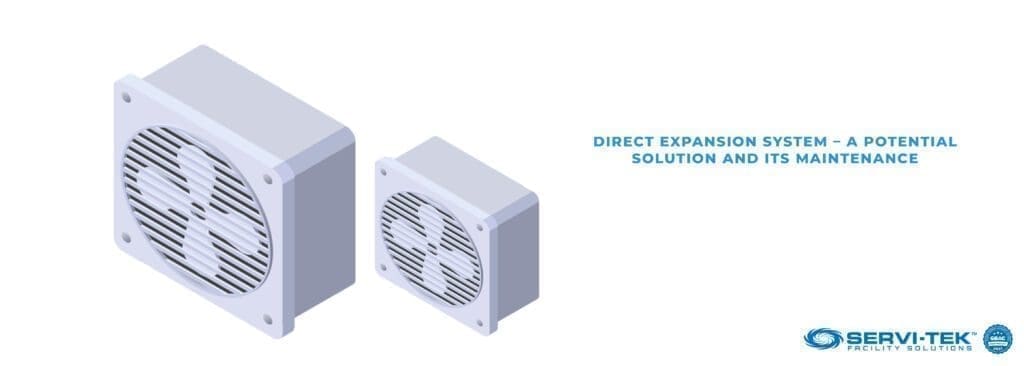
Today, the HVAC unit is one of the most important systems in any commercial building.
If you take a closer look at the market, you will be amazed at the sheer number of options available – which oftentimes can be confusing.
Fortunately, HVAC units are broadly segregated into two primary types:
- Direct Expansion Units, also called DX units or DX central conditioners
- Chiller units also called CHW units or chilled water air conditioners
Although both types of HVAC units are widely used today and comprise of similar cooling components, (including a refrigerant, dispenser, evaporator coils, etc.), they differ fundamentally.
For instance, DX units work by cooling air, and CHW units work by cooling water.
This guide will help you understand the finer nuances of the DX cool air devices and why they are preferred.
Keep reading to learn all the useful information, so you can make the right choice for your commercial building needs.
Parts of a DX cooling unit
For all its complex functionality and versatility, a DX unit comprises 3 harmonious parts. These parts include:
- The refrigerant system, which is also called the plant room. This is the heart of the entire system.
- The air handling system, which is also called the air handling room. This part works like our lungs, providing fresh and cool air to the entire room.
- The air-conditioned room, which enjoys the work put in by the entire system.
Knowing the dynamics between these three parts will help you understand what makes a direct expansion unit work efficiently, and what doesn’t.
The refrigeration system or the plant room
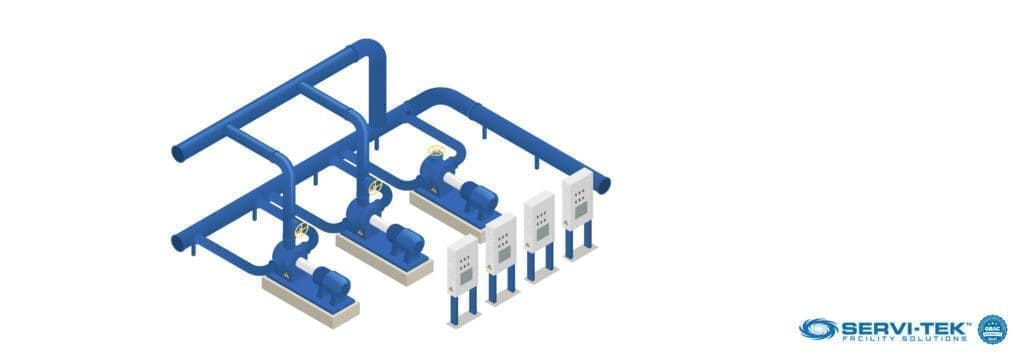
This is, perhaps, the most hard-working part of an air-cooling system.
Ironically, it “cools” air by heating it first, and then running it through friction processes that result in refrigeration. For this, it needs a strong refrigerant.
A refrigerant is typically a chemical compound used to produce a cooling effect through repetitive cycles of heating and cooling.
For this, the refrigerant itself may go through repeated transformations between liquid and gaseous states, until the final cooling temperature is achieved.
Water cooling units work similarly, except that they use water as their primary refrigerant. This also causes some loss of energy efficiency, as covered in a later section below.
How does refrigeration occur in a commercial HVAC unit?
For this, the unit works through iterative refrigeration cycles as described below.
The refrigeration cycle
- The air is collected from the room, through the DX unit’s vents. It is sent through a compressor fitted with a high-pressure line, to generate heat. In some cases, an additional heating pump may also be used to speed up the process.
- The resultant heat causes the air collected to be vaporized into a hot gaseous matter. This is also referred to as refrigerant vapor.
- The hot gas vapor is then sent through a condenser coil, which is constantly cooled using an industry-standard fan. Through this process, the hot vapor is transformed into a cooled liquid.
This completes a single cycle of refrigeration.
But only one refrigeration cycle may not be sufficient to achieve the desired temperature.
So the cooling liquid that emerges from the condenser coil is repeatedly sent back through the same cycle until the final desired temperature is achieved.
The process of refrigeration is facilitated through the use of a reverse valve or an expansion valve, as required.
As the last step, the cooled liquid refrigerant is sent to the air handler unit, through the liquid line, to be dehumidified and dispensed to the final destination unit.
As a general note, in a split-system circuit, the condenser is typically located outside the room that needs to be cooled. This setup also allows outside air to be used to hasten the cooling process.
The air handler unit or the air handler room
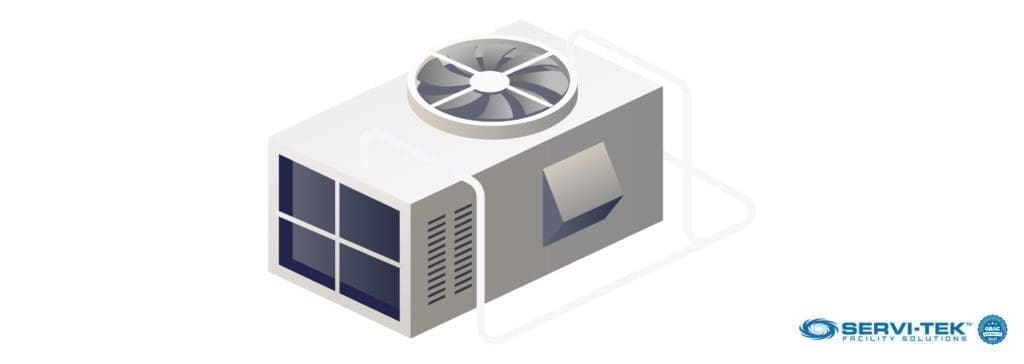
If you thought the step above was the final one, know there are plenty more following, as the processes behind are more complex than they appear.
The air handling unit is responsible for collecting the cooled air and dispersing it to the designated room.
The refrigerant liquid is sent through yet another coil/fan combo. This dehumidifies the matter to produce chilled air.
Yes, this is finally where it all comes together and the magic happens.
The air-conditioned room
At this point, you may have already figured out the rest of the system.
The targeted room is now receiving the returning air – now cooled to the desired temperature, through ducts, and released into the rest of the space through vents.
The cycle of compression, condensation, and evaporation is triggered continuously to regulate the air within a room to the desired temperature.
To summarize the above information in a more simple form, think of it as the following steps:
In Refrigerant unit
- One Refrigeration cycle = Stale air from room -> Compressor -> Refrigerant vapor -> Condenser -> Refrigerant liquid
- Refrigeration process = Multiple refrigeration cycles until desired cooler temperature is achieved.
In Air handler unit
- Refrigerant liquid -> Evaporator -> Cooled air -> FilterR -> Cooled, purified air.
In Air condition unit
- The cooled and purified air is dispensed into the room through the air condition unit’s vents.
Placement and distribution of different components of an AC unit
There are several trigger points where the transformation of matter – from air to gas to liquid and then back to air again – happens during the refrigeration cycle.
This includes:
- The compressor with the heating element, where air/liquid is transformed into a hot gas.
- The condenser with the cooling fan, where the hot gas is transformed back into refrigerant liquid.
These two work together in iterative cycles to complete the refrigeration process. Hence, they are often bundled together and stored in the refrigeration unit.
Outdoor air can also be collected and used to hasten the heating/cooling process. For this reason, the refrigeration unit can be stored outside a room/ building, as is typical in the case of split-system circuit ACs.
Evaporator with dehumidifier + diffuser
It must be stored at the actual location that needs cooling. The evaporator portion is hence installed inside the room or building.
Depending on the size and load of the AC, additional ducts may be installed to dispense refrigerant liquid from the air-handler to the air-conditioned spaces.
The constraints of using DX HVAC systems and suggested alternatives
R22 is a common refrigerant used in DX systems. However, it has been marked as an environmental hazard by the federal government, as it contributes to depleting the Ozone layer.
Hence, if your old DX unit runs on R22 and you wish to integrate it with a larger central unit, this is a good opportunity for you to revamp your old system.
On top, the spare parts are not easy to find.
Another constraint is the distance between the condenser and the air-handling unit. It should be kept to a minimum possible value, so there is no undue pressure drop, causing unexpected loss of heat.
In older installations, the central unit was kept at a higher level compared to individual air handler units. This made the drop in pressure more pronounced, contributing to shrinking efficiency, and resulting in a failed system.
For this reason, check with your local contractor if the DX unit can remain energy efficient in the real estate where you want it installed.
Reasons to choose a DX cooling unit
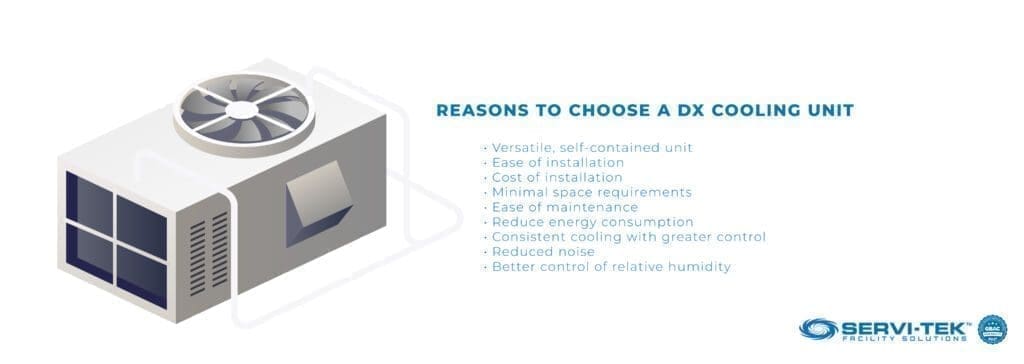
The reasons and benefits of choosing such units, in smaller or large buildings, are not few.
Here’s how the system can benefit you:
1. Versatile, self-contained unit
Unlike chiller units which are fitted into larger central air-conditioning systems, DX units can be self-contained.
It means they can be independent of the messy wiring and tubing that often accompanies a large HVAC installation, especially when they are installed inside the room which is intended for heating/cooling (like split air conditioners).
They can also be installed outside a building (like window air conditioners), or even as part of a central cooling system.
In this case, each DX unit can be independently operated. It comes in handy if you are renovating your building, or you want to add/remove a new room for cooling from your central system.
DX units allow you to cool and ventilate new portions of a building without messing with the existing HVAC system.
2. Ease of installation
Because the DX packaged unit can be installed independent of existing systems, the process is fairly fuss-free. It is easier and safer to consider a DIY with DX units than with liquid cooling units.
3. Cost of installation
This is an organic evolution, due to the system’s design. For instance, CHW units need to be consolidated with additional cooling towers to transfer heat or chilled water across rooms and to suitably ventilate or cool a room.
This can be avoided in a DX unit, which translates into more savings for you.
4. Minimal space requirements
Regardless of the proportions of your facility, it is easy to find a DX unit that is suitable for your space.
They are also less bulky than other cooling units. They can hence be made to fit into less space, even in rooms with low ceilings or limited wall space.
5. Ease of maintenance
The big hassle with CHW central units is their ability to impact an entire building when one component is affected.
A DX unit can, individually and independently, control the air and ventilation of a single room. This makes it easier for maintenance, even when they form a larger part of a central cooling unit.
DX units can also be removed/uninstalled without affecting the overall commercial HVAC setup. For all these reasons, they remain the popular choice for their ease of maintenance.
6. Reduced energy consumption
It may come as surprise to many, but consider this: DX units directly work to cool the surrounding air, rather than cooling the liquids that will be used in the process.
These units require significantly lower amounts of energy to cool an entire room as per your needs.
Also, the fact that they can be individually controlled, independent of other cooling units in a building, helps to further increase energy savings.
7. Consistent cooling with greater control
Because of their versatility of operation, DX units for a room can be powered on or switched off without affecting the rest of the building.
This means that when a room is unoccupied, it can be powered off, leading to energy savings. This trick can also be used to run DX units at full load when a room is completely occupied.
8. Reduced noise
When you think of a traditional cooling unit, the first thing that comes to mind is the continuous humming sound that accompanies most units.
If that’s the case, you will be pleasantly surprised to know that DX units have evolved greatly. The surrounding noise from the modern systems is almost indiscernible, with a noise criterion of 35.
9. Better control of relative humidity
According to Mayo Clinic, the ideal humidity within a building must be kept between 30% and 50%, for good health.
If the levels are too low, we become dehydrated and our skin goes dry. If they’re too high, it can even impact our lungs.
But maintaining this balance is a big challenge for liquid-cooling systems, especially in hotter temperatures, since they work by dispensing chilled liquids into the atmosphere.
On the other hand, DX units are designed to absorb excess water from the atmosphere to produce a colder temperature.
With this, they are more effective at maintaining the ideal relative humidity in a building.
Why a DX system is more efficient than a Chilled Water (CHW) system for cooling purposes
Both DX and CHW units have their uses. But DX units tend to have an edge in the market, as they offer more versatility and benefits.
Here are a few of the advantages:
1. Straightforward process: The ultimate goal of an air-conditioning system is to cool the surrounding air in a room. It can be addressed in a straightforward manner in a direct expansion system.
On the other hand, CHW systems use a middle agent like water, before transferring the heat/ cold to the surrounding air. This is naturally more inconvenient than DX systems.
2. Loss of heat during the cycling processes: The straightforward process design lends itself to increased energy efficiency.
In DX systems, there is no time lost in heating/cooling a middle agent like water.
Also, the transfer of heat between the middle agent (water) and air can cause loss of heat, further delaying and extending the process. This is avoided in DX systems.
3. Minimal loss of heat/ cold: Water-based cooling systems make use of cooling towers, consolidated with installed cooling units, to make the surrounding air cooler.
However, this also requires the water to travel a considerable distance, across internal ducts, before its temperature can be transferred to the air that needs to be cooled.
The travel time between the chiller and the final air-handling unit further causes undue delays. During this time, there may be an additional loss of heat/cold in the refrigerant.
This can trigger the need for further refrigeration cycles until the desired room temperature is finally achieved.
4. Proximity and ease of operation: The possibility for the different components of an air conditioner to be closely packed, and relatively self-contained, is higher in DX units.
This automatically increases its efficiency, as there is less dependence on other non-contained units. Even in a central conditioning system, the individual components are arranged such that they support maximum efficiency.
On the other hand, water-chilled units are bulkier, occupying more space, and sometimes even scattered across a building.
In some cases, an additional pump may also be required just to transport the chilled water from one component to another.
These additional needs automatically warrant more time and resources to provide the final desired cooling effect.
What you need to know, about maintaining a DX unit for HVAC needs
As stated above, a key advantage of choosing a DX unit for your comfort is its ease of maintenance.
For optimal performance, schedule a daily, quarterly, bi-monthly, and yearly routine, as captured below.
Daily inspection & maintenance routine:
- Ensure that all air inlets to the DX unit are clear (including the compressor), and the path is free of material impediments.
- Ensure that all belts and fasteners used in the system are adequately tight.
Quarterly inspection & maintenance routine: (This is also recommended when beginning or ending a season or cycle of operation):
- Check that all automated and manual components of the unit are working as expected.
- Check operation of all-electric components, including magnetic switches, motors, etc. Also, check if they are suitably insulated.
- Check the refrigerant and oil levels in the device.
- Check if all fans within the device are working unhindered.
- Thoroughly clean filters, coils, and the unit of the air conditioner.
- Thoroughly inspect and clean the drainage systems and evaporator.
Half-yearly inspection & maintenance routine:
- Thoroughly clean all key components, including coil, condenser, and evaporator.
- Check tension of all straps & belts within the unit, and adjust as required.
- Check operation of all automated units.
- Lubricate motor bearings and the cooling fan in the DX unit.
Yearly inspection & maintenance routine:
Unlike other inspections, a yearly inspection should also budget for repairs and maintenance. This should include:
- A thorough inspection of the main coil. Check for damages arising due to a leak in refrigerant liquid or oil.
- Inspect if the moisture indicator is working as expected. “Wet” indicators warrant maintenance within the system.
Frequently asked questions (FAQ) on Direct Expansion Systems

1. What are split air-conditioners? Are they the same as DX systems?
Yes, any “air” conditioner is a direct expanded system, without the intervention of any external cooling agent – like water or other liquids.
Air itself is heated and cooled in cycles to produce the desired cooling effect and transform into liquid refrigerant.
In a split air conditioner, (also called a split-system circuit air conditioner), the different components can be appropriately divided into two separate bundles. One bundle containing the compressor/ condenser combo can go into an external package, fitted outside the room (typically in the window).
The other bundle containing the evaporator unit is fitted inside the room which needs to be cooled.
In some cases, the compressor/ condenser combo may be installed away from the building. In this case, they are connected to air conditioner units installed within individual rooms (with the evaporator component), through appropriate ducts.
2. What are packaged air conditioners and how do they differ from direct/ split air conditioners.
Packaged air conditioners are essentially direct expansion air conditioners because they also use only air as the primary refrigerant, with no other external liquid needed.
However, they include all components in a single box. They are also bulkier, therefore useful for cooling larger rooms.
3. What type of direct expansion cooling system is more appropriate for my office building?
All three systems have their advantages. Hence the right choice would depend largely on the real estate area of your office. While this is the rule of thumb, it is always best to check with an expert based in your actual office area.
A reputed facility maintenance provider like Servi-Tek will be able to guide you in getting the best long-term benefit and energy savings you want from your building’s HVAC system, based on a reasonable initial investment.
4. What are the high and low sides of an air conditioner?
The “high side” of a DX system refers to the high-pressure tube connected to the compressor. This is responsible for providing the heat that turns incoming air or liquid into a hot gaseous matter.
The “low side” of a DX system is the low-pressure tube connected to the condenser coil. This is also exposed to a fan. The friction between the temperatures causes extreme cooling, thus transforming hot vapor or refrigerant vapor into refrigerant liquid.
As a safety precaution, these may be marked on an air conditioner to keep them away from easily combustible surfaces.
5. I have a central air-conditioner installed in my office building, but some areas are receiving the poorest ventilation. What could be wrong and how to fix this?
This question is best addressed on-site, through a certified expert from a reputed team of commercial HVAC experts.
The contractor can supervise all components, diagnose the root problem, and thus recommend the best way forward to address your cooling needs.
With this said, here is a snippet of some of the factors that come into play.
Quality of central unit
A central AC system typically comprises a heavy-duty central unit housing the main compressor + condenser combo equipment. This is where the refrigeration happens, and the subsequent refrigerant liquid is transported to individual rooms.
If there is any fault in the central unit, then all rooms are likely to receive poor quality conditioning.
Also, many older systems make use of R22 as a refrigerant, which has now been marked obsolete for several reasons. One, it is considered an environmental hazard. Two, it brings down the quality of refrigeration over time, until the unit’s lifespan is significantly shortened. Hence the central unit needs to be checked for this possibility.
Ductwork
Oftentimes, ductwork may be the make or break component of a central cooling system.
The central unit can provide top-quality refrigeration with no leaks. However, if the ductwork allows leaks or worse, is faulty, the individual rooms are bound to suffer.
Due to this reason, the contractor typically begins his way by checking the room with the worst ventilation and then moves towards the central unit.
Another issue is older ductwork, which is suitable for heating a room, but insufficient to cool a room.
Different types of direct expansion systems
There are three main types of direct expansion systems:
1. Window air conditioner: Most economical, quick, and easy installation, perfect for smaller spaces like studio apartments, single rooms, etc.
2. Split air conditioner: Provides higher energy efficiency than window AC’s, perfect for areas under 1000 square feet or smaller offices with open areas.
3. Central air conditioner: Best for areas larger than 1,000 square feet, especially if you have multiple rooms. It provides more energy savings and efficiency than split ACs in the long term but comes with a sizeable initial investment in comparison.
Installation and Maintenance of DX Coils in Commercial HVAC Systems
Depending on the situation, the right solution for the facility manager can be replacing the HVAC’s direct expansion coils.
The following broad guidelines can help in doing this task safely and appropriately.
Coils, Fins, and Fittings
The direct expansion cooling coils are usually based on a counter flow design. It means that the entering air face is the DX coil’s suction face. One to two rows of hot water coils is known as bidirectional coils.
The regular steam coils are considered “header position vital”. This means that the coil’s low point must be the condensate return point of connection.
These standard coils should have a maximum of two rows. If you find that the original coil exceeds two rows, it could mean that the application or design flaw has occurred. Consult with a facility maintenance expert in this case.
FPT’s or female pipe threads, MPTs or male pipe threads, and unions are mechanical fittings that will require a flexible sealant. A Teflon tape, a superior pipe dope, or a combination of these may be the best.
In time, thermal contraction and expansion may cause the joints to loosen. In this case, the mechanical fitting can be tightened using a backup wrench.
You should avoid lead or tin soldering. In the case of fins, slight distortion may occur at the time of installation. You can straighten the fins with the help of a fin comb.
After the Installation
After installing the water coil, you can carefully open the supply valve and fill the coil slowly with water. Make sure the outlet valve is shut at this time.
If required, you can vent the air from the water coil by removing the vent plug. Make sure to avoid the water hammer effect, which could take place if there is a high-pressure system or a large coil.
Once the coil has been vented and filled, carefully open the outlet valve to further ensure the removal of air from the coil.
The next step is to check for any leakage. DX coils are pressure tested to prevent leaks, but it is important to check for any potential errors. If everything is in order, you can open the outlet water valve fully and activate the system operation.
You can also install refrigerant-type coils using the same procedure guidelines in general. Following the installation, remember to pull and hold all the refrigerant coils at a high vacuum for at least one day.
This way you can make sure that the risk of acid production in the HVAC system is minimized and all the moisture is taken out. If compressor failure causes the system breakdown, you must clean the complete system and neutralize it to protect the copper material present in the new coils.
In evaporator coils, the point of gas connection should be positioned at the coil’s bottom to protect the coil from getting oil bound.
When it comes to condenser coils, the point of liquid connection should be positioned similarly. While brazing refrigerant coils, it is vital to solder using at least 5% silver for safety.
Coil Maintenance
The coils must be maintained and rinsed at least once a year with a minimally acidic cleanser. If it is necessary to use a stronger cleanser, repeated rinsing is essential.
The alkali or acid in a strong cleanser can damage the coil’s aluminum fins. Therefore, with thorough and careful rinsing, you can improve the longevity of the coil.
You can straighten any fins that have become bent with the help of a fin comb. Apart from care and periodic cleaning of the coils, you may not require any other coil maintenance.
Managing a direct expansion system requires training, knowledge, experience, and professionalism.
At Servi-Tek, we have a certified team of experts available to address your AC cleaning, servicing, and maintenance needs. Contact us now to find out more.
