The chiller is generally the building’s single greatest power user and most expensive piece of equipment. It makes sense to devote time and resources to energy efficiency and equipment maintenance.
What can you benefit from investing in a regular and professional maintenance schedule for your chiller? Find out below:
Why Is Chiller Maintenance Important?
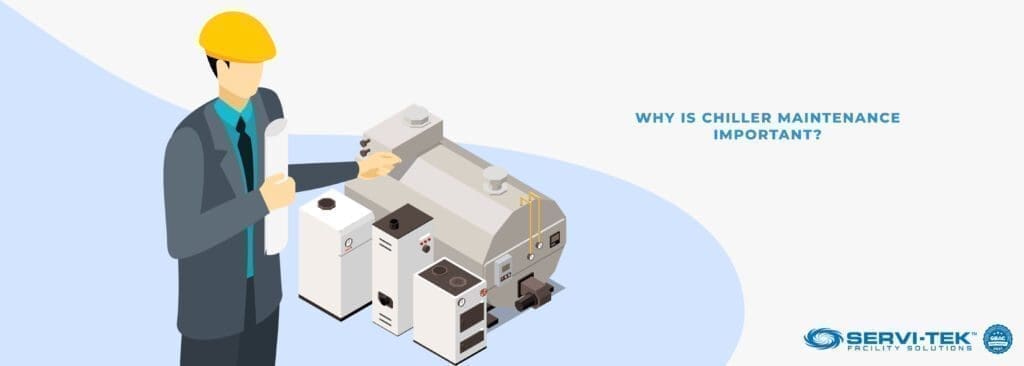
In a large facility with a centralized system, qualified technicians will manage chillers that are comprised of many parts.
Chillers are a critical aspect of the HVAC system that requires maintenance personnel to make inspections to ensure efficient operation.
Chiller manufacturers continue improving aspects of these systems including chiller efficiency, more advanced control panels, and variable speed drives.
Chiller maintenance must be done regularly to produce chilled water and fluids that can remove heat. Equipment used in file-server systems, medical imaging units, and many other costly assets may also depend on chillers.
Chillers are complex systems, therefore, chiller maintenance checklists must be developed with schedules and daily logs to organize critical tasks.
Regular maintenance examples include checking for any fluid leakages, replacing oil filters, reducing moisture, assessing water flow rates, refrigerant charges, etc.
Effective maintenance prevents costly repairs, damaging vibrations, corrosion, obstructed contactors, damaged coils, and broken condenser tubes. Fluid levels including water and compressor oil are checked and quality control samples often are sent to a laboratory.
In some cases, glycol or other additives are used to prevent freezes, sludge, and other contaminants. Checking refrigerant levels and performing chemical analysis of liquids can prevent blockages and tightness in pipes and condenser water loops.
Chiller maintenance is also important for compliance with the U.S. Environmental Protection Agency (EPA) that promotes energy efficiency. The EPA requires facilities to closely monitor components, perform sufficient preventative maintenance, and promptly take corrective measures.
EPA guidelines state that all chillers must be monitored for leaking refrigerant as part of the Clean Air Act.
The concern is particularly with the depletion of the earth’s ozone layer that results from unregulated flowing chemicals.
These measures were part of a broad scope of changes that included more rigid requirements for large appliance leaks. New documentation requirements called on all facilities to track any appliances that are disposed of having a 50-pound refrigerant capacity.
The Benefits of Chiller Maintenance
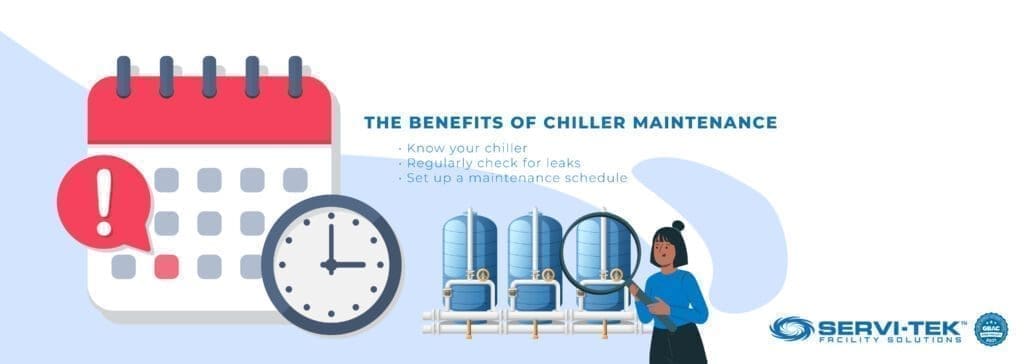
Facility management professionals today understand the critical importance of properly addressing chiller maintenance and service.
Maintenance failures tend to result in future problems that become increasingly more costly. Choosing to postpone maintenance is often the result of shortages in labor, financial resources, or simply not prioritizing the work.
The timeliness of the maintenance activity is the most critical aspect of the maintenance program. The plan is intended to be proactive rather than reactive, and a deferral runs completely contrary to the mission.
Here’s what you should consider in your chiller maintenance plan:
1: Know Your Chiller
Today, many facilities professionals are pondering whether to continue fixing and maintaining existing chiller systems or replacing them.
For example, the facility’s cooling needs, any space-related concerns, and available alternatives are all key factors that should apply. Maintenance professionals must research to determine the appropriate size and consider potential longer-term variables.
Taking advantage of the increased efficiency of a new machine is a clear incentive; however, load requirements are important too. Some facilities are relying on chiller-bank systems for minimizing run-time and optimizing the system during periods of reduced need.
Air-cooled chillers positioned in exterior areas may lack the efficiency of centrifugal chillers yet may reduce maintenance costs. Upgrades are another option, such as adding a variable-frequency drive, transitioning to a new piping layout, and reducing friction.
Changes are most common when systems are still expected to have at least five more years of good service. Often, building renovations, additions, new ownership, or new tenants will create a need or desire for a check-up.
Certain upgrades to existing systems are logical when they can reduce costs, such as adding insulation and adding timer units. In today’s digital environment, most managers have a reasonable expectation that systems have the capability of issuing real-time alerts.
2: Regularly Check for Leaks
The EPA published a section of guidelines for addressing leaks of refrigerant, specifically for industries including chemical, pharmaceutical, manufacturing, and more. They sought to address corrective measures to take when refrigerant that may be harmful to the environment leaks.
Leaks should never go more than 30 days without any fixing or a plan should be devised for retrofitting or disposal. Initial and ongoing testing is critical after repairs are made to confirm that the leak has been properly repaired.
Regularly checking for leaks is necessary for more reasons than simply to prevent environmental harm. The loss of refrigerant might stem from a damaged component and could pose risks for very costly repairs to a machine.
3: Set Up a Maintenance Schedule
Checklists are tools for assessment that maintenance professionals use to stay organized and ensure proper inspection intervals are met. The list is a critical part of any preventative maintenance plan for tasks including temperature checks and other measurements.
Among the most critical functions to be performed involves checking oil pressure and temperature gauges for any potential abnormalities. Chillers should be checked for any unusual noises, evidence of excessive vibration, and indications of friction.
Electrical panels should be checked and secured as well as any fire safety components and equipment as needed. An assessment may be needed to gauge high approaching temperatures, which compares the supplied water and recirculated return water.
Water system pretreatment is one potential solution when these large discrepancies exist or chiller tubes may need chemical treatment. It is common for scales, algae, and other miscellaneous contaminants to limit heat transfer and impair overall functionality.
Sometimes condenser pressure will noticeably increase over a period, which is often indicated in the rates of water flow. Most of the remedies to these problems involve recalibration of the control unit related to non-condensables, inlet blockage, and more.
Making Chiller Maintenance Less Expensive and More Effective
As a facility management professional, you should know that proper cleaning and maintenance help eliminate downtime and system repairs.
Chiller tubes, fins, condenser coils, and many other components are vulnerable to buildups of harmful deposits and sediment within the water.
Costs of deferring maintenance may not always be instantly apparent, however, they will surface at some future point. For this reason, the daily operations log is one of the best tools used to stay on task for maintenance professionals.
The costs of water treatment have partially been reduced due to improved formulas which prevent bacterial growth and contamination. Each system and premise have some unique combination of equipment, water quality, types of scale, that requires a specialized approach.
Categorize the Types of Problems You Are Having

Knowing what you are dealing with is the first, m=sometimes most important step in finding a solution.
One of the common problems involves high-pressure discharge, specifically in water-based cooling units. Often, this results from failures in water treatment, particularly among those with open cooling configurations.
Many people fail to realize that air contains tiny particles of dirt and minerals that enter the water system loop. Once these materials have breached the condenser loop, they will likely begin to create problems downstream stemming from obstruction.
These obstructions result as the materials travel through pipes and pass the heat exchanger segment. This creates an effect that disrupts thermal energy flow or transfer because the chiller has become insulated.
Air-cooled chillers inherently struggle with a reduced airflow, which also stems from obstructions in the condenser or sometimes the fans. Insufficient airflow results in increased heat, poor performance, and failure of components are likely.
Flow rates must be measured at different points throughout the system to better detect where obstructions occur. For example, pumps, strainers, and other components are all subject to potential problems with obstructed flow rates.
High-pressure discharges sometimes become evident when the water temperature is too high. If the cooling tower is unable to effectively operate, often a fan has failed.
The chiller’s shut-off valve should be checked to ensure it is not partly closed, which is much less common. Air-cooled chillers are also more susceptible to excessive environmental air temperatures that overwhelm the condenser’s abilities.
One mistake that is generally considered short-sighted is spraying the condenser with water to cool it down. This will ultimately lead to the buildup of deposits on the exterior of the condenser unit that will further impede performance goals.
In some instances, maintenance personnel might overcharge the system with refrigerant, which may generate excessively high pressure. This type of problem may be detected by regularly testing the temperature and listening for any audible indications of a problem.
Low-pressure discharge is often the result of a partly closed suction valve or simply an undercharged level of refrigerant. Similarly, to the previous scenario, having an ambient air temperature that is too low poses potential problems.
Although often not practical, heating the air can resolve the problem, such as by using ventilation air. Obstructions within the evaporator are also a likely source of problems that is evident when pressure is too low.
Again, the fundamentals of the process are also similar. A buildup or deposit in one part of the system creates a chain reaction of efficiency concerns down the line.
This might involve obstructions near the filter or strainer. In some cases, high suction pressure will be caused by a problem with the expansion valve.
The expansion valve might be generating too much refrigerant and need to be replaced. Instability in the voltage supply is another area of concern when it comes to chillers.
This occurs from an imbalance in the voltage supply that could involve the switch gears or another overall building power concern. When a voltage problem exists, it will generally hinder other parts of the system that are influenced by the faulty circuit.
In some rare cases, maintenance staff will fail to fully reconnect wires or cables during other types of service. This is most evident when the machine behaves unpredictably and requires systematically checking each connection.
Open breakers or blown fuses might also be to blame in these situations. Keep in mind that many chillers have a multi-phase supply and one part or phase could be faulty.
Ground-related problems are often to blame when the machine’s internal protection system automatically turns off. Any prolonged period of excessive heat can create very costly motor damage.
Stock Up on Repair Parts That Are Frequently Used

One of the leading causes of excessive downtime is not having access to the supply of parts necessary for executing a repair. Some debate on whether to stock a wide variety of spare parts on newer machines should be expected.
As machines begin to age, it is best to annually check on the status and availability of replacement parts. This can help to prevent unforeseen calamities and lengthy shutdowns.
Having a stock of parts can reduce this downtime and bring the machine back online much quicker. It is worth mentioning that a lack of spare parts also may encourage patchwork types of repairs that are harmful to the machine.
As with the majority of equipment, older machines often have hard-to-find parts when a machine is no longer being produced. Failing to maintain a supply of scarce parts also can extend downtime as technicians search to locate them.
Smart facility professionals will conduct some analysis to better determine when to begin stocking parts. Often, this is based on how dependent the operation is upon a specific machine for production.
Be Sure to Record All Chiller Problems
We stressed the importance of regular maintenance practices, but this aspect of operations must also be properly documented.
What good is a maintenance plan if there is no track record of any activity being performed?
In the absence of sufficient documentation maintenance tasks could unintentionally be repeated, overlooked, or some other related failures. Maintenance records are critical for evaluating staff performance and preventing potentially expensive repairs that may have been easily avoided.
A maintenance plan is only as good as the documentation you create both in establishing a plan and executing it.
Failures in documentation may also impact this area of the service and maintenance plan by being too disorganized. How would you know that a specific replacement part has been used and needs to be reordered without details?
Keeping It Simple – A Checklist for Chiller Maintenance

Following your maintenance checklist and documenting every activity is often critical for maintaining warranty coverage on a piece of equipment.
With no history to reference, you risk lacking any credible supportive documentation necessary for a claim. This might apply to warranties associated with repairs, replacement, reimbursement, and refunds that are made in writing.
Manufacturers must also adhere to the standards when it comes to their internal product development and testing of machines. Otherwise, the manufacturer would have no reasonable basis for recommending a service and maintenance schedule.
When a piece of equipment prematurely fails, documentation to support adherence to the maintenance recommendations is vital.
Having a detailed maintenance history containing the nature of each activity and the dates performed will eliminate any problems.
You’ll find below the ideal checklist for chiller maintenance, made easy:
1. Test Your Chiller
Medium to large facilities should have the technical personnel necessary for properly testing the chiller. Knowing the manufacturer’s performance parameters is critical for having a baseline and measuring results.
The testing will assess deviations between the parameters and the actual performance of the system. Some of the tools needed for testing may include a water flow meter and devices for analyzing power and measuring temperature.
2. Check the Condenser Coils
As accumulations of dust and debris develop on coils, it is time to clean them. A proactive approach is preferred, which must be balanced with safety and preventing damage.
Pressure washers are among the methods used for cleaning coils; however, they must be used cautiously. The pressure washer may deliver the water with too much force, which may damage the fins.
The key is to find a medium for cleaning coils that involves sufficient pressure—yet not excessive pressure.
Choose an appropriate chemical for cleaning that is safe for workers, effective, and eco-friendly. For example, very acidic agents may pose health risks and lead to coils erosion.
3. Clean the Water
When water is the liquid used for the cooling system, it must be filtered and clean.
Why? Because it contains excessive mineral content that is harmful to the system.
Corrosion and algae inhibitors are typically effective when placed in reservoirs. For example, adding glycol to the water creates a good solution.
A water filter is typically an option for most models of chillers. Water filters often do an excellent job of capturing unwanted debris; however, they can begin lowering performance if not regularly cleaned.
A good rule of thumb for water filters is to check them every month.
4. Clean the Chiller
Chillers must be regularly cleaned, particularly those equipped with cooling towers. Keep in mind that warm water may create algae in cooling tower systems.
The cooling tower is also potentially subjected to other environmental concerns that can create corrosion. For example, insects, pollen, and dust that are circulating could be accumulating and need to be cleaned away.
5. Clean the Air Filters
Filters are used to screen and capture the many impurities that pass through a system. The maintenance staff must generally remove it to adequately clean it.
Filters can be cleaned with a sufficiently powerful air pump and with or without a cleaning agent.
6. Clean the Condenser Fan
On some units, the fans are positioned on the top and might be accessible without completely removing them.
When you have to remove the fan, caution is needed to avoid bending the blades and altering the proper balance.
7. Clean the Booster Fans
Booster fans are often positioned at strategic locations through the system of ducts to boost airflow, particularly in remote areas. These fans, also referred to as inline duct fans, will require some source of electrical power.
8. Regulate the Condenser Water Temperature
Chiller unit efficiency and performance are closely related to maintaining consistent water temperatures. In some cases, the chilled water temperature is reduced when necessary to control excessive humidity.
The temperature of chilled water systems can be reset (adjusted) when necessary. Even changing the temperature by a couple of degrees can significantly impact the strain and efficiency of the compressor.
How Chiller Maintenance Saves You Time and Money
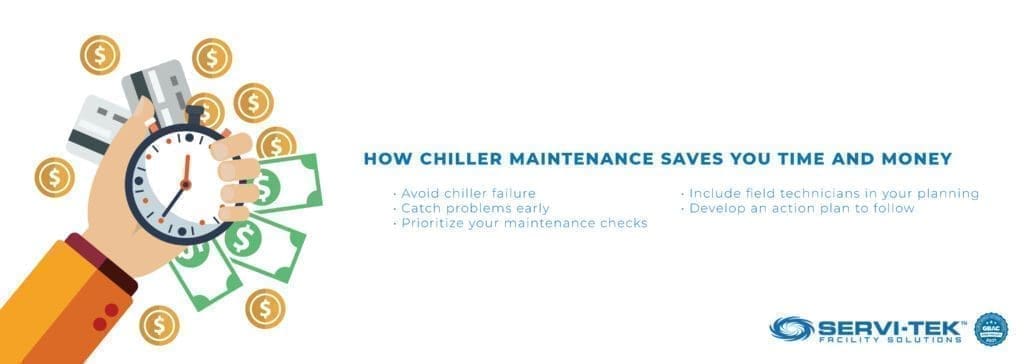
Diligently performing maintenance certainly increases the likelihood of saving time and money.
Saving time might also be measured in the amount of downtime avoided.
The savings component is clear when considering how a minor repair need that goes unnoticed often develops into more costly problems.
Regular maintenance also creates the potential for ongoing savings through reduced energy consumption and utility expenses.
Here’s how chiller maintenance saves you both time and money:
1: Avoid Chiller Failures
Chiller failures are commonly categorized as either being electrical or mechanical.
Electrical problems may stem from the incoming power supply or the internal electrical components of a system.
Mechanical failures might include a damaged bearing, valve, or shaft. Lubrication of moving parts is among the commonly overlooked aspects of preventing mechanical failures.
2: Use Preventive Maintenance to Catch Problems Early
Properly trained service technicians should approach preventative maintenance using a diagnostic and comprehensive view. This is necessary for properly recognizing relatively minor problems that the control system might not.
Too often, those performing the maintenance simply focus on the reading such as pressure and flow. Here, they may overlook many potential mechanical problems that might need to be seen or heard to be recognized.
3: Prioritize Your Maintenance Checks
Despite placing tremendous emphasis on adherence to the maintenance schedules and checklists, often tasks must be prioritized.
It involves identifying the most pressing concerns first and placing others on the list accordingly.
In many cases, the most important task is very clear, such as the immediate need to replace parts.
Priorities are also subject to change, such as being upgraded or downgraded. The reprioritization might be motivated because new information has emerged or because of input from management.
4: Include Field Technicians in Your Planning
As was previously mentioned, keeping field maintenance technicians “in the loop” is critical. This involves both consistent communication and training that encourages their understanding of the broad scope.
Field technicians often must also prioritize their maintenance activities in real-time. These decisions might be based on an immediate safety concern or simply recognition of a needed repair amid preventative activity.
Field technicians also have to accurately report and document their activities. The effectiveness of a maintenance reporting system with tremendous capabilities is still dependent on the quality of the information entered.
5: Develop an Action Plan to Follow
Some of the elements of an effective action plan include:
- Identifying ways to quantify the benefits of an effective maintenance plan such as the cost of one hour of downtime, the added savings of extending the serviceable lifespan of a piece of equipment, etc.;
- Having different maintenance activities synchronized such as between regular preventative activity, immediate work orders, and activity related to purchasing of supplies;
- The ability to monitor and track key performance indicators (KPIs) i.e., planned maintenance percentage, plant uptime, downtime percentages, or emergency maintenance percentages.
Additional Tips
These easy to follow tips are the extra information you need to make sure your chiller runs smoothly at all times:
Tip 1: Install Quick Drain Valves
Using quick drain valves may be used for rapidly removing water from the system for repairs or maintenance as needed. Drain valves are commonly added to the bottom of the evaporator box and usually have a shutoff valve.
Tip 2: Brush Down Coils
Coils are used in the heat exchange process, typically on the evaporator and condenser, and must be cleaned for optimal performance. The common cleaning options include compressed air and soft bristle brushes.
Failures to clean coils result in excessive heat that may cause damage to components over a period.
Tip 3: Calibrate the Refrigerant Charge
Careful calibration is required regarding how much refrigerant moves through the compressor for maximum efficiency. When the refrigerant charge is too low, the compressor will be required to work much harder and will likely be less effective.
Refrigerant leaks should be quickly detected and air and moisture entry into the system minimized.
Keep in mind that EPA guidelines continue to expand regarding the use of refrigerants and should be followed and updated.
Experienced Provider of Commercial Facility Maintenance Services
At Servi-Tek Facility Solutions, we are here to help you! How do we do that?
We place your needs first, as we handle your problems so you can manage your business, free of hassle.
We provide comprehensive commercial facility maintenance services, which include maintaining today’s chiller systems in top shape.
We strive to maximize energy efficiency, extend the life of equipment, limit downtime, and many other benefits for our clients.
We encourage you to contact us today for a free consultation.