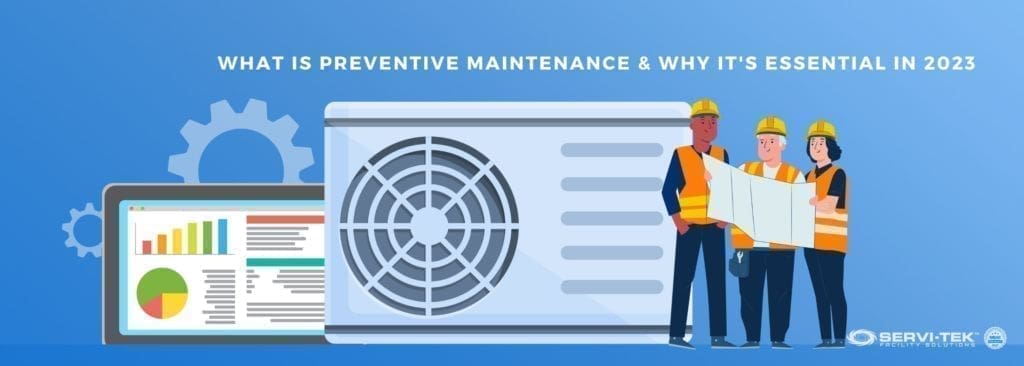
Preventive maintenance is becoming an increasingly popular concept among facility managers as it helps in extending the useful life of assets. Based on this, preventive maintenance is not something you should consider keeping in-house in 2023. Commercial maintenance contractors have the necessary resources, trained technicians, and industrial knowledge to effectively maintain and manage your equipment.
Your facility can benefit from higher accuracy, efficiency, and profitability by implementing a preventative maintenance program which can eventually lead your facility into a predictive environment with 100% uptime and ultimately mitigate loss in time and operations revenue.
What Does Preventive Maintenance Mean?

Preventive maintenance is a systematic approach that allows for predicting and preventing catastrophic equipment failures before they happen. Facilities personnel are required to carry out routine inspections, repairs, and maintenance of assets in order to ensure that they are working as intended. When a preventive maintenance program is working correctly, staff members in facilities can focus less on reactive maintenance and focus more on maintaining equipment in an environment where equipment is functional with the highest possible uptime.
When Facility maintenance transitions from a reactive environment to a predictive one it makes budgeting and KPI of facilities easier to create and navigate.
Preventive maintenance has become more important in 2023 in helping the facility team to understand industry best practices so they can approach time-sensitive work orders and prioritize upcoming maintenance tasks. After all, it’s always better to prevent equipment failures and issues as compared to react to them. The likelihood of unexpected issues is reduced by preventive maintenance and it promotes the optimal performance of the equipment.
These are a few ways facility managers and their teams can stay on top of scheduled maintenance in 2023 to avoid any setbacks:
- Scheduling and performing regular equipment inspections
- Conducting regular cleaning of assets, buildings, and grounds
- Reducing wear and tear by lubricating moving parts
- Adjusting controls for energy efficiency and optimal performance
- Replacing and repairing any defective equipment parts
Different Types of Preventive Maintenance

Preventive maintenance is a blanket term with different types of maintenance included in it. These are:
Time-based maintenance
This type of maintenance can be helpful in creating an annual or monthly maintenance schedule that complies with recommended manufacturer guidelines for inspecting and cleaning equipment. This can help the facility remain on track with its maintenance schedules. You should remember to regularly check essential equipment and machinery that may disrupt operations if not working. This will ensure smooth operations throughout the year.
These are a few examples of calendar-based preventive maintenance:
- Getting the air conditioner serviced within 1 – 2 months of summer
- Replenishing salt in soft water systems
- Cleaning vents at least twice a year to comply with health standards
You need to consider major utilities, tools, equipment, and technology when creating a calendar-based preventive maintenance plan. Your business may depend on this plan for success. These plans should be checked regularly for ensuring the facility continues to thrive. The last thing you need is to close the shop for several days because of equipment downtime.
You may want to consider hiring an experienced commercial contractor to support calendar-based maintenance. This will allow you to keep costs to a bare minimum while ensuring that you are always on top of breakdowns and other problems. Trained technicians have a better idea of the equipment and systems that may need a bit of additional care.
Usage-based maintenance
You should track usage if your organization makes use of certain equipment or machinery on a regular basis. You can track usage based on operating hours, production cycles, or equipment monitors if it doesn’t automatically provide notifications and tickets regarding the number of operating hours reached. Certain equipment needs maintenance on the basis of usage, much like the way a car is serviced.
Whether it is an essential piece of machinery or a vehicle oil change, you can stay on top of proper maintenance and care by reaching a particular number of hours. This will ensure the long-lasting use of the equipment. This is also helpful in case of machinery that is too expensive to replace.
Predictive maintenance
Predictive maintenance requires sensors for capturing information regarding a particular piece of equipment. This can be vibration or temperature sensors. The technology will alert you to an inspection or upgrade. It may trigger work orders if an appliance or machine needs maintenance or replacement.
Predictive maintenance involves regular monitoring of the condition of essential machinery for tracking performance. It can detect possible defects that may have caused a system crash. This type of maintenance is particularly useful in the following industries:
- Power and Energy
- Food production plants
- Manufacturing plants
The information gleaned from predictive maintenance can be used for forecasting whether a system downtime may occur in the near future or not. Maintenance tasks can be scheduled quickly for reducing (crashes on a piece of critical equipment.)
Prescriptive maintenance
Prescriptive maintenance makes use of machine learning, advanced analytics, and artificial intelligence for generating maintenance predictions. This is on the similar patterns of predictive maintenance analysis. Prescriptive maintenance provides recommendations for improving system operations. It follows up on the work order and oversees the entire process.
This type of preventive maintenance is usually advanced for most types of business operations. You probably don’t need this if you can manually check essential equipment and stay on top of inspection procedures as per manufacturer recommendations. You are already way ahead where effective preventive maintenance is concerned.
Importance of Preventive Maintenance
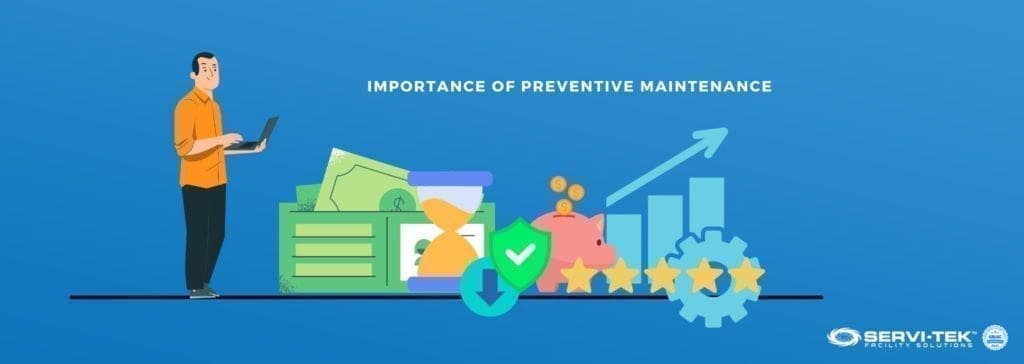
Preventive maintenance is essential to facility management since it lays the necessary foundation. It ensures that assets and equipment run efficiently to avoid any costly and large repairs at a later date. It also maintains a higher safety level for all employees. Properly planned and running preventive maintenance programs can help in keeping operational disruptions to a minimum.
You can use preventive maintenance with the right tools and resources to transform the way your premise, grounds, and buildings/facilities are kept.
These are a few reasons why preventive maintenance is essential to the smooth running of any organization:
Save money on repairs and utility bills
Maintained equipment breaks down less often. They also don’t consume as much energy by running at optimal and efficient levels. Your equipment will run efficiently since all parts are working as they should. It’s impossible to prevent reactive maintenance completely. However, you can reduce the likelihood of a major breakdown with a functional preventive maintenance program.
Delay replacement of critical equipment
Air handling units, HVAC systems, boilers, plumbing, and roofing are a few examples of expensive assets in a facility that needs regular and consistent maintenance for optimal performance. You can help these assets and other equipment/assets run longer by inspecting them on a regular basis. Any issues can be spotted early and dealt with quickly as required. You can make sure the equipment remains in its best shape by extending its useful life.
Safer work environment
The majority of facility managers agree that the health and safety of building occupants is a top priority. You can keep facilities safer and more secure through preventive maintenance by ensuring that all equipment and assets meet appropriate safety standards. They will be less likely to cause serious harm to operators or pose any other risk if any issue is detected early and fixed. You can reduce dangerous and catastrophic equipment failures with regular maintenance. This can play a major role in making the facility a safe place for all occupants.
Reduce asset breakdowns and disruptions
You won’t be caught off guard if routine maintenance checks are performed. Preventive maintenance programs will let you know beforehand if a part needs to be replaced. You can avoid unexpected disruptions by keeping the parts on hand for timely repairs. You can also reduce the wear and tear on your equipment by replacing parts before they are completely damaged and help your facility get close as possible to 100% uptime.
Ease in budgeting
Preventive maintenance, especially when performed by trained commercial contractors, gives you a heads-up about any costly repairs, maintenance, or replacement. You will be better prepared and able to ensure where KPI and cost need to be increased or transitioned so that you can plan better for the quarterly or yearly budgets. This can also aid in strategic facility planning. You can keep track of all information regarding the asset, parts required, and repair personnel with a preventive maintenance plan in place. You will have a clear idea of the upcoming maintenance expenses.
Lengthen the lifespan of your asset
The most important benefit of preventive maintenance is arguably the lengthened lifespan. You can ensure your equipment is run longer with lowered costs by keeping it in good running condition. Mean time between failures (MTBF) is a frequently used KPI by facility managers for making informed maintenance decisions.
Facility leaders use such tracking information for planning preventive maintenance at the right moment. They catch any repairs before the equipment breaks down and causes operational disruptions. A good downtime tracking system has invaluable benefits. Over 78% of organizations have implemented preventive maintenance reports for assessing the increase in their system’s lifespan.
Enhance customer satisfaction
You can increase revenue and cost savings by making sure the equipment always runs as efficiently as possible. This also helps in creating a strong brand image while boosting customer satisfaction. Preventive maintenance can play a major role in avoiding breakdowns in manufacturing facilities. This can uphold the high quality of the goods manufactured which can in turn guarantee customer satisfaction and also prevent loss in profit by making sure distribution and production aren’t impacted by a neglected equipment malfunction.
Increased employee productivity
You can boost employee productivity by helping your workers perform their job responsibilities. There are certain systems that are critical to day-to-day operation. This can be a chiller providing cooling capacity to a cold storage facility or scientific asset or a boiler providing comfort heating to office spaces during a winter storm or process heating for an assembly line in a manufacturing facility. Regardless of the machinery, facility managers have a primary responsibility of ensuring that operational activities are not affected.
Reduce Risk with Preventive Maintenance
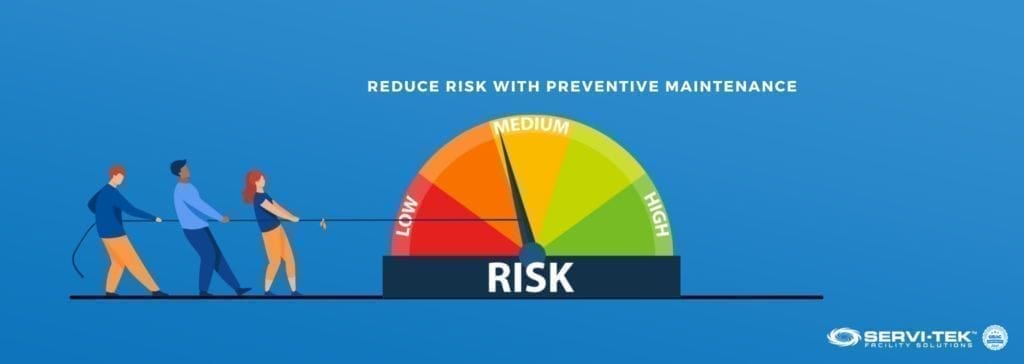
All facilities face potential risks, which can place workers, building occupants, and business goals at risk. Facility managers along with their teams are responsible for upholding safety and securing these risks in a facility. You can reduce two types of risks to your premise with a strong preventive maintenance plan.
Reduce risk to people
After the covid-19 pandemic, there is an enhanced need to protect building occupants. Facility managers have the power to take measures that can protect their employees from sickness and injuries. The time spent by an employee away from work is productivity lost. Recurring maintenance and inspections can play a major role in keeping occupants safe. This should be done on door locks, security cameras, emergency exit signs, fire extinguishers, and other assets.
Reduce risk to property
It can be expensive to perform reactive maintenance. There are significant costs when an asset breaks down unexpectedly. You would need to pay for the cost of diagnosing faults, replacing parts, and ultimately fixing the problem. Preventive maintenance can reduce the likelihood of such risks dramatically. Planned maintenance and routine asset checks should be implemented by facility managers to help avoid costly fixes.
Key Action Items of Preventive Maintenance in 2023
Preventive maintenance essentially takes a proactive approach where maintenance is concerned. There are four key action concepts that are fundamental to a successful preventive maintenance program:
Inspection
Inspections ensure that all equipment and maintenance in a given facility are safe. It also provides the business with liability protection. Regular inspections play a major role in property protection too.
Detection
There may be significant costs associated with operating on a run-to-failure approach. The majority of facility managers use a preventive approach for detecting problems early. These issues are relatively easy and cheaper to fix when detected early.
Correction
Facility managers are encouraged by preventive maintenance to take a proactive approach towards correcting and caring for issues before they occur. Prompt steps need to be taken if an issue is detected before it becomes worse and shuts down operations.
Prevention
Inspection records and maintenance notes can be combined for correcting any repeated issues with machinery. You can increase productivity and reduce stress by avoiding asset failure. The facilities team can focus on proactive tasks instead of reactive ones.
Create a Preventive Maintenance Program for 2023
It’s always a prudent idea to develop a preventive maintenance plan. Based on this, you can quickly get frustrated if you don’t know where to start. The good news is that it can be painless to implement a proactive process if you have the right tools and a solid strategy. The quickest and easiest way of supporting a winning preventive maintenance program is by hiring a commercial contractor or using facility management software.
You need to designate your goals for the process and list each item that requires attention. For instance, your goal may be to experience zero lost time or to target a particular machinery. You need to make sure the entire team is on the same page where goals are concerned. The second step is to plan and schedule maintenance by selecting the most convenient day for upgrades and repairs.
You should also stock up on all essential supplies. These steps will establish a baseline for preventive maintenance. You may need to revisit the drawing board if you feel that reactive maintenance is still taking place at a high frequency.
These are a few examples of preventive maintenance:
- HVAC system: The heating, cooling, and ventilating system is a vital part to the success of any business. You cannot have it go bust in the middle of the summer.
- Essential assets: Main assets in a business are the most frequently used ones. For instance, your business cannot probably function properly if you own a restaurant and the walk-in refrigerator stops running.
- Essential vehicles: You should inspect all essential business vehicles frequently. Failure to perform these tasks may result in engine failures, breakdowns, and dangerous driving conditions.
Preventive Maintenance
Too much of anything is not a good thing. You don’t want to eat away your profits by investing too many people and other resources in preventive maintenance. You should always check the work history of a particular item for gauging whether it needs another inspection and parts replacement or not. You should also maintain a log of recent upgrades and malfunctions.
Additionally, be careful not to overdo simple preventive measures, such as over-lubricating machinery, over-salting parking lots during colder months, or over-scheduling safety walks of employees. Such actions will only result in lost time. In severe cases, it may also lead to preventable and unintentional damage.
It’s always a salient idea to consider outsourcing your preventive maintenance needs. This is especially true if you have several different machinery and don’t want to waste money on training your team. Commercial contractors are cost-effective when it comes to preventive maintenance. Always start by targeting the most essential equipment for ensuring optimal functionality and conditions.
You should take preventive maintenance actions in those areas where the benefit outweighs the costs and risks.
Get in Touch with an Experienced Preventive Maintenance ContractorThe life of your equipment can be prolonged by preventive maintenance. The team at Servi-Tek Facility Solutions can ensure that your building satisfies compliance and inspection needs while decreasing reactive maintenance requests and downtime. Learn more about our services today by calling (866) 454-6185 or completing our online contact form.