The Preventive Maintenance Schedule For Your Variable Frequency Drive
You need a variable frequency drive if you have AC motors in your facility or use mechanical means for varying the frequency of output.
VFDs fed with DC voltage may still power an AC load.
You would need variable frequency drives even if the AC motors in your facility require a variable output.
You could be wasting valuable energy if you are not already using VFDs, which is equivalent to throwing good money out of the window.
For example, large utility providers in the oil and gas industry may recognize energy savings in HVAC applications using variable frequency drives (VFD) for regulating motor speed..
VFDs need to be maintained properly if you want their life cycle to be prolonged.
Preventive maintenance of VFD components is much easier than you would believe. You can get the job done by integrating logical and simple steps into your maintenance schedule.
This will ensure that your VFD input drives remain trouble-free for several years.
This guide will cover everything you need to know about VFDs, including their purpose, components, types, and steps for preventative maintenance.
What is A VFD?
VFD Maintenance
So as we were talking about these cooling towers, one of the things we're looking for, regardless of
whether it's an evaporative condenser fluid cooler or open condenser water flow, it's something that has
a variable frequency drive. That means that it's going to control the system based on the need. So it's,
again, tied to an energy management system. Sometimes it can be standalone, depending on what it's
sensing, which is typically temperature control, and trying to maintain a certain condenser water
temperature that goes back to the chiller. So instead of the old on-off or two speed, low speed, high-speed
cooling tower fans, these variable frequency drives can actually slow ramp up the cooling tower
and then bring it down and just let it float at a lower level using less energy, rather than that hard start,
hard stop where you hear the belts chirping, and it's harder on the motors and all of those things.
This is much softer, much easier on the equipment, and has better control with better energy efficiency.
So whenever we're looking at our cooling towers, a new cooling tower, a replacement, or even
modifying an existing cooling tower, we want to look at putting in a variable frequency drive.
Variable Frequency Drive (VFD) is a motor controller type that varies the voltage and frequency supplied to drive an electric motor that is also known as an adjustable speed drive, variable speed drive, adjustable frequency drive, inverter AC drive, and Microdrive.
The device is usually used in HVAC systems in commercial facilities for the purpose of controlling the speed of the motor, fan, and even the compressor.
Think of the VFD as a dimmer in a light bulb. It provides the exact level of brightness you desire without having to resort to the on/off switch.
Also, having one installed allows for variable voltage and may or may not have a bypass switch, meaning that in case the drive fails,, you just need to flip a switch to turn off the component, and your HVAC system will continue functioning as before.
There are several reasons for using a VFD, but the main one is to save energy and machine damage.
Your HVAC system or any other equipment will function well even at lower energy requirements.
VFDs help in reducing noise contamination as well by providing softer stops and starts for moving components within a unit.
Your VFD can control the torque, direction, and speed of an AC induction motor.
It essentially takes the frequency and voltage of a DC bus to convert it to the variable frequency and voltage of an AC output.
Single power pack protective components may contain the inverter and converter in very small VFDs.
Involved control circuitry coordinates the starting and shutting down of power devices through a control board.
The circuit boards dictate the firing of the capacitors in a proper sequence.
Digital Signal Processor (DSP) or microprocessor meets all the decision requirements and internal logic required.
This makes VFD similar to a power supply computer.
Imagine a car with an inexperienced driver that slams the brakes and hits the gas often.
The car would experience increased wear and tear.
VFD enables your HVAC systems to transition smoothly between the start and switching of power devices.
This increases the longevity and durability of the unit as a whole.
VFD Types
The AC variable frequency drive and fluid coupling are the most common VFDs used.
It involves controlling asynchronous squirrel cage motors and Voltage Source Inverter (VSI) typology.
Fans and pumps are among the most common applications for these VFDs.
Variable frequency drive has two major types – electrical and mechanical.
Electrical VFDs have the following types:
- Eddy current coupling
- DC drives and corresponding DC motor
- AC VFDs and associated AC motors
Mechanical VFDs have the following subtypes:
- Variable pitch drive
- Traction drive
- Hydraulic hydrostatic drive
- Fluid coupling or hydraulic hydrodynamic drive
- Hydraulic hydro viscous drive
VFD Parts and Components
There are four major power components within a VFD:
- Rectifier: This is used for converting AC input power into DC power
- DC Link: This stores the DC power, which can be used by the converter. The capacitors are usually in the back of the VFD.
- Converter: The IGBT (Inverse Gate Bipolar Transistor) inverter is your device’s heart. It provides the PWM (Pulse width Modulation) output for running under the direction of the control circuit.
- Control Circuit: This component is responsible for the programming and controlling of the VFD. It is essentially the brain of the operation.
Common Operation & Maintenance Instructions
There are three basic categories to the VFD maintenance schedule:
- Keeping the VFD Clean
- Keeping the VFD Dry
- Keeping all Connections Tight
These preventative steps are discussed in detail below.
Step 1: Keeping the VFD Clean
The majority of VFDs fall within the NEMA 1 category, which includes side vents for cooling airflow.
Many VFDs also fall within the NEMA 12 category as well which involves a dust-tight and sealed enclosure.
NEMA 1 VFDs are prone to dust contamination.
Lack of airflow is common if there is dust or debris accumulation on the VFD.
This results in diminished performance from circulating fans and heat sinks.
Malfunctions or failures can be caused when there is dust on the device.
This is because dust tends to absorb moisture.
Consider spraying air through the heat sink fans as part of your preventative maintenance schedule.
In some environments, you can also discharge compressed air through the VFD.
However, you should know that the typical commercial facility air is rife with moisture and particulate matter.
You should use air that is free from oil and moisture.
Otherwise, the process may do more harm than good.
Use a dedicated and specialized air supply or you could run the risk of creating electrostatic discharge (ESD).
Reverse-operated ESD vacuum or non-static generating sprays are good at reducing static build-up.
2. Keeping the VFD Dry
Circuit board corrosion is common damage when the VFD is installed in high moisture areas.
You need to make sure that there is no water dripping on the VFD.
You should also make periodic inspections to check whether the VFD is installed in humid conditions.
This is especially true for NEMA 1enclosure styles. A dry environment is particularly important if you want to prolong the life of your VFD and other electrical equipment.
Condensation used to be a major nuisance in earlier product versions.
VFD manufacturers had to include a type of condensation protection.
The system would not turn on when the mercury went below 32 degrees Fahrenheit.
The software logic is used to prevent the drive from starting.
The same protection is seldom required in the more modern and advanced versions.
Regular heat cycles cause heat sinks that prevent condensation.
You should consider using a thermostatically controlled space heater and a NEMA 12 enclosure if you think condensation is likely.
3. Keeping all Connections Tight
Checking for loose connections is a major step that most people miss out on or do not perform correctly.
You need to make sure the VFD is kept in a clean room before you attempt at making the connections tight.
Mechanical vibrations and heat cycles can cause sub-standard connections.
The same holds for amateur preventative maintenance practices.
It is a bad idea to re-torque screws.
Further, if you tighten screws that are already tight, it could result in erratic operation or bad connections.
Improper connections lead to arcing, which could cause voltage faults, malfunction of fuses, and damage to protective components.
Arcing at the output may result in damage to the power components or over-current faults.
Erratic operation is a common side effect of loose control wiring.
For instance, uncontrollable VFD stops may occur if the Start/Stop signal wire is loose.
The drive speed may begin fluctuating if the speed reference wire is loose causing personnel injury, machine damage, and even scrap.
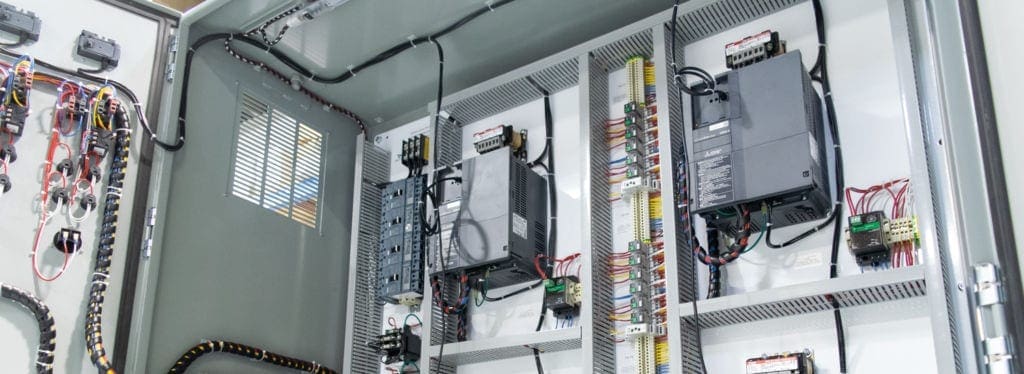
Tips for VFD Maintenance
In terms of maintenance, consider the following tips:
- Always check the internal components while conducting a mechanical inspection such as the fans for foreign objects or any sign of bearing failure.
- Look out for leakage and bulging in the DC bus capacitors may be a sign of electrical misuse or component stress.
- Take measurements of voltage while the VFD is working, as DC bus voltage may fluctuate and indicate capacitor degradation. Capacitors act as filters to smooth out AC ripple voltage, meaning abnormal AC voltage may suggest capacitor failure.
- Read output voltage while keeping the VFD in operation at zero speed. Transistor leakage may stem from higher voltages. The power components at zero speed must not operate. Readings over 60 VAC may indicate component failure.
- Always store spare VFDs in a dry and clean environment and check them when performing your preventative maintenance schedule. This is necessary for keeping DC bus capacitors at peak performance capability and maintaining their high charging abilities.
- Regularly monitor heat sink temperatures using the temperature readout on the display or keypad each week.
- Prevent exposure to direct moisture, humidity, and sunlight, as these have similar electrical components as found on desktops or laptops.
You can achieve impressive performance by following these tips and adhering to your maintenance schedule.
Re-torqueing VFDs is Not Always a Good Idea
Re-torqueing is a popular way of checking tightness in usual preventative maintenance procedures.
However, the task violates the basic principles of mechanics.
It usually ends up doing more harm than good. Screws have maximum clamping power.
The torque is specific to their shape, size, and composition.
You can reduce or diminish the clamping power of the screw permanently by exceeding that value.
You may end up deforming or reducing the screw’s elasticity this way.
Re-torqueing after loosening will cause the screw to have reduced elasticity.
This would again result in a loss of clamping power.
You could end up losing 50% of the clamping power by doing this to the lock washer.
Instead, you should use an infrared thermometer for noting hot connections.
You should also check the torque. Try retightening the screws if they have merely loosened.
Make sure you give the IR check to these screws in your next preventative maintenance cycle.
If you find the screws are loose again, you may need to replace them.
Finally, always perform the tug test. This allows for checking crimps along with screw connections.
Do not do this when the drive or microprocessor is online. It may result in expensive process disturbances.
How to Clean Your VFD Control Panel
You may have worked with an air compressor or seen compressed air in cans.
Resist the urge to use these for cleaning your VFD panel.
They will only end up causing more harm than good.
Instead, clean your VFD control panel using a vacuum.
Compressed air causes dirt and dust to be pushed farther within the crevices of the control panel.
This can end up harming your control panel in the long term.
A vacuum is the best tool for cleaning a VFD control panel.
The dirt and debris can be easily removed without affecting any parts of the electrical connection.
Make sure you properly care for the VFD panel by investing enough time in the cleaning process.
This is the only way for you to get the control panel to work for a long time.
How to Prepare For Maintenance
There are several things you need to consider while performing preventative maintenance on your VFD panel.
Simple and expensive maintenance is all you need to prevent costly repairs down the line.
These are a few ways you can prepare for VFD maintenance and make it easier.
1. Air Filters
Filters are usually present in most VFD control panels.
You should check and change these as and when needed.
The environment and the amount of time your VFD panel runs will determine the frequency of air filter change.
You may want to consider purchasing panels with filters that are on the outside if you are thinking of installing the VFD in a dirty or dusty environment.
Certain VFD panels come with washable poly filters.
You can simply wash, dry, and reuse these to keep the panel clean and cool.
2. Cooling Devices
Fans are the perfect way to cool the VFD panel.
However, these will fail at some point or the other.
There are redundant fans installed in certain panels to keep the panel cool in case there is a fan failure.
Get in the habit of checking your cooling devices whether there are redundant fans or not.
This is important if you want your VFD panel to be functioning properly.
3. Routine Visual Inspection
VFD control panels are often installed in mechanical rooms or remote areas.
They are looked at only when there is some problem.
However, you can prevent expensive repairs if you take the time to check the control panels regularly.
It will also prevent unnecessary downtime.
Carrying out routine visual inspections is strongly recommended.
You should look at both the inside and the outside to see if there is any problem.
Benefits of Performing Preventative Maintenance on VFDs
There are several benefits of performing preventative VFD maintenance on a regular basis. A few of the major ones are:
1. Prolonged Lives
Industry professionals can easily identify operational issues by carrying out regularly scheduled preventative maintenance.
They can correct the issues before they turn into a major system or component failure and involve downtime.
The process helps in extending the reliability and life of your VFD.
2. Better Performance
Preventative maintenance helps in ensuring that the VFDs function for as long as intended.
They are more reliable which translates to better operational capacities and control.
The device can accommodate a broad range of tasks without the inherent risk of failure.
3. Cost Effective
You may feel that regular preventative maintenance initially is cost-intensive.
However, it more than makes up for the amount invested in the long run.
For instance, you don’t need to pay for unplanned replacement and repair costs.
You also lower the risk of the device being completely replaced.
Replacement can cause your equipment to be out of commission for a long time.
This can cause a loss of money in the long run.
Summary – Book Your Preventative Maintenance Today
You can map the performance of your VFD by using an oscilloscope.
You may need to compare it over time for variations with past performance of output signal, input power, and drive.
These signals can indicate early signs of device failure when compared to measurements in an optimized setup.
For instance, you may gauge transformer issues, weakening capacitors, early warning of motor insulation issues, or load and line reactor issues.
VFDs are known to play an important role in several motorized types of equipment, devices, and systems, including HVAC systems.
This makes it necessary for you to maintain the VFD properly and regularly.
Preventative maintenance also ensures the device works for as long as it is supposed to without any trouble.
Servi-Tek is here to help if you want to keep your VFD in good working condition.
We are known to specialize in the servicing and repair of electric motors and variable frequency drives.
We have the necessary skills and knowledge required to keep all your motorized devices and equipment up and running at all times.
You can rely on the Servi-Tek experts to do everything necessary for keeping your preventative maintenance and support on schedule at reasonable costs.
Give us a call today at (866) 454-6185 for additional information about our services and how they can help your facility.