The old saying “if it isn’t broken, don’t fix it”, doesn’t apply to routine maintenance of equipment in a commercial setting.
But then, why would you pay for equipment service if there isn’t anything wrong with it?
This article will clear all your queries and answer everything you need to know about establishing a preventative maintenance schedule and proper preventative maintenance planning, which play a major role in a facility’s efficiency, revenue, and development.
What is Equipment Maintenance?
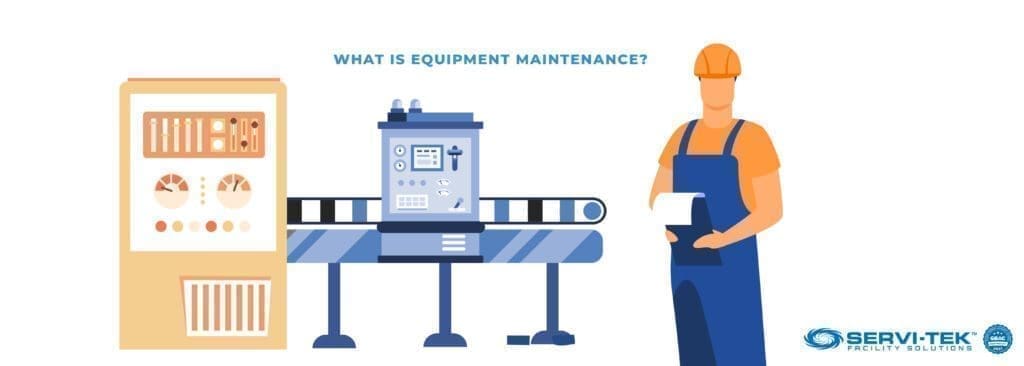
The term equipment generally refers to any articles, physical resources, devices, or tools used in operational performance or activity. In another different yet applicable context, the term describes the fixed assets of a business except for land or buildings.
Equipment is largely any resource that an organization or entity uses to conduct its necessary functions.
In a business context, the term maintenance refers to any acts of upkeep or preservation made involving property or equipment. Equipment maintenance might be performed by an internal member of an organization or an outside maintenance provider.
Today, equipment maintenance is an entire sector of the U.S. economy and is used throughout most industries.
It is a necessary process for the majority of U.S. businesses to keep activities going strong.
This work is performed on large mechanical assets needed for manufacturing, vehicles or may apply to electronic computer systems.
Maintenance activities can appear very differently, for example comparing work performed on the heavy construction equipment to that needed for sensors.
When it comes to this industry, here are some of the most common questions, answered:
How large is the U.S. market for repair and maintenance type services currently?
Estimates suggest the market size of Machinery Maintenance and Heavy Equipment alone is $34.3 billion and growing at nearly 3%.
What types of workers are employed in the U.S. equipment maintenance sector currently?
One example is an equipment maintenance technician, which is a worker responsible for the day-to-day maintenance tasks and duties. A technician will commonly perform diagnostic testing or inspections on specialized equipment or may operate in a general role.
A maintenance supervisor is someone that has some responsibility for oversight of the maintenance mechanics. This is largely a role filled by a seasoned maintenance technician that has performed well and been promoted.
They might have additional responsibilities such as compliance with health and safety guidelines and planning and scheduling duties.
An equipment maintenance manager has responsibility for oversight of maintenance supervisors and is normally a leader of the department. This individual is less involved in day-to-day service activity and more devoted to long-term departmental goals.
The role of a supervisor and a manager have some commonalities and they operate in clear succession.
What type of development, training, and certification is common or necessary among professionals working in this field?

The Society for Maintenance and Reliability Professionals offers a Certified Maintenance and Reliability Professional (CMRP) program that requires an examination.
The Association of Equipment Management Professionals offers the Equipment Management Specialist (EMS) and the Certified Equipment Manager (CEM) programs.
What are the activities comprising equipment maintenance?
Equipment repairs are considered a core activity among the various functions performed by all maintenance personnel. Repairs are responsive measures that require workers to correct a problem that may have rendered equipment inoperable. The type of repairs necessary to restore the equipment to the proper working condition may be apparent or might require a diagnosis.
The process of diagnosis could be compared to a patient who visits a doctor’s office for not “feeling well.” Here, the medical professional must make a diagnostic assessment before determining a proper remedy or solution. An equipment maintenance program requires identifying the source of the equipment breakdown and often making a part replacement.
Sometimes the notifications are sent to the maintenance managers in the form of work orders that report a problem. The response of the maintenance staff might be high-priority, requiring management to deploy available resources immediately.
Depending on the type of problem, technicians with some level of expertise may be necessary to make an accurate assessment.
Repairs can be simple or complex, such as breakdowns involving heavy machinery that requires strict manufacturer recommendations or input.
An off-site field service call may be necessary by mechanics with specialized training based on the overall complexity.
One example of an industry that relies heavily on regular maintenance is road construction, which uses costly assets. They use grading machines that have designated hourly maintenance intervals for supporting hydraulic and pneumatic components.
Some of the common maintenance tasks involve checking fluid levels, oil changes, grease, lubrication, replacement of filters and hoses, etc.
Why is Equipment Maintenance Important?
In some cases, proper maintenance is incorrectly viewed as a cost because it requires time, which equates to money. This type of thinking is simply bad for business, particularly when referring to very costly capital assets.
Preservation of the equipment used in a facility may be done according to a maintenance schedule based on compliance standards.
An example includes preventative maintenance needed for construction equipment involving regular inspections for coolant leaks, cracks, or proper calibration. In a manufacturing facility, proper maintenance is critical for avoiding potential periods of downtime, meaning production is halted.
Regular equipment maintenance is critically important to any successful operation. In today’s digital landscape, companies are investing in equipment maintenance software and employing predictive maintenance strategies coinciding with inventory management.
The following are six critical reasons why this activity is important, and how it can benefit you and your business.
Reduce Expenses
In a manufacturing environment, a problem with a machine that goes undetected may result in the creation of flawed products. The results of the output may be components or products that fail to meet specifications and must be scrapped.
What if a broken machine piece goes undetected for many days or weeks?
The manufacturer may have a significant amount of inventory or materials that are unable to be sold. This can create a “domino effect” when the flawed output is a necessary part while assembling another product.
Aside from lost productivity, the machine operator responsible for the equipment may need to stay after hours to work. This could push the worker’s weekly hours into overtime, meaning the employer is paying extra wages for that time as well.
WARRANTY COVERAGE RISKS
Improper maintenance practices could lead to ineligibility for warranty claims coverage from the supplier of a capital asset.
If a machine within the warranty period was not properly maintained and now needs a major repair, the supplier usually requests proper documentation showing the maintenance history.
This not only illustrates a potentially costly result of not adhering to maintenance procedures. It further shows the importance of clearly maintaining written documentation to support a potential warranty claim.
Overall, those with costly capital assets are always encouraged to make the effort needed to protect these investments.
Reduce the Risk of Accidents
Several reports issued by the International Journal of Occupational Safety and Ergonomics explained how unexpected equipment failures create accidents.
Researchers determined that roughly 35% of workplace incidents were related to failures of the equipment used in production.
The construction industry is a sector occupying a leading position in the total number of fatal workplace accidents.
In this field, many of the fatalities are linked to equipment failures, particularly those where maintenance practices were inconsistent. Accidents and injuries that result from poor equipment maintenance have been shown to persist despite having excellent safety training for workers.
The Occupational Safety and Health Administration (OSHA) is among the leading regulatory agencies involved in overall workplace accident prevention.
OHSA has determined that a strong correlation exists between poor maintenance standards and workplace injuries and fatalities. For this reason, equipment maintenance should be among the topics addressed in proper training for occupational safety practices.
Keep in mind, an active preventative maintenance program will never stop all unexpected problems, but failing to perform timely service invites only troubles.
Workplace injuries and accidents are not only tragic and harmful to workplace morale but are also potentially very expensive. Accident injuries and fatalities in occupational environments may create sharp increases in the rates you pay for worker’s compensation coverage.
Also, these accidents create opportunities for potential costly civil litigation in personal injury actions.
Maintenance failures involving occupational equipment have shown to be a risk to worker safety across dozens of other industries.
Reduce Breakdowns
When proper maintenance is not completed on assets such as machinery or tools, the result is increased failure rates. Workplaces that fail to properly service their equipment can expect to see a sharp rise in the number of breakdowns.
Often, by ignoring small or relatively minor maintenance tasks on a piece of equipment, you will only create larger problems. Here, the short-term savings earned by neglecting maintenance result in major financial calamities later.
Another thing to consider is that a major repair to a piece of equipment will require locating and obtaining a replacement part in a short time. The shipping costs and managing the entire operations equal more time and money wasted.
Equipment breakdowns resulting from inadequate maintenance practices demonstrate the importance of proper preventative maintenance.
Preventative maintenance is a term for describing the concept of adopting proactive maintenance and service practices.
Preventive contrasts with reactive maintenance, the latter causing an abrupt stoppage (downtime) and unexpected work for technicians to make repairs.
Make Equipment Last Longer
Machines contain a variety of different parts that sustain wear and tear over time including gaskets, bearings, and seals. These components require a proper inspection to assess their condition and replacement as necessary. Based on manufacturer recommendations, the specialists will perform service functions, which sometimes are based on the number of hours in operation.
Some types of capital assets purchased by the organization will eventually be upgraded in line with the latest technology.
The existing piece of equipment could be sold to another aftermarket user. The value of the asset for resale may reflect the quality of the maintenance performed and records documenting this activity.
REMEMBER THE IMPORTANCE OF CLEANING
One aspect of maintenance that is commonly overlooked or ignored is regularly cleaning the equipment. In many industrial work environments, these costly assets are exposed to soot, dust, and dirt. These airborne particles can adhere to moving parts and contaminate oils or lubricants and alter their viscosity.
Particles of dirt and dust may become logged-in filters, adhere to fans, and restrict airflow through vents. The result of neglect is that the equipment may be exposed to excessive heat. This is one factor that contributes to premature equipment failure, which could be prevented during the maintenance process.
Costly capital equipment has a life cycle that can loosely be classified into three phases new, middle-life, and end-of-life.
During the first phase, the organization makes a large investment and the equipment is expected to perform at peak efficiency. Problems that surface during the early period are typically the result of errors during installation or defective components.
During the middle phase, the equipment is expected to operate effectively and return some value for the organization’s investment. Proper maintenance is critical during this second phase to recover the initial cost of purchase.
Equipment performance in the final stage of life is largely based on the prior quality or lack of maintenance.
Increase Efficiency
During the first phase of a piece of equipment’s useful life, it will likely operate at optimal efficiency. To truly measure overall value, an asset’s level of efficiency is a critical factor. It is important to first define what efficiency is and how it is calculated.
Efficiency is a measure of how effectively a piece of equipment is operating compared to the critical costs. These costs include the amount of energy consumed and the time and money necessary for operation. In measuring energy efficiency, the value is compared proportionally to the energy and resources used.
As mentioned earlier, aging equipment and negative environmental factors generally combine to decrease the efficiency of operation. The piece of equipment may be using increasing levels of fuel, electricity, and other utilities and resources each day.
During the final phase of useful operating life, a poorly maintained piece of equipment will generally be very costly. This is the result of marginal production or output, increased consumption of energy, and rising maintenance costs.
In this case, major repairs and component replacements are likely and good managers recognize the significantly diminished value in its continued operation.
Improve Working Conditions for Employees
An overall correlation exists between an organization’s commitment to workplace maintenance and employee job performance and satisfaction. Not surprisingly, working each day in a disorganized, cluttered, or otherwise poorly-maintained setting is not good for morale. Employees operating in an environment clean, safe, and well-maintained are better positioned for occupational success.
Working with equipment that is routinely inoperable is both discouraging for employees and reflects poorly on the organization’s quality standards. Good equipment maintenance practices are centered on consistently and diligently doing the small things to achieve long-term success and value.
How can workers be expected to perform at a consistently high level within an organization operating to the contrary?
Many employees working in roles such as service and production have their performance evaluations based on efficiency and output.
In many cases, their performance level is dependent on having the tools and equipment needed. When maintenance is not prioritized, this will often create resentment because equipment performance is closely tied to achieving goals.
Organizations that fail to adopt proper standards and practices related to maintenance will eventually fail to deliver quality.
The same applies to a commercial provider of services, as low-quality work is inevitable when performed using poorly maintained tools. Employees prefer to take pride in the quality of the products or services that the organization creates or performs.
Maintenance failures often result in adverse economic consequences including stagnant wages, mediocre benefits, and other problems.
What Equipment Maintenance Involves
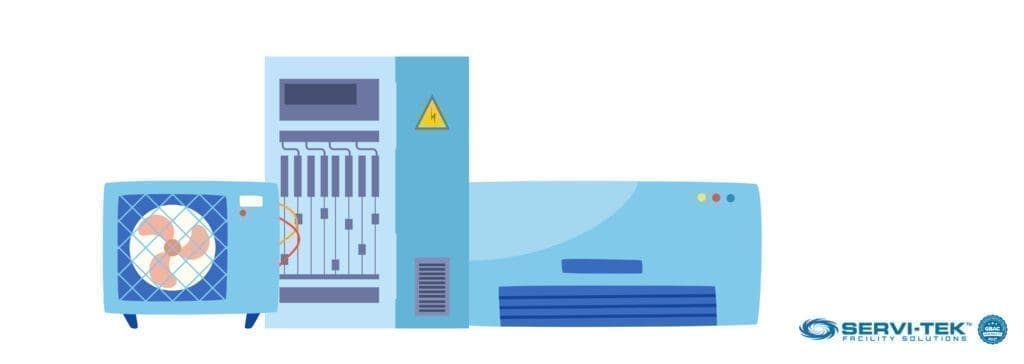
Equipment maintenance involves attempting to optimize the efficiency of operation and have high production quality.
New technology has enabled remote monitoring by using sensors to detect any irregularities in the status of the equipment. These remote monitoring capabilities complement the scheduled preventative maintenance activities such as cleaning, changing fluids, and other tasks.
Facility managers and maintenance personnel are tasked with establishing operational guidelines for achieving goals. It is important to remember that simply having sensors positioned to detect potential problems is insufficient by itself.
Technicians must also be trained to interpret the nature of any alert and have knowledge of how to react. Designated staff must have responsibility for this activity continuously throughout each day of active operations. This is part of a larger preventative maintenance workflow that is tested regularly to measure real-time performance.
Equipment Maintenance in the Workplace
Incorporating maintenance activity into the workplace creates the challenge of ensuring regular daily operations are not interfered with.
At the same time, maintenance tasks completed in a working environment may pose significant safety concerns. For example, maintenance staff might be challenged to perform functions in areas with limited space and among other workers.
Maintenance tasks frequently involve the possibility of human error while using tools to disassemble or otherwise make mechanical adjustments. Maintenance-related accidents and injuries are common and present a continual challenge for facilities managers.
Oftentimes, maintenance activity involves working with electricity, moving parts, and sometimes is conducted at potentially dangerous heights.
Although it may not always be possible, maintenance and facility managers should assess the various scenarios involved.
This might require assuming some “worst-case” scenarios, such as having maintenance performed during peak operating times with multiple mechanics. Outside contractors are generally needed for servicing certain specialized equipment.
Although less common in today’s safety-oriented industrial environment, maintenance activity can be a contributing factor to occupational disorders.
Examples may include exposure to agents that are a known risk for disease, sources of hearing loss, back problems, etc.
These risks must be acknowledged and minimized without ignoring the reality that maintenance tasks are vital to the organization’s success.
Why Regular Maintenance is Important
What are we specifically referring to when discussing the nature of routine or regular maintenance?
Usually, the term is describing time-based or “calendar-type” maintenance programs that are largely preventative. These are tasks based on a set schedule that dictates the timing common for maintaining capital assets.
For example, a technician will access the roof for an onsite inspection every 60 days. Heating and cooling components might be thoroughly inspected quarterly. The water filter leading into a production line may need to be replaced semi-annually.
Preventative maintenance can also be usage-based or based on operational runtime. For example, a construction transport vehicle requires certain maintenance tasks completed at a certain number of miles. A large piece of machinery in a manufacturing operation might need to have the coolant changed every 25,000 hours.
Preventative maintenance is also critical to limiting risks in the occupational setting, both those associated with people and property.
Machinery that may pose an injury risk to people requires regular safety-related inspections. This is similar to how a facility manager would inspect door locks, fire extinguishing equipment, and marked emergency exits.
Limiting risks to the property is at the core of a preventative maintenance strategy, particularly in contrast to a reactive strategy.
Here, putting together detailed written procedures and using a comprehensive checklist are two of the best practices for success.
How to Carry Out Regular Maintenance of Equipment
The maintenance needs of the facility should initially be determined and then the potential risks identified.
What are some of the key factors that could create risks when performing specific maintenance work?
Certain maintenance tasks might make a technician, for example, susceptible to electricity or expose them to fire or excessive heat.
Some types of equipment contain substances with potentially harmful chemical properties or may contain highly pressurized hot fluids.
Others can have moving parts that can strike a technician or become entangled with clothing, hair, or equipment. Certain types of equipment release dangerous emissions if an exhaust system suddenly fails.
Once all potential risks are identified, it is mandatory to incorporate this information into a diligent training program. Keep in mind that outside contractors are placed at risk if unaware of these concerns as well. A designated set of safety instructions should always be easily accessible for anyone involved in maintenance activity.
Another critical aspect of developing these safety-related concerns is determining when access to the maintenance area should be restricted.
It is a good idea to use visible signs; however, having a temporary physical obstruction in place is even better. Machine operators or others working in areas where maintenance will be conducted must always be notified in advance.
Regular Maintenance Checklist for Equipment
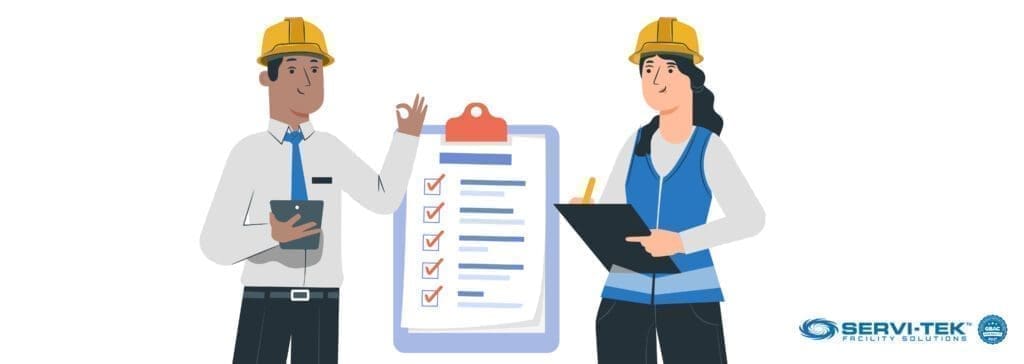
A facility maintenance safety plan should be accompanied by a checklist for simplifying and better organizing key information.
In today’s digital environment, this checklist should not be limited to some printed-out document in a binder. These documents should be available in an electronic format that is accessible to staff working in the field in real time.
You can find below a sample format to illustrate the concept of the maintenance checklist.
Lighting:
- Check the function of lighting used exclusively in cases of emergency.
- Inspect all lighting on the exterior of the premises.
- When replacing any lighting unit, record the date to gauge the longevity and frequency of replacement.
- Wiring and cabling should be checked for any evidence of wear or deterioration that could cause an outage or be hazardous.
HVAC:
- Clean and change all filters according to the schedule created by the manufacturer.
- Inspect blower motors during operation to detect any excessive vibration or irregular sounds.
- Check below the condensers for evidence of any excess accumulations of moisture that suggest possible damage or lead to mold growth.
- Physically test any pressurized tubing or hoses for potential holes or leaks.
Building Interior:
- Inspect floors and ceilings for any visible signs of leaking that may indicate problems.
- Test of all devices for detection of smoke or carbon monoxide.
- Look through storage or warehouse areas for evidence of pest intrusion.
- Check doorways for proper closure and any potential obstructions.
Building Exterior:
- Inspect the exterior foundation for any evidence of cracking or structural changes.
- The management of water is critical: always ensure gutters and drainpipes are clear and functional.
- Check for any backups or problems with storm drains.
- Inspect the exterior trash areas for infestations from rodents, birds, or insects.
Plumbing:
- Inspect the condition of any circulation pumping units.
- Test boilers and water heaters.
- Change any refrigerant per manufacturer guidelines.
- Check the functionality of pumps.
Maintenance Tips
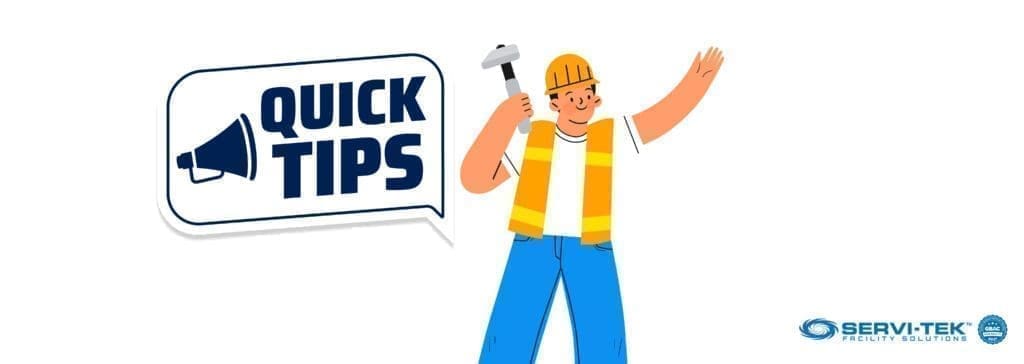
It is important to remain up to date with the maintenance plan schedule and prevent backlogs. When breakdowns occur, they must be well-documented and the cause identified.
Are these problems related to failures in maintenance?
Remain aware of when equipment is approaching the end of its useful service life and explore options including refurbishment or replacement.
Training technicians are among the most important aspects of any maintenance plan. Failures in initial or ongoing training practices are potentially dangerous and show a complete lack of responsibility.
Maintenance staff should have easy access to the producer’s manuals and guides for reference.
Emphasize the importance of proper documentation. This is crucial for warranty coverage, gauging job performance, and evaluating the long-term value of the equipment. Records should include key factors including hours of operation or mileage, age, and current condition.
Why is Equipment Maintenance So Vital?
Equipment maintenance is always critical for the safety of those operating in these environments. Failures in proper equipment or facility maintenance continue to be a source of workplace accidents, injuries, and fatalities.
This can contribute to increased costs of worker’s compensation, employee turnover, and potentially costly litigation.
Preventative or Planned Maintenance?
The answer to this question is both!
A well-designed equipment strategy is dependent on excellent preventative maintenance practices, which are created as a direct result of planning. Preventative maintenance is often completed based on the number of hours a piece of equipment is used.
Preventative maintenance may also be conducted based on regular time frames such as monthly, quarterly, annually, etc.
Another type of planned upkeep is often referred to as being pre-determined maintenance, which follows the manufacturer’s recommendations. These two strategies generally overlap because the manufacturer’s guidelines are likely a key consideration either way.
Maximize Your Productivity
Well-maintained equipment is necessary for the maximization of productivity, which refers to achieving peak operational efficiency.
Failing to regularly service heavily used equipment may not result in immediate reductions in productivity; however, it appears over time.
Many factors will potentially impact overall productivity.
First, the proper type of equipment or tools must be used for the job or activity. Following, the maintenance activities must be properly documented to track and perhaps prove that regular upkeep is being performed.
Limiting downtime is a leading goal for maximizing productivity, as unexpected stoppages for repairs halt output.
Reduce Risks
Reducing risks associated with equipment in a commercial setting involves a proactive process of accessing the potential dangers.
Once these dangers are identified, a customized strategy of prevention can be created. These include risks that place people at risk or those that create equipment failure and result in financial losses.
Increase the Safety of Your Workers
Worker safety must remain a priority in the realm of facility and equipment maintenance. Identifying hazards such as the possibility of being struck by moving equipment, electrocution, falls, and many more.
It is unreasonable to expect workers to deliver high performance and maintain job satisfaction when accidents and injuries are common.
Equipment Maintenance is a Priority for Business Efficiency
Commercial facility and maintenance managers that achieve ongoing success recognize how regularly servicing equipment heightens efficiency.
When equipment failures occur during daily operations the business will struggle to meet deadlines and demonstrate consistency.
Today, maintenance managers are encouraged to employ electronic systems that serve to centralize data, allow remote access, and ensure accountability.
The software that supports facility maintenance departments provides a framework for proper organization. Each asset must have a specific history documenting work orders, repairs, and maintenance, which are critical in assessing value.
A schedule of planned preventative maintenance should be accompanied by detailed standards and procedures for these activities.
The systems should also integrate with efforts related to predictive maintenance. This involves real-time monitoring, detection, and alerts that will deploy appropriate service and maintenance personnel.
Meanwhile, all warranty information, service agreements, and specifications needed for repairs and component replacement are always available for reference.
CONTACT AN EXPERIENCED PROVIDER OF EQUIPMENT AND FACILITY MAINTENANCE FOR LARGE COMMERCIAL ENVIRONMENTS TODAY
We are a team of highly trained professionals at Servi-Tek Facility Solutions, and we provide comprehensive services for organizations in many industries and sectors today.
Equipment maintenance is among the key offerings within our engineering service programs that keep facilities moving forward. We remain committed to the current best practices, the latest technology, and manufacturer service recommendations to optimize efficiency and create value.
We recognize that commercial organizations invest significant resources to acquire the tools and equipment necessary to achieve goals.
As a result, we create comprehensive preventative and predictive maintenance strategies that also minimize risk and protect worker safety.
Contact our office today to speak with one of our professionals regarding how we can be an asset to your organization.