A misguided notion in many facilities, small businesses, and organizations today is:
“if they do not break it, don’t fix it.”
It is a preconceived notion that needs to be banished in maintaining properties, buildings, and facilities.
The repeated usage of a piece of equipment without a routine maintenance plan is ten times more costly than a corrective maintenance program.
Without a maintenance strategy, you may run into frequent downtimes, which will slow down your processes and lead to costly repairs.
I know the questions on your lips, as you read this post, are what is preventive maintenance, and how important is it? Here’s everything you need to know about preventive maintenance.
WHAT IS PREVENTIVE MAINTENANCE?
Preventative maintenance involves proactively scheduling maintenance activities which are needed for equipment and systems to reduce the likelihood of unplanned breakdowns.
It is important to perform maintenance activity on the machine while it is operable and ensure functional reliability.
It focuses on providing a systematic inspection, detection, and correction of any failure before its occurrence or before it turns into a major defect.
This form of maintenance includes testing, adjusting, measuring, and replacing any part of the equipment to prevent the fault from occurring.
You can implement a preventive maintenance program by using facility management software.
In the present world, preventive maintenance is playing a vital role, as the use of machines and equipment is an advantage.
Through preventive maintenance, equipment reliability is preserved and enhanced as it detects worn components before it can cause a major failure.
3 BENEFITS OF PREVENTIVE MAINTENANCE FOR YOUR FACILITY
The idea behind a preventive maintenance program is to limit unexpected breakdowns of systems and equipment.
Are you undecided about adopting an effective preventive maintenance program for your facility?
These four benefits of maintenance planning should change your mind:
1. SAFETY
Preventive maintenance reduces safety risks for employees and customers, which may significantly lower the risk of lawsuits and workers’ compensation claims stemming from accident injuries. .
2. INCREASE EQUIPMENT LIFE
An effective preventive maintenance plan will help maximize the serviceable lifespan of key equipment and systems. Regular maintenance helps limit wear and tear, minimize utility consumption, and heightens efficiency.
3. REDUCED COSTS
Unscheduled downtime can cost significant time and money as a machine breakdown can disrupt the goals and efficiency of your facility.
Although preventive maintenance activity, such as regular inspections and testing, often seems burdensome–it is critical.
For example, performing preventive maintenance helps prevent emergency repairs. In many cases, emergency repairs involve collateral expenses, such as the high cost for expediting shipping of replacement parts.
4. INCREASE PRODUCTIVITY
Preventive maintenance increases productivity by reducing the amount of reactive work performed by staff and management.
Good preventative maintenance will allow for earlier detection of problems and lowers overall capital expenses.
Maintenance activities today increasingly use new technology. For example, accessing information via handheld devices, generating electronic work orders, and real-time reporting capabilities.
Main Types of Preventive Maintenance
There are different preventive maintenance programs you can use to ensure your equipment operates smoothly for the rest of its useful life.
Selecting an effective preventive maintenance program for your facility would depend on the equipment and its operational capacity.
Some common types of preventive maintenance used in commercial facilities include:
Time-Based Maintenance (TBM)
Time-Based Maintenance (TBM) is a calendar schedule, which uses a computerized maintenance management system to trigger alerts for facility maintenance.
For example, it maintains the HVAC systems of your building before summer every year and replacing the air filters every three months to maintain high-quality indoor air.
Failure-Finding Maintenance (FFM)
Failure-Finding Maintenance is a set of preventive maintenance tasks that can predict and detect equipment failures in the components of your machinery systems.
This maintenance strategy will reduce the likelihood of a breakdown in the machinery systems.
A piece of equipment that functions as a backup or an emergency (fire alarms) needs to undergo FFM.
Failure-Finding Maintenance tasks checklist all the potential circumstances in which a protective system would malfunction.
Risk-Based Maintenance (RBM)
Risk-Based Maintenance prioritizes the maintenance of equipment by the risk of mechanical failure.
It means that a piece of equipment with a high risk of failure is monitored and maintained, and the assets with a lower risk of damage have a less stringent pm plan put in place.
RBM aims to achieve the economical use of maintenance resources in your facility.
Predictive Maintenance
Predictive Maintenance is pinpointing when your machinery may require adjustments before it breaks down.
The predictive maintenance strategy works through the overall knowledge of the equipment and expected performance.
Artificial intelligence and sensors attached to the machines will collect a range of operational data to help you detect the possibility of a breakdown.
It eliminates the risk of unplanned downtime and increases the overall safety of your operations.
Condition-Based Monitoring (CBM)
Condition-Based Monitoring involves a maintenance activity that monitors the actual condition of your equipment.
It aids in deciding on which preventative maintenance tasks to perform and when to schedule the routine maintenance.
The CBM is operational when the equipment indicators display inefficiency signs.
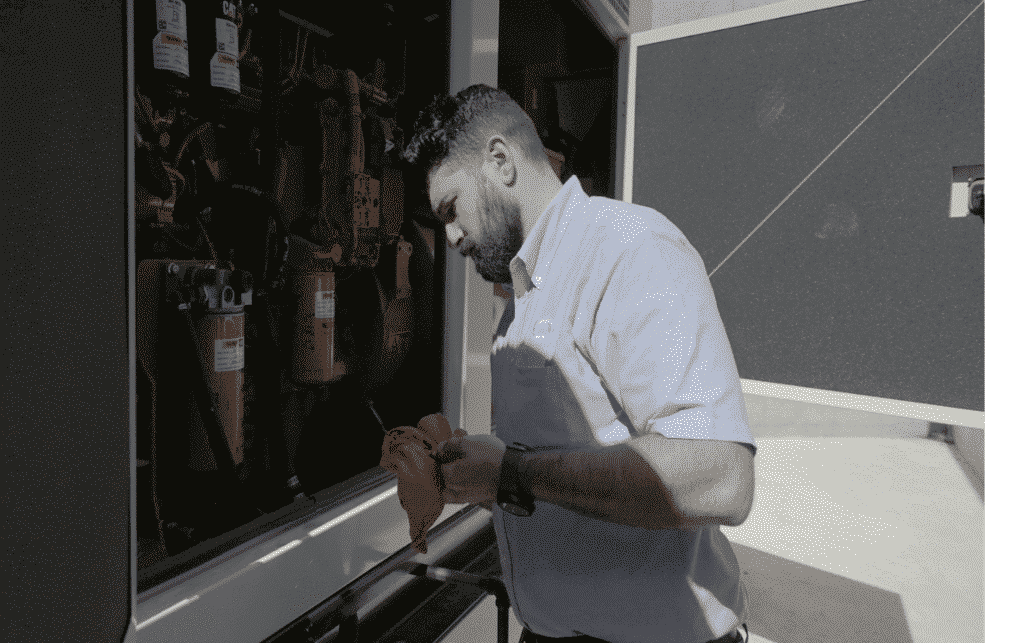
PREVENTIVE MAINTENANCE CHECKLIST
Creating a preventive maintenance checklist is a great way to streamline your maintenance activities and keep organized.
A “checklist” essentially refers to a “to-do list.” Some of the information contained in a preventative maintenance checklist includes:
- A comprehensive listing of all maintenance tasks.
- Clearly define when each task is to be performed (i.e., frequency of weekly or monthly).
- Instructions regarding the location of the Original Equipment Manufacturer (OEM) manuals–for referencing any information.
- Documentation that confirms the date when any maintenance activities are completed.
PREVENTIVE MAINTENANCE SOFTWARE
Preventive maintenance software is a great tool for efficiently creating and scheduling work orders digitally for preventive maintenance.
These programs will help you reduce the time you would spend manually tracking faulty systems and equipment.
Many preventive maintenance software providers are quite affordable and help you keep all your maintenance history in one place.
Implementing preventive maintenance software will benefit your commercial facility, these programs will allow you to create and submit digital work order forms on one streamlined system, and allow you to modify completed or in-process repairs and maintenance.
Some of these programs take off administrative tasks for the technicians, so they can focus on inspecting and maintaining equipment.
Preventive maintenance software also provides technicians easy access to all the preventive maintenance work orders they need to perform and send alerts and reminders about when the next inspection is due.
Through preventive maintenance software, you could track work orders through their process from start to finish, and receive access to data and trends that show operational downtime, repair costs, and causes of issues.
CMMS SOFTWARE
When you use CMMS software for preventive maintenance, it is very important to ensure that preventive maintenance is one of the available tools or components.
I cannot understate the essence of this program as it creates a difference between effective machines and faulty ones in need of repair.
The preventive maintenance tool is incorporated into a user-friendly interface easy to interpret and understand.
If the software has complexities of its own, then it would defeat its overall purpose since sophistication would discourage technicians/employees from using it.
The con to using CMMS software with an intuitive preventive maintenance tool is the overall cost that is involved.
Although the results would speak for themselves during a long-term course, during the purchase period, the capital investment seems huge.
Even in text, the whole working of the component sounds complicated, and in reality, it is.
But looking at the bigger picture, there is usually more to gain than lose when equipment repair, which can be prevented, becomes an enormous cost, especially when it’s a lot of equipment we’re talking about.
CREATING AN EFFECTIVE PREVENTIVE MAINTENANCE PLAN FOR YOUR FACILITY
Preventive maintenance is an essential factor for facilities management.
The goal of a successful preventive maintenance program is to establish consistent practices designed to improve the performance and safety of the equipment at your property.
The planned maintenance of equipment will help to improve equipment life and avoid any unplanned maintenance activity.
A successful preventive maintenance program depends on the cooperation of all the parties involved.
A preventive maintenance checklist will serve as a guide to monitor, service, repair, and replace equipment parts to curb the risk of equipment failures.
You should take into consideration the following steps when creating a preventative maintenance plan for your facility.
STEP 1: DEVELOP THE END GOAL
Make a list of your organizational goals, the list aids in choosing the right preventative maintenance planning for your facility.
Work history, labor tracking, and planned maintenance will follow in the plan you select.
STEP 2: SELECT PREVENTIVE MAINTENANCE SOFTWARE
There are several preventive maintenance software programs in-use and selecting the right one for your facility is crucial.
There are factors you should take into consideration when choosing preventive maintenance software.
Some of these factors are ease of use, web-based access, reporting functions, and real-time cost.
STEP 3: IDENTIFY ASSETS AND EQUIPMENT HIERARCHY
A clear definition of the relationship between the highest level of equipment and the smaller units in your facility will help you identify the pm tasks you should prioritize.
Adhering to manufacturer recommendations about service intervals and the scope of work from the Original Equipment Manufacturer (OEM) is imperative.
STEP 4: CREATE JOB AND LABOR RESOURCES
A preventive maintenance plan includes a list of prescriptive maintenance functions to perform the actual work.
Providing information on the job scope and time to your maintenance personnel gives ample space for the maintenance technicians to schedule the right skills, supplies, and equipment.

WHAT DOES IT COST TO IMPLEMENT PREVENTIVE MAINTENANCE?
The cost of preventive maintenance will depend on labor costs (for large facilities and staff), and the number of machines and utilities you need to improve or protect.
It’s important not to break your business’s budget just to implement preventive maintenance.
You should do what you can and where you can, to avoid future damages to your business caused by preventable accidents.
It can be as simple and as budget-friendly as manually cleaning a ventilation system, increasing lubrication frequency on equipment, or spending one-hour training staff to operate certain machinery safely and effectively.
To determine how much of your budget should be allocated to preventive maintenance, you should:
- Add up the total cost of your reactive maintenance for the past year;
- Consider the value of all your equipment.
This will give you a good idea of how much you might save in the way of reactive maintenance, besides the savings you’ll enjoy from extending the life of your equipment.
No matter your cost restraints, there’s usually something you can do to better protect your business and your employees—and you won’t need to break the bank getting it done!
HIRING THE BEST MAINTENANCE PERSONNEL OR MAINTENANCE TECHNICIANS FOR EFFECTIVE PREVENTIVE MAINTENANCE
As a facility manager, you may view preventive maintenance as an unnecessary cost for your facility, an inability to develop a comprehensive preventive maintenance plan will lead to costly consequences.
An accident or unplanned downtime will harm your process and the facility’s reputation.
The viable recommendation is to utilize experienced, reputable maintenance personnel or contract maintenance technicians, depending on your facility’s size and needs.
Servi-Tek Facility Solutions offers top-notch, customized preventive maintenance programs and services to exceed the goals and needs of your facility.
Are you looking for professional commercial facility services near you? Contact us today to get started.