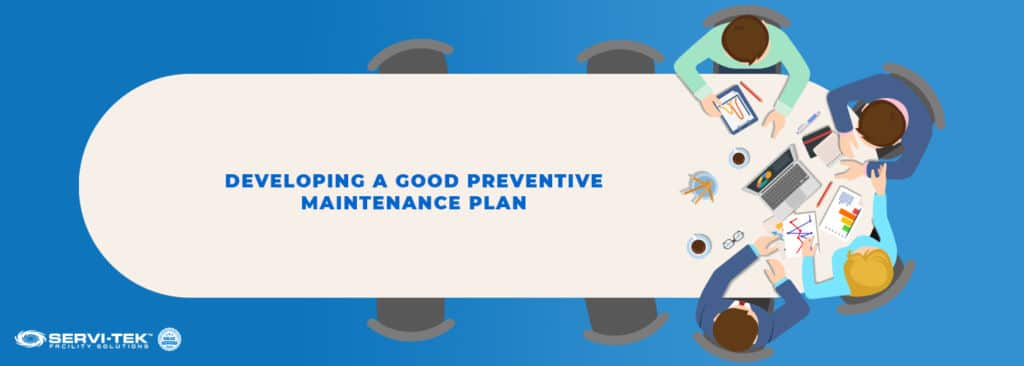
Developing A Good Preventive Maintenance Plan
The American Society of Heating, Refrigerating and Air-Conditioning Engineers (ASHRAE) recently posted important information regarding preventative maintenance strategy and best practices. Let’s take a closer look at short-term and long-term maintenance tasks that maintenance teams and facility management personnel use.
We will address why companies ranging from smaller businesses to large enterprises employ maintenance technicians and other maintenance personnel. A successful maintenance strategy takes a proactive approach toward potential problems and demonstrates care, prolongs asset life, and should cut costs.
Preventive maintenance activities often involve the preservation of parts, equipment, and critical assets. Organizations have workers and team members perform
preventative maintenance tasks (PM tasks) that are part of a good preventative maintenance plan.
The main types of preventative maintenance tasks are performed on a specified time interval or as indicated in a preventative maintenance schedule. A good PM schedule follows a regular preventive maintenance plan that includes mandatory tasks and non-mandatory tasks.
A preventative maintenance program (PM program) might involve routine maintenance on a piece of equipment that will prevent equipment failure. Performing regular maintenance work, such as regarding maintenance of equipment, is a wise decision for maintaining satisfactory operating conditions.
In addition, among the benefits of preventative maintenance programs is reducing the likelihood of failure or a breakdown of equipment. Proper types of maintenance are also some of the best ways for preventing a critical failure and preventing equipment downtime.
For example, downtime is often a worst-case scenario for plant facilities or a manufacturing facility that hinders production throughout the entire organization. Perhaps a major piece of capital equipment is neglected by not conducting proper inspections or completing oil changes.
Understanding A Preventative Maintenance Checklist
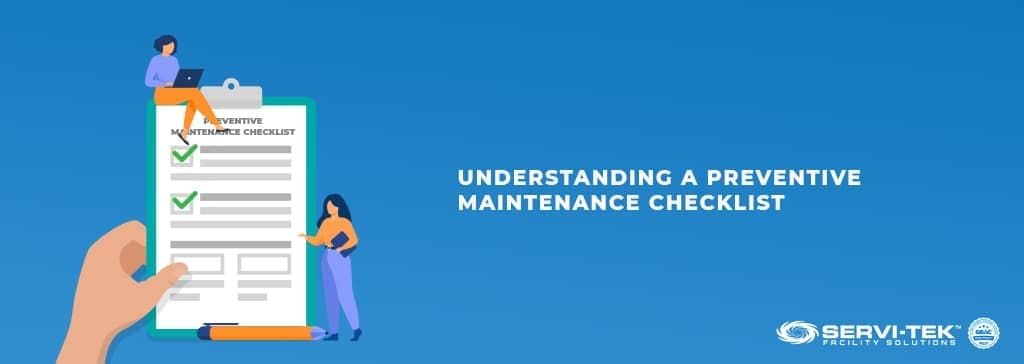
Regardless of the type of maintenance involved, historical data suggests that effective maintenance management systems use checklists regularly. A checklist is a general term that may contain a list of a large amount of equipment in a building.
Even when done by hand, checklists may represent a comprehensive list containing each task, place, or type of inspection. A checklist can save much time by guiding you through each step from servicing of equipment to the final step.
One reason for checklists is that it better ensures complete work is performed according to a specific order or sequence. A new preventative maintenance task (new PM task) is often introduced such as one associated with newly installed electrical systems.
Here, a checklist guides a technician i.e., explaining the recommended time of inspection, measurements, adjustments, any spare parts, etc. When you schedule maintenance inspections, they are obvious examples of preventive maintenance that might allow for early detection.
The good news is that early detection can prevent the high costs involved with a possible type of corrective maintenance. Maintenance costs easily get excessive when response times for necessary repairs are slow or other poor maintenance habits develop.
Experience shows that the main difference is that a reactive approach translates to high costs and other such budget issues–. Having a good checklist reduces the amount of work necessary, such as the time needed for the correction of incipient failures.
Preventive Maintenance Software
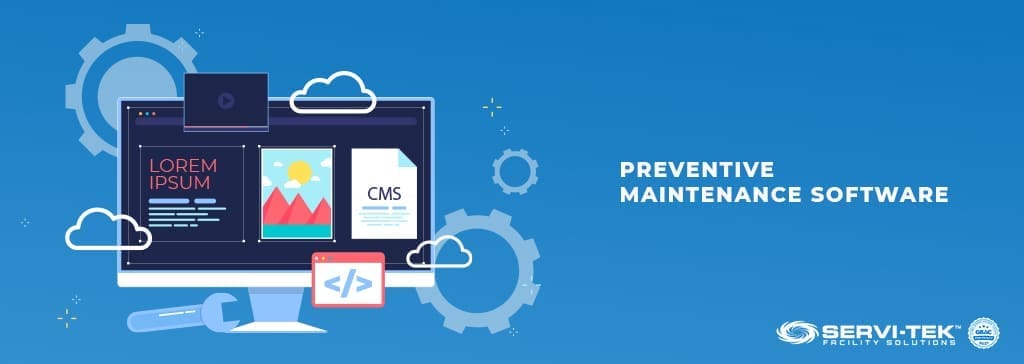
A computerized maintenance management system (CMMS system) or maintenance management software (CMMS software) system employs modern technology and data. CMMS Solutions are a good idea as they allow easy access, data collection, tracking of inspection tasks, and other benefits.
In recent years, the use of a maintenance software program has emerged as necessary for those providing world-class advanced digital maintenance solutions. Today, these programs have capabilities beyond only storing records of past inspections or work orders-part of a robust preventive maintenance strategy.
Decisions regarding CMMS systems should focus on choosing the right program for your specific conditions and key performance indicators. For example, a certain department might have an exact requirement such as real-time tracking of inventory or water supplies.
Predictive Maintenance (PdM)
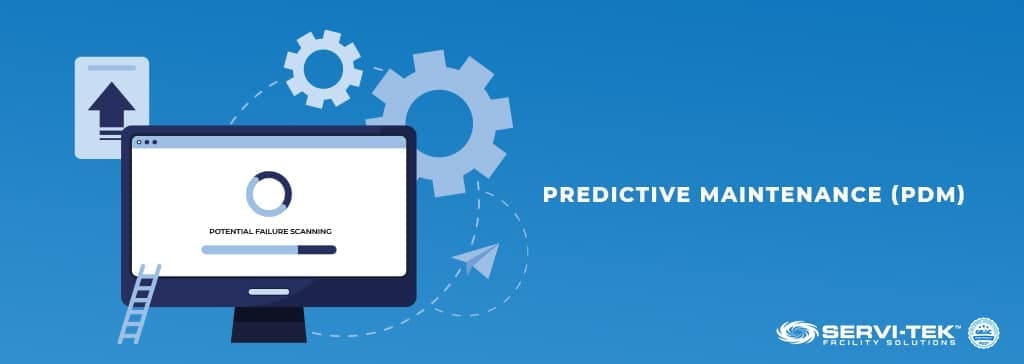
Predictive maintenance or PdM is a strategy that relies on key data for establishing when physical assets will need service. As a critical aspect of asset management today, PdM minimizes costs by proactively performing maintenance before a potential failure.
PdM is increasingly popular among organizations that must avoid failures and the resultant downtime. PdM is distinct from reactive maintenance and the aforementioned preventative maintenance strategies are often used in facility management.
The data used in predictive maintenance software is generated by the Internet of Things (IoT), a concept of continual connectivity. Put simply, IoT is how something remains online and identifies and communicates with other devices.
A basic example of predictive maintenance occurs when your car’s computer generates an alert suggesting you need oil changes. This example would reflect a “consumer-level” application of IoT, which is distinct from enterprise-level applications.
Predictive maintenance functions might involve detecting a piece of equipment’s key indicators for any possible problems or abnormalities. However, a truly predictive system might only perform this monitoring or assessment when there is some likelihood of problems.
The aforementioned example seeks to achieve some of the following:
- Limiting the use of often scarce or valuable resources similar to a preventive maintenance plan is
- Maximizing a piece of equipment or device’s normal operating time or “uptime”
- Enhance the overall quality of operations and optimize functions relative to the supply chain
- Should eliminate the need for deploying reactive measures
To simplify, predictive maintenance functions require an understanding of when a failure is most likely and should limit or eliminate downtime.
What is an example of a type of predictive maintenance schedule? The system might feature a schedule that activates sensors every 30 days that perform diagnostics such as checking vibration activity.
Prescriptive Maintenance
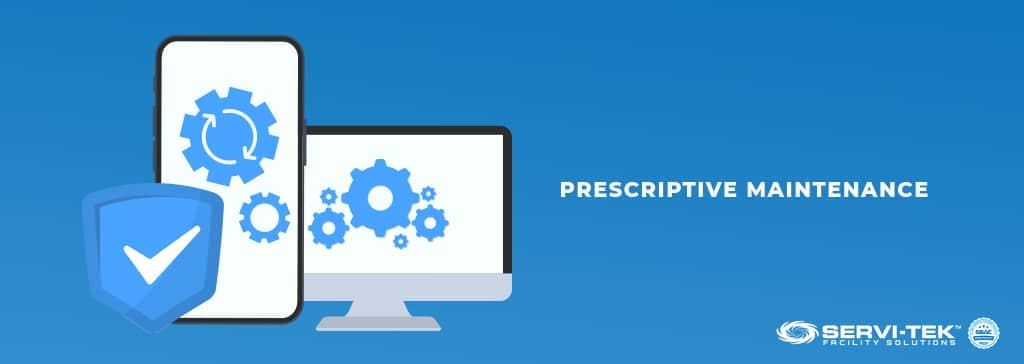
Efficient Plant Magazine recently posted a good explanation of the prescriptive maintenance concept that has emerged in recent years. Prescriptive maintenance developments appeal to those involved with manufacturers seeking further modernization and to properly optimize equipment reliability.
For many years now, sensors capable of detecting activity have increasingly generated more and more data. As part of the IoT, prescriptive maintenance is a field that employs machine learning and fast, automated ways of reviewing data.
Prescriptive maintenance is often thought of as an advanced form of preventive maintenance that also includes most of the tools in predictive maintenance. Prescriptive maintenance goes much further by applying artificial intelligence, which should allow for better optimization.
Prescriptive maintenance programs today sound very appealing to operation and facility maintenance professionals; however, many suggest that the cost is high. Although the sensors now are quite affordable, a certain advanced level of complexity is also a concern.
When we look at all of these maintenance strategies, they all require having access to viable data in real time. The difference is primarily how the data is analyzed and prescriptive maintenance may go further by actually “activating” a response (solution).
Corrective Maintenance
The term corrective maintenance covers maintenance tasks performed in response to a failure, such as involving repair or replacement. For a simple example, a technician replaces a burned-out light bulb. Corrective maintenance is essentially a reactive maintenance strategy as outlined below.
Reactive Maintenance
Maintenance activities performed “reactively” might include any type of response made after experiencing a failure of equipment or machines. In many cases, the first step involves probing or detecting the conditions or causes that created the failure.
For example, in an industrial setting, a maintenance professional might respond with diagnostic tools that show a corrosion-based failure. Inherently, reactive maintenance activities can get costly for a variety of different reasons.
First, reactive maintenance likely addresses a current outage or stoppage of production—which clearly can have financial repercussions. Secondly, reactive maintenance activities often involve acquiring replacement materials or components that may be costly—potentially exacerbated by expedited shipping fees.
Reactive maintenance activities might represent emergency activities, which usually drive up costs and may create subsequent, collateral consequences. For example, a manufacturing facility with phases A, B, C, and D might experience an equipment failure in the A phase.
How Today’s CMMS Solutions Support a Preventive Maintenance Program
Traditionally, building maintenance teams performed a substantial amount of reactive work, such as repairs to a broken-down machine. In years since, busy professionals recognized the importance of considering new IT developments, software applications, and more.
Anticipating equipment failure has proven valuable in preventing unforeseen downtime and production stoppages. When transitioning to a CMMS solution, building owners and facility managers must identify all assets that might need maintenance.
Assets are further prioritized, with those selected being incorporated into a preventive plan and a preventive maintenance schedule. This involves identifying an asset, determining the maintenance frequency, and ensuring that the staff adheres to the plan.
The CMMS will also allow for enhanced productivity, communication, and efficiency, as many preventive maintenance tasks are centralized and accessible from anywhere. The CMMS will eliminate paperwork such as work orders and scheduling books, allow real-time data access, and automate communications.
Provider of Innovative Preventive Strategies for Building Maintenance
For more than 16 years, the team of specialists with Servi-Tek Facility Solutions has developed customized maintenance programs for clients. Our formula combines adhering to manufacturer recommendations, implementing the latest ASHRAE standards, and embracing the use of technology.
Owners, facility managers, and other professionals that oversee commercial building maintenance appreciate how we optimize performance, boost efficiency, and reduce expenses. We encourage you to contact us today for a consultation regarding how can assist your operation.