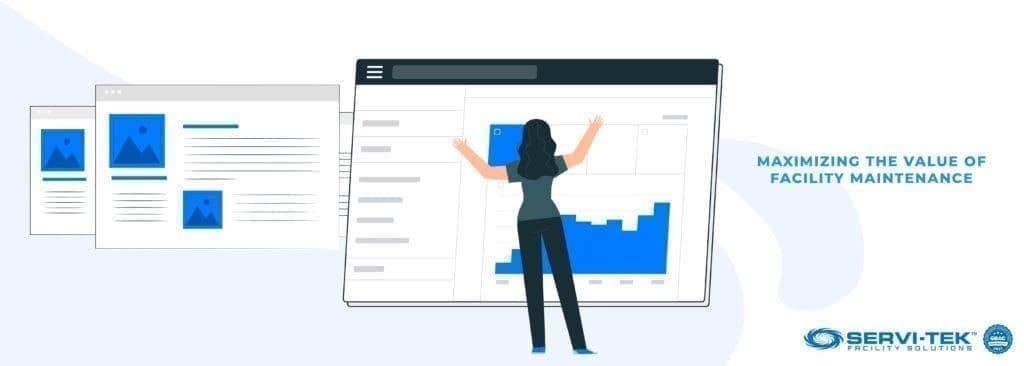
It’s no secret: there is a continued increase in popularity for the U.S. facilities management sector.
While the temporary demand for space within large commercial buildings is lower, emphasis on overall sustainability and facilities management has not declined.
The challenges for most real estate facility management professionals are to achieve enhanced energy efficiency and develop sound practices to maintain their facility operations and physical plants.
Does it sound familiar to you?
Commercial property managers today are challenged to create value – perhaps through outsourcing or partnerships.
One of the biggest challenges faced is to:
- Improve building systems;
- Improve environmental compliance;
- Follow all safety and security standards;
- Boost maintenance productivity.
To get started, the first question that needs to be addressed here is what exactly creating value means?
To build value, property maintenance strategies must benefit the organizational function in many ways.
For example, by improving the capital assets and the service requests processes, all resulting in an increased net operating income.
Real estate value can also be created by building automation that ensures fire safety and preventive maintenance. As a result, the need for costly emergency repairs and the operating expenses are reduced.
A facility maintenance team that successfully maximizes value operates “behind the scenes” often without being noticed by the end-users and clients.
What are the steps to get you started in maximizing the value of your maintenance programs?
Let’s start with the basics:
What is Commercial Facility Maintenance?
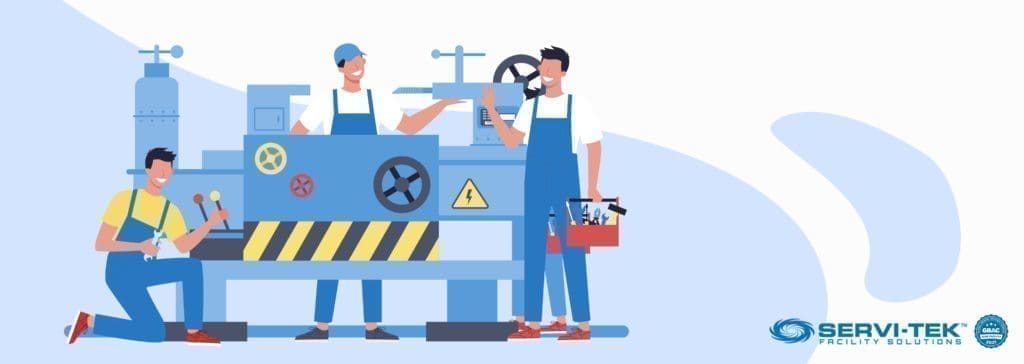
It involves maximizing a building’s functionality and efficiency through servicing key systems and equipment.
The International Facility Management Association (IFMA) mentions the profession of “facility management” was considered legitimate and received recognition in the 1970s.
It was when larger businesses began using third-party service providers for heating, illumination, plumbing, cleaning, sanitation, and more.
The profession also expanded to other commercial activities including corporate office relocation and space planning.
Soon, opportunities for obtaining professional certifications began.
Today’s certifications include:
- Certified Facility Manager (CFM)
- Facility Management Professional (FMP)
- Sustainability Facility Professional (SFP)
And the list doesn’t stop here.
Common types of workers include facility managers, chief engineers, and maintenance experts.
A technician generally performs preventative maintenance, system testing, repairs, and often is an expert in heating, ventilation, and air conditioning (HVAC).
Building maintenance examples of large commercial properties and their related maintenance need Include:
- Office and residential buildings and complexes: Maintaining interior temperature (HVAC), lighting, elevator servicing, hallways floor maintenance, and indoor air quality concerns.
- Retail centers: Tasks include regular roof monitoring and repairs, fire safety and comfort concerns, as well as ensuring restroom plumbing fixtures are properly operating.
- Hospitals: Ensuring systems for safety standards, including fire alarm and fire suppression, are maintained by specialists.
- Universities and other educational facilities: Tasks may include lighting and emergency repair issues such as flooding.
- Hotels: Maintenance concerns may include waste and recycling management, refrigeration, HVAC, fire safety, and exterior lighting.
Why Facility Maintenance is Important
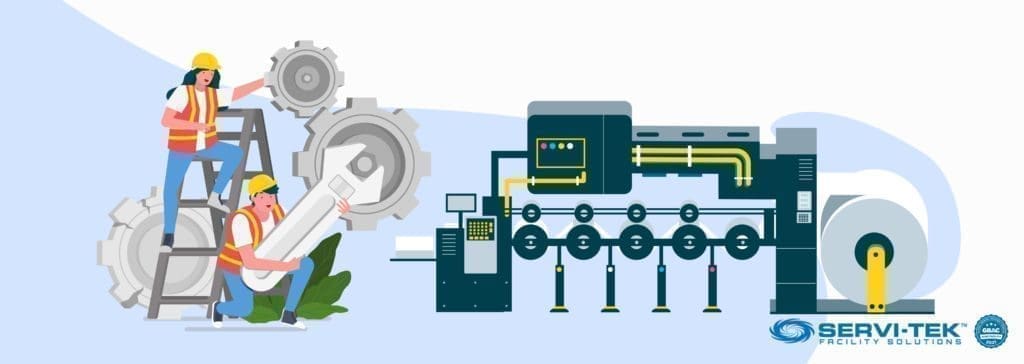
It is an important operational function that typically involves day-to-day tasks and continuity plans that support a building’s systems and equipment.
The maintenance system is designed to achieve optimal levels of productivity and efficiency. A large commercial facility has many critical components and separate systems, along with safety standards, to adhere to.
Although each component within commercial assets is separate, the major ones are interconnected.
When maintenance is neglected or the issues are not properly identified, the building will experience downtime or losses of productivity that can have real and expensive consequences.
Facility maintenance must be part of an overall plan to keep the operations continually moving properly and minimize the highest risk possible.
Employees, tenants, and customers often form negative opinions when they recognize that a commercial real estate property is poorly maintained.
People commonly perceive that maintenance shortcomings are an indication of overall low-quality standards, which is not far from the truth.
Building owners must also remain aware of how poorly maintained assets have a multitude of other negative effects.
Reduced property maintenance effectiveness in a commercial real estate environment may create business risks that increase the potential for accidents and injuries.
For example, a plumbing leak that goes unrepaired may result in dangerous slip-and-fall incidents for employees and others.
Accidents that occur on the premises can increase the costs of worker’s compensation and expose parties to potential liability.
Capital assets typically require regular service and maintenance to be performed according to a schedule issued by the original equipment manufacturer (OEM).
When these parameters are not followed, an expensive piece of equipment may need replacement much sooner than its expected functioning life.
Some capital assets can also require strict compliance with the manufacturer’s maintenance schedule to maintain warranty coverage.
Effective facilities maintenance professionals understand the significance of unexpected downtime that occurs during repairs or replacement of components, which typically affect the entire property.
Emergency repairs, due to the extensive damage, may result in failing to meet key project completion deadlines for a building’s occupants.
Following a proper maintenance schedule will prevent these types of problems and keep the operation moving at peak efficiency.
Why Do Facilities Need to Be Maintained?
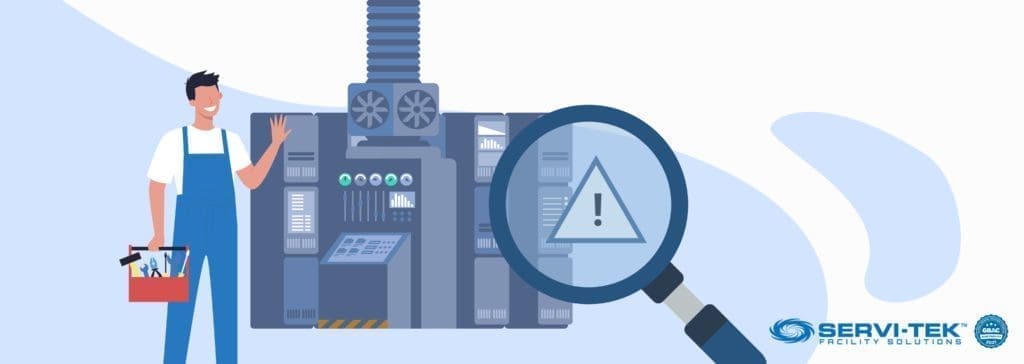
Guidelines are needed for compliance with certain fire safety requirements, environmental standards, or other regulatory measures.
For example, specialized boilers might require detailed inspection, diagnostic testing, monitoring, and preventive maintenance at specified intervals.
Facilities must also operate according to health or safety compliance requirements of local, state, or federal governments.
The Occupational Safety and Health Administration (OSHA) is an agency that provides guidelines for minimizing risks and prevention of possible occupational hazards that create illness, injury, or death.
For example, OSHA requires properties that work with any potentially hazardous chemicals to adhere to operational maintenance practices and procedures.
In this case, all maintenance experts must undergo thorough training regarding preventive maintenance programs.
Paperwork is necessary to properly comply with most facilities’ maintenance activities. This “paper trail” should be documented in a standardized format that ensures accuracy and includes the time and date of completion by the technician.
Today, many commercial facility managers use Computerized Maintenance Management Systems (CMMS) with reporting capabilities that document activity, costs, and equipment assets.
Delays in maintenance requirements have proven to increase future expenses, particularly those related to capital assets.
Deferred maintenance is a term referring to delays (failures) in properly inspecting and/or repairing equipment and systems.
Maintenance deferrals are among the leading causes of potential problems with building systems and equipment.
When proper maintenance, service, and inspection tasks are deferred, it inevitably leads to more costly system or equipment failures. In these situations, maintenance staff is functioning in a largely reactive manner that is generally not sustainable in a facility.
Key Facility Maintenance Concepts
The Assessment Process
Commercial facility and property management professionals must work to develop the framework and procedures for an effective and value-oriented maintenance requirement plan.
The maintenance process must be developed using strategies that will best achieve asset-specific results.
Before testing, or employing different strategies, the maintenance goals must first be clearly defined based on the circumstances and needs.
Some of the common goals will involve prolonging the life of equipment, reducing repair costs, achieving peak efficiency, and energy reduction.
Experienced professionals understand the importance of inventorying the critical building systems and equipment, as well as their current condition and recent work order history.
Operating costs will be among the most critical considerations in the development of a facility manager’s maintenance plan.
Examples of fixed or stable costs may include the wages paid to maintenance specialists or annual service contracts.
Routine inventory procurement for the preventive maintenance process might also be somewhat predictable, particularly when they are purchased in advance.
For example, a piece of equipment that could require frequent changes is filtering for HVAC units.
Other key aspects of the plan include staffing, such as establishing ways of measuring performance, and initial and ongoing training.
Facility Maintenance Work Order
What is a work order process in the context of commercial facility maintenance?
It is a formal request for the performance of different types of maintenance activities. After a work order request is approved, the technician will proceed with the task.
In today’s paperless, digital environment, work orders are usually created in an electronic format or facility management software.
In this example, the CMMS is used exclusively as the means of initiating, tracking and documenting facility maintenance requests in real-time. This creates uniformity and allows any party, including end-users, to view the status of a particular work order.
A work order will typically be assigned a unique job number or combination of characters. If supplies are needed for the completion of the project, a purchase order number may also be referenced.
A work order might request a particular piece of equipment to be tested, inspected, cleaned, or have preventive maintenance performed.
Generally, a work order would is not an ideal way of addressing emergency or extremely urgent matters.
Having your work orders completed through a central computerized facility management platform allows for a more seamless process.
The management and maintenance technician teams can easily access warranty information specific to the equipment or system needing service.
A robust electronic system today can be configured so trained professionals have access from their mobile devices regardless of location.
These best practices will better ensure that work order requests are handled promptly and productively.
Proactive reminders regarding system or equipment maintenance will result in fewer crisis repairs.
Next, we will discuss the three most common types of facility maintenance.
Predictive Maintenance
With today’s robust digital networks, predictive maintenance is a process that can be considered continuous or in real-time.
Predictive maintenance involves remotely monitoring the status of a piece of equipment, system, or another significant property asset.
It is largely based on detecting variations from the normal or expected activity.
First, “baselines” are established, which can be thought of as the “control group” used in scientific research. Sensors responsible for monitoring the status of the equipment will continually detect any unexpected deviations from the baselines.
Maintenance technicians must receive proper training for both interpreting and responding to notifications of potential concerns.
When the sensors detect a problem, electronic systems can generate a work order that describes the concerns for action.
Preventive Maintenance
Preventative maintenance (or preventive maintenance) involves proactively inspecting, servicing, and replacing components within equipment or systems.
The U.S. Department of Energy states that the concept of preventive maintenance was initially created by the U.S. Navy.
Data now suggest that preventive maintenance can reduce overall costs by approximately 12% to 18% compared to basic reactionary property maintenance practices.
It involves the actions taken “before problems occur”, and is extremely cost-effective compared to not stepping in as soon as an issue arises.
Three of the most frequent areas in need of preventive maintenance include electrical systems, plumbing, and HVAC units.
Maintaining these areas is critical, as they represent some of the most expensive systems found within a large commercial facility. They also carry the highest risk of failure and significantly affect the end-users.
Common preventive maintenance activities involving plumbing systems include detecting pipes for leaks, cracks, or other types of wear.
Components such as fans, bearings, filters, motors, and pumps used in the HVAC units need to be inspected at varying intervals.
Electrical systems generally require diligent maintenance, due to possible hazardous conditions and the need of maintaining uninterrupted service throughout the facilities.
Corrective Maintenance
Often considered to be reactive, corrective maintenance involves promptly responding to notifications of known system or equipment failures.
Although a form of maintenance, it is a process of restoring or repairing something malfunctioning. A task that begins as preventative maintenance can sometimes reveal an apparent need for corrective maintenance.
It might be the case when a maintenance technician is performing a preventative service and notices that a significant problem exists.
Because of these scenarios, many seasoned facility managers will ensure their staff is cross-trained in predictive, preventive, and corrective maintenance.
This type of maintenance involves capital assets, HVAC units, plumbing problems, and generally requires trained experts, for the overall safety of the processes.
Because system failures are unexpected, this form of maintenance is extremely time-sensitive. Corrective action may also be dependent on access to or availability of certain parts necessary for making the repairs.
When a maintenance technician detects a potential safety concern, it is generally corrective. Such problems may also be prioritized when they create production delays or periods of downtime, all to minimize disruptions of comfortable work environments.
When combined with effective preventive measures, it helps facility maintenance preserve the equipment by lengthening its service life.
Preventive Maintenance: It’s Your Best Bet
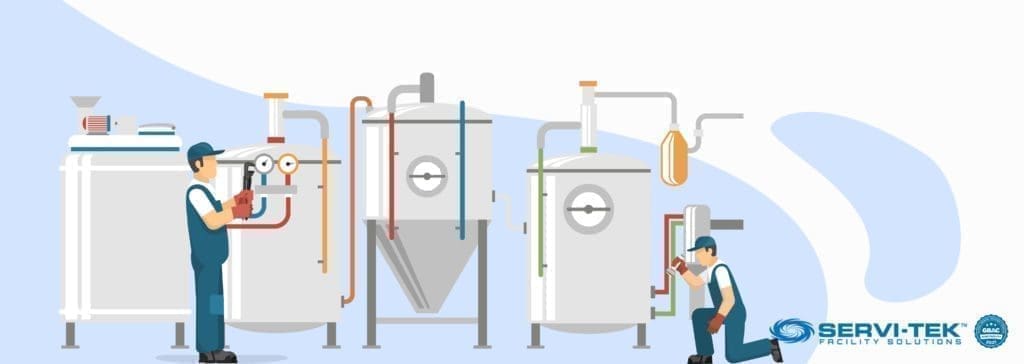
Preventive maintenance should be a key part of any comprehensive facilities maintenance strategy.
The strategy should be based largely on the recommendation of the original manufacturer for optimal results, in the case of equipment. Over time, these proactive measures have proven to result in excellent savings for organizations of all sizes.
Keep in mind that equipment that has been properly maintained is also likely to operate more efficiently.
Capital assets are significant purchases, typically intended to last for a multi-year period and are worthy of diligent maintenance.
Compared to emergency repairs, preventative maintenance is much more cost-effective and less disruptive for the service and maintenance personnel.
Safety standards are another critical reason to develop sound practices. The well-being of employees and all parts within a commercial facility is a top priority.
Injuries from equipment not properly functioning can translate to employees missing work, increased insurance rates, and potential exposure to costly civil liabilities.
Things to Know About Preventive Maintenance
Usually, there is a tendency to lose sight of how maintaining a preventative plan creates value. Management may transition to a form of “lowest-cost” maintenance by insufficiently staffing employees and/or failing to properly train them.
In the vast majority of cases, this results in costly unforeseen facility system malfunctions that could be avoided.
The next two steps in achieving a properly developed preventive maintenance plan involve establishing your equipment database and project implementation.
Preventive Maintenance Database
Effectively developing your preventive maintenance inventory involves reviewing the systems and equipment that need service and determining appropriate service intervals.
It is helpful to know the anticipated lifespan of the equipment and set goals for prolonging this period.
Checklists for preventive maintenance tasks generally have a separate set of time-based and condition-based activities.
Time-based activities are typically performed at some regular intervals and are seen as being “routine.”
Compiling a list of condition-based activities generally poses a greater challenge, as these tasks are not routine, and optional.
All equipment that will be serviced within the preventive maintenance plan should have its model number verified and an appropriate service manual obtained. Each piece of equipment is then added to a full inventory listing and any existing maintenance history included.
Planning must be performed to determine if the preventative maintenance will create downtime or disruption.
Certain critical pieces of equipment are best serviced by the on-site technician team or contracted vendor after-hours or during off-peak times of operation.
Implement a Preventive Maintenance Program
The preventive maintenance database should be viewed as a framework that supports a certified facility manager’s overall process.
The implementation involves taking this compiled data and applying it.
The following list includes the four key actions to establishing the maintenance equipment or system implementation process:
- Create the schedule according to the specific recommendations of each item needing maintenance. Data regarding each piece of equipment is a key consideration including age, remaining years of service, rates of failure, etc.
- Obtain input and feedback from technicians who typically perform this type of work.
- Consider creating a system of labeling each piece of critical facility equipment.
- Document the amount of time that is usually required for maintaining each system or piece of equipment. This helps calculate the expected time needed to complete inspection, testing, or other maintenance tasks.
Remember, the preventive maintenance plan should be continually evolving and improving once implemented.
Even the most well-developed checklist will reveal some required updates or inefficiencies once put into practice.
Some Critical Characteristics of Effective Facility Maintenance
Successful facility maintenance experts increasingly demonstrate excellent listening and communication skills as a means of problem-solving.
The underlying concept of preventive maintenance today is based on gathering information, encouraging feedback, and understanding new technologies.
An effective facility manager understands the organization’s goals and communicates with staff, conducts research, and works with vendors and suppliers.
Now more than ever, effectively maintaining large commercial facilities requires these experts to use the latest technology.
Real-time monitoring of equipment, remote notifications, and integrating with a comprehensive facility management system are among the most critical.
Failing to embrace all the technology of today offers only hinders efficiency and is not cost-effective.
How Facilities Maintenance Can Maximize Value
To achieve value creation, property maintenance must strive to maximize the lifespan of the costly capital assets.
At the same time, efforts must be made to reduce expenses by limiting operational costs and increasing energy efficiency.
Today’s facility maintenance experts might consider contracting or outsourcing many of the operations within their scope of responsibility.
Exploring the possibilities of using third-party service providers is a viable part of a value-based strategy.
The Most Effective Facility Maintenance Provider
For many years now, facility and property management professionals have relied on the team at Servi-Tek Facility Solutions for their large commercial properties.
We offer customized facilities and engineering services for property managers, facility directors, and different buildings owners in dozens of leading industries.
We recognize that each commercial property has unique challenges, maintenance requirements, and operating budgets.
Our team has expertise in the maintenance and service of systems including HVAC units, electrical, plumbing, energy conservation, and many others.
Servi-Tek’s objectives in our contract facilities are to achieve optimal efficiency, reduce operating costs, and boost returns on investment.
With offices now located in Hawaii, Arizona, and Southern California, we look forward to the opportunity to partner with you.
Contact us today to discuss how we can help your organization achieve its facilities management objectives.
