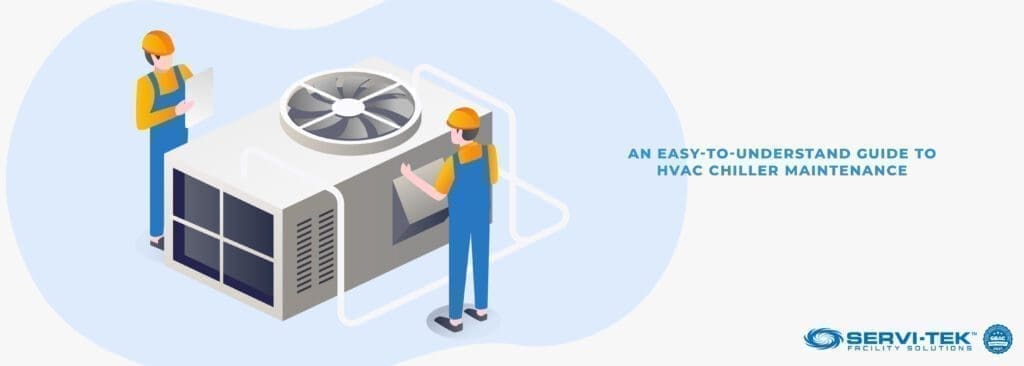
In most institutions, chiller systems are the single largest consumer of electricity. During peak seasons, they might easily absorb more than half of the total electricity used.
What is your chiller system’s consumption and how can you maintain it efficiently and hassle-free?
We’ve set up an easy guide, answering all of your questions, so you won’t have to worry now, or in the future when it comes to your chiller’s performances and costs.
What is a Chiller?
In smaller buildings, an air conditioning unit is typically sufficient. However, larger structures require transitioning to low-pressure chillers.
Buildings tend to generate heat from external and/or internal sources such as the sun, the building occupants, and the equipment used.
Maintaining reasonable temperatures is a must for the occupants’ comfort and the protection of mechanical equipment.
To understand chillers, it is important to differentiate them from air conditioners, as both have similarities involving moisture control and refrigeration.
Air conditioning regulates room temperature and dehumidifies using condenser coils to remove heat, typically with chilled water.
Chillers use vapor compression or refrigeration to lower fluid level temperatures and can be positioned on the exterior or interior of a building.
Chillers have different mechanisms of power including reciprocation, centrifugal methods, screw-driven, and others.
How A Chiller Works

Have you ever wondered how a chiller works?
Chillers use a gas (refrigerant) to transfer heat from an evaporator through a condenser.
More specifically, a chiller operates on the vapor compression or vapor absorption principle. The machine maintains a constant coolant flow to the cold side of a process water system.
The coolant is then pumped through the process, extracting heat from one portion of the facility and returning it to the process water system’s side.
Common locations where chillers are placed include roofs for air-cooled applications or basements for water-cooled models.
Inside A Chiller
The cooling process is either completed using an air-cooled or water-cooled condenser for transferring heat. The air-cooled type is comparable to a radiator used in a car to keep the engine cool.
The air-cooled process involves using a blower to push air across a set of refrigerant lines. Air-cooled condensers typically must have relative temperatures of roughly 95 degrees (F) for effective operation.
The water-cooled option functions similarly to the air-cooled method, however, additional steps are required for transferring heat. The heat moves from refrigerant to condenser water, which is then pushed to a cooling tower for dispersal into the atmosphere.
Water-cooled systems are most common in medium to large facility applications, particularly in locations with a plentiful supply of water.
Traditionally, water-cooled systems have demonstrated excellent consistency for industrial and commercial applications because they are less susceptible to temperature variations.
The smallest-sized water-cooled chillers have a capacity of roughly 20-tons but reach several thousand tons for large applications.
Smaller water-cooled models have less than a 200-ton capacity.
Midsized water-cooled chillers range in capacity from 200 to 500-tons and use screw compressors. Screw chillers trap refrigerant in rotor threads to create compression, where the pressure drops or rises based on the cavity size.
The majority of centrifugal compressors have capacities that exceed 500 tons for more expansive environments. As low-pressure chillers, water-cooled models generally have a longer anticipated service life and may operate much more efficiently.
Another reason why water-cooled chillers are longer-lasting is that the units are shielded from harsh exterior weather conditions. From an installation and maintenance perspective, the added cooling tower may result in higher costs.
On the other hand, air-cooled models use environmental air to cool a condenser and are much better for tight spaces and smaller applications. In regions where water is scarce, air-cooled chillers might be the only feasible option for a commercial facility.
Air-cooled models are also less susceptible to corrosion, erosion, and biological growths such as algae that can result from water flows.
In today’s increasingly eco-conscious environment, air will likely be preferable to water in many future projects. These chillers are less fragmented and most simplistic, which translates to maintenance staff having shorter daily logs and maintenance checklists.
Chiller Parts
The following are the primary components that comprise HVAC chillers:
Compressor: As a critical component, the compressor is responsible for generating pressure and circulating the refrigerant throughout the unit. Always positioned between the evaporator and condenser, compressors may have designs that are centrifugal, screw, scroll, or reciprocating.
Compressors are typically insulated to some extent and are driven by an internal or external motor. The compressor is usually a rather noisy part; therefore, those nearby should wear appropriate hearing protection.
Condenser: The condenser extends from the compressor to the expansion valve and is used to remove heat. As we mentioned before, they can be air or water-cooled.
Expansion valve: The expansion valve expands the refrigerant, which lowers its pressure and boosts its volume to allow for absorbing heat.
If the expansion valve is not used for expanding the refrigerant, the evaporator would be unable to remove heat.
Expansion valves may be thermal, fixed, electronic, or be pilot-operated.
Evaporator: The evaporator extends from the expansion valve to the compressor and gathers heat and moves it toward the refrigerant. The refrigerant transfers the heat to the cooling tower for dispersal.
As the heat is removed from the refrigerant, it transitions to chilled water that is circulated through to cool the building.
Power unit: The power source is typically fixed to the chiller or linked to the chiller using cables. The power unit regulates the electricity and contains breakers, controllers, and monitors, which today have remote monitoring capability.
Controls: Digital control units are the most commonly produced in the market today, replacing older pneumatic-style systems. These older units required regular service of the tool responsible for compression and drying.
Pneumatic systems were vulnerable to moisture, which could lead to expensive repairs, and water control valves required lubrication. Today’s digital control modules require significantly less maintenance and are largely driven by software.
Control units, like the power units, can be mounted directly to the chiller. The new technology allows for real-time notifications such as alarms that immediately are sent to engineering and maintenance staff.
Water boxes: Water boxes control outlets for directing the flow of water from evaporators and condensers, when used in water-cooled systems. Water boxes differentiate between flowing water that enters and exits the system.
Why Is an HVAC Chiller So Important?
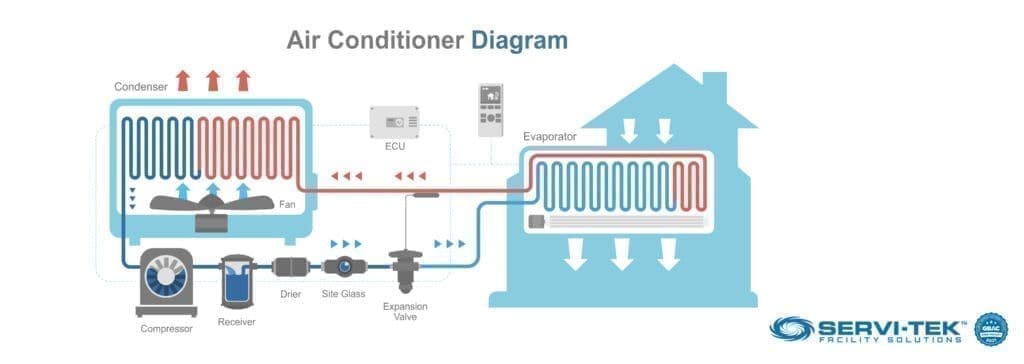
As we approach more extreme temperatures, inefficiencies, refrigerant leaks, corrosion, mud, algae, and other biological growths become costly.
Some improvements include enhanced motor efficiency, improved heat transfer, newer variable-speed drives, heightened flow rates, and microprocessor controls.
Inefficiency in the cooling system of commercial buildings results in massive increases in energy costs and needs for maintenance.
Efficient operation requires more inspections and maintenance of compressors, fans, condenser tubes, water inlets, compressor oil, and measuring variable speed.
Facility managers are often tasked with oversight for HVAC system maintenance, repair, replacement, and other functions.
Many of the most critical decisions involve whether to continue maintaining and repairing an aging system or to replace it. When making these capital decisions, it is necessary to consider the long-term costs or savings that can be realized.
Chillers often constitute a facility’s largest consumer of electricity, and diligent maintenance is critical.
Does HVAC Maintenance Work?
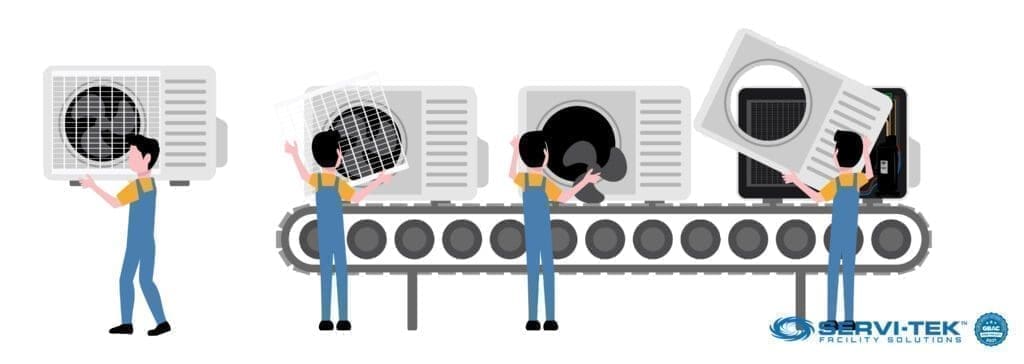
You might ask what would happen if you didn’t pay for a service that prevents problems, such as HVAC maintenance.
After all, the equipment is doing its job to keep your facility at a comfortable temperature. You may not notice a difference if someone comes in twice a year or more to maintain it.
So, what exactly do you get for your money?
Adhering to an HVAC maintenance schedule is the best means of maximizing overall efficient operations.
In many cases, the preventative maintenance schedule is determined based on run-time intervals, which are specified by the manufacturers.
Preventative maintenance work often involves the replacement of small but important parts that are found at most of the system’s junctions. The liquids that serve as the lifeblood of the system are often measured such as the refrigerant and oil levels.
These systems are also equipped with belts, strainers, gaskets, that need inspecting, cleaning, and replacing. The components are known to develop scaling, mold, and other buildups that eventually create inefficiencies, leaks, and other problems.
A building’s water supply may become altered or otherwise contaminated from exposure to buildup and fouling. Some of the leading tests specific to the water supply include assessments of pH levels, alkalinity, and more.
When water is being contaminated by the system itself, it is best remedied by replacing all lines, hoses, pipes, etc. When the water’s properties or quality are otherwise unsatisfactory, additives and treatments are usually implemented to achieve the desired mix.
Why Is Your Chiller Not Working?
There are plenty of potential factors that will hinder the performance of a chiller system. Common examples include leaking refrigerant, obstructions such as buildup, excessive heat that stifles performance, and dozens more.
Most of today’s remote monitoring capabilities that interface with the control system will make real-time assessments to reveal problems.
Older more mechanically-based systems lacked this capability and demanded significantly more troubleshooting work.
Common Problems
Among the leading problems are chiller inefficiencies that surface during the warmest months, which are very problematic for cooling systems.
In many of these situations, there is a compounding effect.
For example, what begins as a relatively minor problem begins to substantially increase the ongoing energy costs. This creates increased stress on the system, which may progress to a major component failure.
Among the many concerns that facility managers and engineering professionals must monitor involves a system’s “lift.”
Lift refers to the variance that exists between hot water exiting the condenser and the colder water generated by the chiller.
When the lift is excessive, the system is placed under increasing pressure to convert the water and refrigerant to desired levels. Among the leading causes of excessive energy consumption is having an overworked compressor.
An excessive lift can also cause create problems and inefficiencies involving fans, coils, and cooling towers. Normal ranges for water temperature are in the 40s (F) for chilled water.
Another common, yet overlooked concern involves installation failures. They can occur when implementing a new system in a new location or upgrading an older system.
Installation-related mishaps often result in 20% decreases in system performance and roughly the same increase in utility costs.
Among the most common mistakes are improperly sized coils being used or faulty connections involving coils. In some instances, installation failures go undetected until a technician discovers them while troubleshooting or testing another component.
How Can You Tell If Your Chiller Needs Repairs?
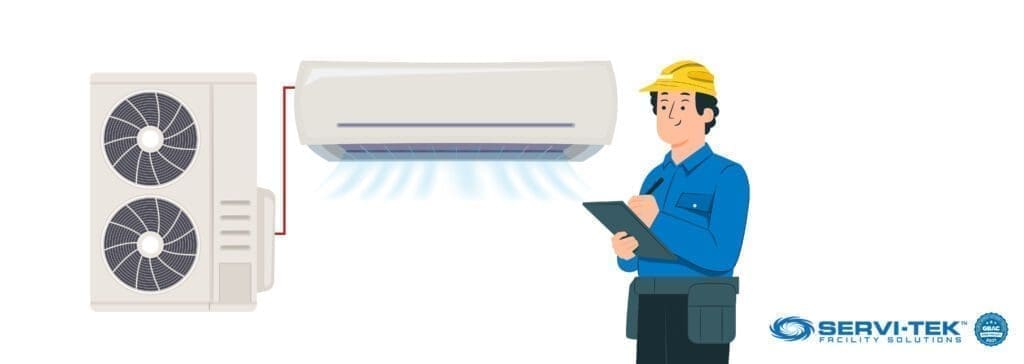
Three of the most common indicators of a necessary repair are as follows:
- Low-pressure discharge: One of the most common causes of low-pressure discharge is a partly closed suction valve, which might occur from build-up. Also, the refrigerant charge may be too low or the existing air temperature might be too low.
- Low-suction pressure: In some situations, the suction pressure may be insufficient, which may be another indicator of a low refrigerant charge or a leak. In many cases, the expansion valve may be partially blocked, resulting in poor flow to the evaporator unit.
- High-suction pressure: When suction pressure is excessive the cooling load may be overwhelming the chiller. This commonly involves a faulty expansion valve that is distributing too much refrigerant.
How to Prevent What’s Causing Your Chiller Problems
Preventing chiller problems begins with being properly organized and tracking all maintenance activities, which is best completed using a log.
Keeping a daily log effectively tracks key indicators including temperature, fluid volume, pressure, and flow rate.
Remote system monitoring options today make this process easier than ever before. Creating and maintaining the log allows for generating reports at intervals i.e., weekly, monthly, or seasonally.
Cleaning the tubes throughout the system is critical for efficiency in transferring heat. The tubes also are subject to obstruction from mineral buildup, algae, and other impurities that reduce performance and potentially increase costs.
The water that is contained within the condenser is another common cause of chiller problems. The water can be treated with an additive that will limit the development of scale and possible corrosion.
The water loops that connect to the condenser are also susceptible to biological growth buildup. Inspecting and cleaning these lines is critical; however, always adhere to the manufacturer’s instructions when choosing agents or chemicals.
Maintenance vs Repairs
Simply explained, repairs refer to the necessity for fixing a broken part, whereas maintenance refers to preventative activities that help your system run more efficiently and last longer.
As a manager, you should expect increased needs for repairs once a machine reaches 15 or more years of service.
It is also at this point in a machine’s service life that decisions arise regarding whether to repair or replace.
Regular maintenance is among the best ways to extend a system’s service life, prevent costly repairs, and maximize overall efficiency.
Based on the age and type of chiller, it is reasonable to assume a service life that extends beyond 20 years. Some of the best practices include high-quality maintenance, adhering to manufacturer recommendations, and properly budgeting to maintain the asset.
What Maintenance Is Recommended?
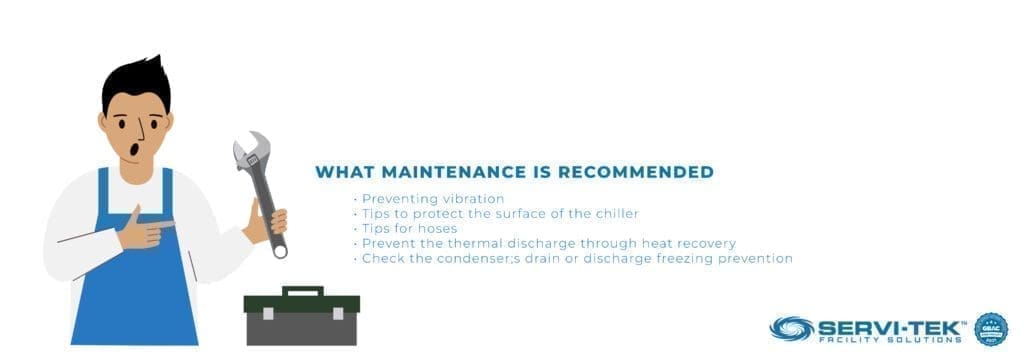
Quarterly inspections, as specified in the manufacturer’s operations manual, should be the first step in basic maintenance.
Regular checks for refrigerant leaks, as well as oil levels, pressures, and temperatures, should be performed by maintenance specialists.
Motor voltages, as well as starters, relays, and contactors, should all be checked. Finally, the technician should inspect the operation of the hot gas and unloader.
Testing the refrigerant charge is another important maintenance task that determines cooling efficiency by ensuring the compressor receives enough.
Refrigerant leaks, in addition to intrusion from moisture or air, may hinder refrigerant charge and overall reliability.
All of the above are just a few examples of what general maintenance should include.
You can find below a more detailed analysis, but keep in mind your own specific needs:
1. Preventing Vibration
HVAC systems often create noise and vibration that result from the movement of air, fluids, and rotating equipment. Sound generally will not exist without the existence of equipment vibration or friction, particularly in mechanical parts.
Managing vibration is typically performed by either isolating or damping. To prevent vibration in the system using isolation, you might dissipate the energy by converting it to heat.
Damping involves limiting the amount of vibration by using internal or external materials to reduce frequency or intensity. Some of the materials commonly used for damping include fluid, rubber, neoprene, or cork, often in the form of padding.
2. Tips to Protect the Surface of the Chiller
HVAC systems are often constructed of durable metallic surface materials, which are strong but potentially vulnerable to corrosion.
For example, a system may be exposed to saltwater in coastal areas or near processing facilities that emit contaminants.
Corrosion can impair the exchange of heat, hinder the function of coils within a condenser, and other problems. Some of the common preventative options include acrylic or polyurethane coatings that are applied as a thin layer of protection.
3. Tips for Hoses
Regular inspection and maintenance of hoses are necessary to detect breaks, wear, and other conditions that develop into leaks. Hoses might last for several years when not subjected to pressure or heat, but the seals might not.
The seals are located at critical junctions and have close contact with other components. In many cases, installers and/or maintenance personnel will overtighten the seals of the hoses.
The seals generally will also have a gasket that requires inspection, which involves removing the hose and making replacements when needed.
4. Prevent Thermal Discharge Through Heat Recovery
Heat recovery is a means of conserving energy by recycling or redirecting heat that is otherwise wasted.
Recovered heat might be useful for heating water, warming the building, and various other purposes. While this sounds good in theory, it might be challenging to capture the heat in quantities to achieve practical purposes.
The options available for using the reclaimed heat are largely dependent on the type of facility and the nature of the activity. For example, hotels or school athletic departments may use the heat to warm swimming pools or for laundry.
5. Check the Condenser’s Drain or Discharge Freezing Prevention
Facility and maintenance professionals must also consider whether a plan is necessary to prevent freezing. A frozen chiller can translate to costly repairs and the majority of manufacturers will not extend warranty coverage for this.
Drainage poses risks associated with excessive air entry that can create oxidation and subsequently cause fouling of key parts. Most major manufacturers offer an optional electric heating unit that prevents freezing within an evaporator.
Another prevention strategy involves moving the evaporator to a climate-controlled indoor location. Another solution uses additives to prevent freezing, such as ethylene or propylene glycol, which has lower freezing points than water.
Insulation of the unit is another potential solution, which commonly involves using cables or strips that are heated. Having the ability to turn these heating elements on and off is critical to limiting costs when the heat is not necessary.
Chiller Maintenance Schedule
An effective ongoing maintenance plan begins with a carefully drafted schedule. Key indicators to track include flow rates, temperature, pressure levels, and much more.
Load balances and limits, for example, can be inspected twice a year. An annual cleaning, electrical system inspection, and other maintenance tune-ups are recommended.
Importance of Preventive Maintenance on a Chiller?
Preventative maintenance is a vital part of overall system performance. Part of this process is adhering to the chiller maintenance schedule and manufacturer recommendations.
Preventive maintenance will ensure that your commercial refrigeration systems work at their best. You’ll also be able to detect possible problems sooner, allowing you more time to address them.
What Testers to Use for Chiller Maintenance
Testing is often an assessment that compares the field performance of the system against factory performance standards.
It is a critical function and must be completed according to the manufacturer and/or regulatory specifications. Samples of liquids are commonly sent to laboratories for testing.
Computerized testing modules are increasingly common today that interface with the system control units and comply with AHRI and other standards.
Risks Involved With DIY
You might find it costly to hire an HVAC specialist to troubleshoot and repair your chiller system.
To save some money, it can be tempting to try a DIY air conditioning repair. Most people, however, lack the necessary information, abilities, or equipment to do so.
The HVAC systems in today’s large commercial facilities are costly and are central to continuous operation. Do-it-yourself maintenance and repairs are discouraged and should be completed by trained professionals.
Chiller Maintenance Tips from HVAC Professionals
As a building owner or manager, you’ve recognized improved service, reduced maintenance and repair expenses, and increased efficiency when using a service provider.
Servi-Tek Facility Solutions is an experienced team of professionals that offers comprehensive maintenance services for commercial clients.
Our staff understands the importance of maintaining your commercial HVAC system. Services include establishing a detailed maintenance plan, troubleshooting, maximizing efficiency, repairs, and leveraging the latest technology to ensure results.
Our technicians are familiar with both the new and more traditional existing systems from the major manufacturers.
Contact us today for a free consultation!