based Preventive Maintenance
Maintenance action is triggered by usage-based preventive maintenance when the equipment usage hits a particular benchmark. This can be after a certain number of hours, miles, or production cycles. An example of this is that motor vehicles are scheduled for maintenance after a certain number of miles.
2. Time-Based Preventive Maintenance
A set time interval is used for scheduling preventive maintenance tasks in a time-based approach. This can be every 10 days or more. For instance, preventive maintenance can be made necessary like regular inspection on the first of every month or every 4 months.
3. Condition Based Preventive Maintenance
This is a type of proactive maintenance. The maintenance strategy is to monitor the real condition of equipment for determining whether maintenance needs to be performed or not.
In this type of maintenance, the equipment requires maintenance tasks performed only when it shows signs of upcoming failure or decreased performance.
For instance, a machine will be maintained when vibration reaches a certain threshold. The vibration in this case would indicate the need for certain parts to be lubricated or replaced.
Variables To Consider
These are a few factors you should consider while developing a preventive maintenance plan:
- Qualified and experienced employees for overseeing and executing the program;
- Consider a computerized maintenance management system (CMMS);
- Consistent and regularly scheduled equipment maintenance for reducing the likelihood of failure;
- Make informed decisions for electrical component replacement;
- Ensure that scheduled maintenance shut-downs doesn’t affect productivity;
- A preventive maintenance checklist should include all important tasks;
- Follow manufacturer recommendations for scheduling maintenance;
- Clear and simple record-keeping methods.
A Consistent Schedule Of Preventive Maintenance
A preventive maintenance plan must be followed consistently and as per schedule. These are three steps to ensuring that your preventative maintenance plan doesn’t fail:
Step 1: Develop A Preventative Maintenance Schedule For Your Facility
The first step is to create a detailed and easy-to-follow preventive maintenance schedule for your facility.
If you are planning on hiring commercial contractors for the work, then you should share the preventive maintenance plan with them before bringing them on board.
Step 2: Keep An Accurate Record Of Work Done
It is vital to keep an accurate record of all work that is being done. This includes servicing, repairs, and inspection. This catalog should be maintained for individual machinery, equipment, and assets.
Step 3: Set Up Protocols to Make the PMs Easy to Follow
The facility manager should set up easy-to-understand protocols for the preventive maintenance plan.
The Importance of Properly Inspecting Your Facility
These are a few reasons why you should inspect your facility properly:
- Equipment problems that are not detected early and fixed can result in costly issues. Equipment that doesn’t function properly is at an increased risk of damage while being operated. This can be due to further mechanical problems or accidents.
- Recurring equipment concerns can be identified through past work orders. This can provide you with the data to quantify trends and isolate causes.
- Technicians tend to take better care of equipment since regular inspections make them responsible and accountable. This is particularly important in the case of critical assets.
Call for Preventive Maintenance Today
Preventative maintenance is a highly cost-effective way of improving the efficiency of both equipment and employees. You can find it costly to neglect electrical machinery. It is helpful to create a program that establishes guidelines for the maintenance and inspection to be performed.
If you are ready to make the switch to planned preventive maintenance, then it’s time to reach out to Servi-Tek Facility Solutions.
We are the leaders in helping commercial facilities stay on top of maintenance and repairs. We can provide you with various options once we get a better understanding of what your current options are and what you are trying to achieve.
Contact us today! We’ll perform a free inspection, answer all your questions, and discuss how we can help you take your business to the next level.